Catalog excerpts
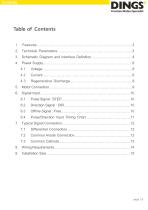
Schematic Diagram and Interface Definition………………….…………..4
Open the catalog to page 2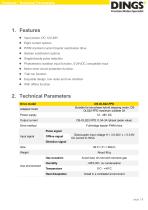
Features / Technical Parameters 1. Features Input power: DC 12V-48V Eight current options PWM constant current bipolar subdivision drive Sixteen subdivision options Single/double pulse selection Photoelectric isolation input function, 5-24VDC compatible input Motor short circuit protection function Trial run function Exquisite design, low noise and low vibration With offline function 2. Technical Parameters Drive model DS-OLS22-FPD Suitable for two-phase hybrid stepping motor, DSOLS22-FPD maximum suitable 3A Adapted motor Power supply Output current DS-OLS22-FPD: 0.3A-3A...
Open the catalog to page 3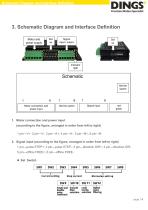
Schematic Diagram and Interface Definition 3. Schematic Diagram and Interface Definition Motor and power supply Signal input / output Indicator light 6 Motor connection and power input 1. Motor connection and power input (according to the figure, arranged in order from left to right) 1 pin---V+, 2 pin---V-, 3 pin---A+, 4 pin---A-, 5 pin---B+, 6 pin---B2. Signal input (according to the figure, arranged in order from left to right) 1 pin---pulse STEP+, 2 pin---pulse STEP-, 3 pin---direction DIR+, 4 pin---direction DIR5 pin---offline FREE+, 6 pin---offline FREE Set Switch
Open the catalog to page 4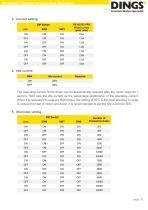
Schematic Diagram and Interface Definition 3. Current setting DIP Switch SW1 DS-OLS22-FPD Phase current (peak value) Idle current The operating current of the driver can be automatically reduced after the motor stops for 1 second. SW4 sets the idle current as the percentage relationship of the operating current. When it is necessary to output a high torque, the setting of 90% is the most effective. In order to reduce the heat of motor and driver, it is recommended to set the idle current to 50%. 5. Microstep setting DIP Switch SW5
Open the catalog to page 5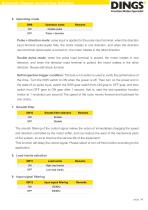
Schematic Diagram and Interface Definition Operation mode Double pulse Pulse + direction mode: pulse input is applied to the pulse input terminal, when the direction input terminal optocoupler fails, the motor rotates in one direction, and when the direction input terminal optocoupler is turned on, the motor rotates in the other direction. Double pulse mode: when the pulse input terminal is pulsed, the motor rotates in one direction, and when the direction input terminal is pulsed, the motor rotates in the other direction. Reuse self-check function Self-inspection trigger condition: The...
Open the catalog to page 6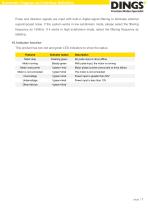
Schematic Diagram and Interface Definition Pulse and direction signals are input with built-in digital signal filtering to eliminate external superimposed noise. If the system works in low subdivision mode, please select the filtering frequency as 150kHz. If it works in high subdivision mode, select the filtering frequency as 500KHz. 10. Indicator function This product has two red and green LED indicators to show the status: Features Indicator status Motor stop Flashing green Motor running Steady green With pulse input, the motor is running Motor overcurrent Motor phase current overcurrent...
Open the catalog to page 7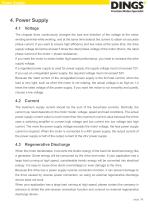
Power Supply The chopper drive continuously changes the size and direction of the voltage at the motor winding terminal while working, and at the same time detects the current to obtain an accurate phase current. If you want to ensure high efficiency and low noise at the same time, the drive supply voltage should be at least 5 times the rated phase voltage of the motor (that is, the rated phase current of the motor × phase resistance). If you need the motor to obtain better high-speed performance, you need to increase the drive supply voltage. If a regulated power supply is used for power...
Open the catalog to page 8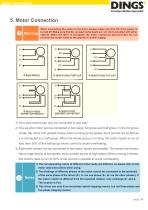
Motor Connection 5. Motor Connection Warning When connecting the motor to the drive, please make sure that the drive power is turned off. Make sure that the unused motor leads are not short-circuited with other objects. When the drive is energized, the motor cannot be disconnected. Do not connect the motor leads to the ground or power supply. 1) Four-wire motors can only be connected in one way. 2) The six-wire motor can be connected in two ways: full group and half group. In the full group mode, the motor has greater torque when running at low speed, but it cannot run as fast as it is...
Open the catalog to page 9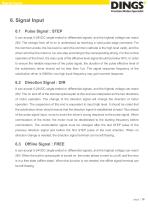
Signal Input Pulse Signal : STEP It can accept 5-24VDC single-ended or differential signals, and the highest voltage can reach 26V. The change from off to on is understood as receiving a valid pulse edge command. For the common anode, the low level is valid (the common cathode is the high level valid), and the driver will drive the motor to run one step according to the corresponding timing. For the normal operation of the driver, the duty cycle of the effective level signal should be below 50%. In order to ensure the reliable response of the pulse signal, the duration of the pulse...
Open the catalog to page 10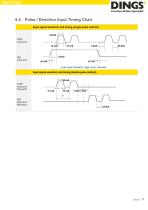
Signal Input Pulse / Direction Input Timing Chart Input signal waveform and timing (single pulse method) STEP Input port Input signal waveform and timing (double pulse method) STEP Input port (Forward) DIR Input port (Reverse)
Open the catalog to page 11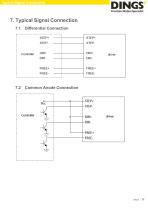
Typical Signal Connection 7. Typical Signal Connection 7.1 Differential Connection Common Anode Connection
Open the catalog to page 12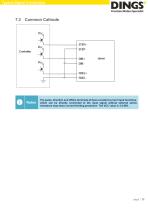
Typical Signal Connection Common Cathode The pulse, direction and offline terminals all have constant current input functions, which can be directly connected to the input signal without external series resistance step-down current-limiting protection. The VCC value is 3.5-26V.
Open the catalog to page 13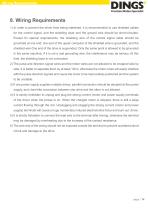
Wiring Requirements 8. Wiring Requirements 1) In order to prevent the driver from being interfered, it is recommended to use shielded cables for the control signal, and the shielding layer and the ground wire should be short-circuited. Except for special requirements, the shielding wire of the control signal cable should be grounded at one end: one end of the upper computer of the shielded wire is grounded, and the shielded wire One end of the drive is suspended. Only the same point is allowed to be grounded in the same machine. If it is not a real grounding wire, the interference may be...
Open the catalog to page 14All Jiangsu DINGS' Intelligent Control Technology Co. catalogs and technical brochures
-
General Catalog
295 Pages
-
Simple Brochure
36 Pages
-
DS-BVS-FETC-FCAO_Hardware Manual
18 Pages
-
DS-BVS-BVM-Series_Reference Manual
181 Pages
-
DINGS Servo Studio Manual
57 Pages
-
DS-BVM-FETC-FCAO_Hardware Manual
15 Pages
-
DS-OL42-ICAO_Technical Manual
53 Pages
-
DS-CLS9-FETC-2I_Technical Manual
43 Pages
-
DS-CLS9-FETC-2A_Technical Manual
43 Pages
-
DS-CLS9-FETC_Technical Manual
17 Pages
-
DS-CLS9-FCAO_Technical Manual
59 Pages
-
DS-OLS10-FSC_Technical Manual
12 Pages
-
DS-OLS8-FRS4_Technical Manual
30 Pages
-
DS-OLS7-FRS4_Technical Manual
29 Pages
-
DS-OLS8-FPD_Technical Manual
16 Pages
-
DS-OLS4-FPD_Technical Manual
17 Pages
-
DS-OLS2-FPD_Technical Manual
16 Pages
-
DS-CLS9-FRS4_Technical Manual
21 Pages
-
DS-CLS9-FRS4-01_Technical Manual
29 Pages