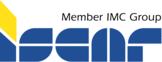
Catalog excerpts
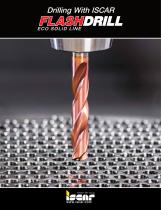
Drilling With ISCAR
Open the catalog to page 1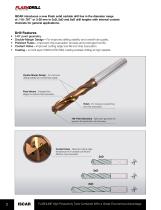
ISCAR introduces a new Flash solid carbide drill line in the diameter range of .118-.787” or 3-20 mm in 3xD, 5xD and 8xD drill lengths with internal coolant channels for general applications. Drill Features 140° point geometry. Double-Margin Design – For improved drilling stability and overall hole quality. Polished Flutes – Improved chip evacuation process and prolonged tool life. Coolant Holes – Improved cutting edge tool life and chip evacuation. Coating – A multi-layer IC608 (AlTiCrSiN) coating enables drilling at high speeds. Double-Margin Design - For improved drilling stability and...
Open the catalog to page 2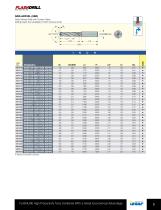
SCD-ACP3FL (3XD) Solid Carbide Drills with Coolant Holes, Drilling Depth 3xD (Available in North America Only) PL 140° DCm7
Open the catalog to page 3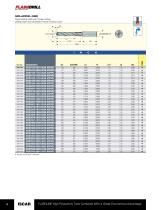
SCD-ACP5FL (5XD) Solid Carbide Drills with Coolant Holes, Drilling Depth 5xD (Available in North America Only) PL DCONMS h6 FLASHLINE High Productivity Tools Combined W ith a Great E conomical Advantage
Open the catalog to page 4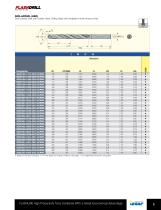
Solid Carbide Drills with Coolant Holes, Drilling Depth 8xD (Available in North America Only) • Based on DIN 6537 standard • For user guide and cutting conditions, see pages • For regrinding instructions, see pages
Open the catalog to page 5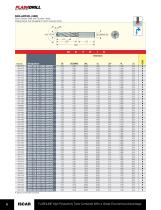
Solid Carbide Drills with Coolant Holes, Drilling Depth 3xD (Available in North America Only) PL 140° DCm7 FLASHLINE High Productivity Tools Combined W ith a Great E conomical Advantage
Open the catalog to page 6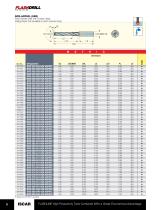
Solid Carbide Drills with Coolant Holes, Drilling Depth 5xD (Available in North America Only) PL 140° DCm7
Open the catalog to page 8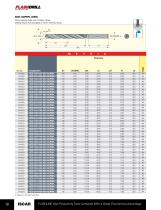
SCD-ACP8FL (8XD) Solid Carbide Drills with Coolant Holes, Drilling Depth 8xD (Available in North America Only) PL DCONMS h6 FLASHLINE High Productivity Tools Combined W ith a Great E conomical Advantage
Open the catalog to page 10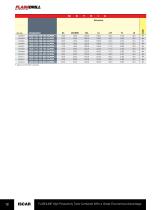
FLASHLINE High Productivity Tools Combined W ith a Great E
Open the catalog to page 12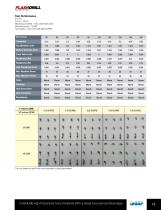
Tool Performance Ø 7mm D.O.C – 25mm Machining material – Alloy steel AISI 4340 Machine power – 22KW Tool Tested - SCD 070-028-080 ACP3FL Chip Evacuation Chip Formation The tool performs well in all recommended cutting parameters FLASHLINE High Productivity Tools Combined W ith a Great E conomical Advantage
Open the catalog to page 13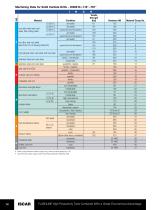
Machining Data for Solid Carbide Drills - IC608 D=.118”-.787” I Material non-alloy steel and cast steel, free cutting steel Condition annealed annealed quenched and tempered annealed quenched and tempered annealed P low alloy and cast steel (less than 5% of alloying elements) high alloyed steel, cast steel and tool steel stainless steel and cast steel M stainless steel and cast steel gray cast iron (GG) K nodular cast iron (GGG) malleable cast iron aluminum-wrought alloys ≤12% Si aluminum-cast alloys N copper alloys non metallic Fe based high temperature alloys S titanium alloys hardened...
Open the catalog to page 14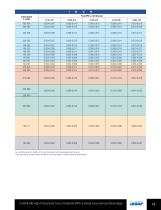
Feed (IPR) vs. Drill Diameter As a starting value, the middle of the recommended machining range should be used. Then, (according to wear results), conditions can be changed in order to optimize performance. FLASHLINE High Productivity Tools Combined W ith a Great E conomical Advantage
Open the catalog to page 15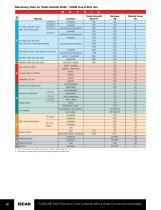
Machining Data for Solid Carbide Drills - IC608 D=3.0-20.0 mm M Material non-alloy steel and cast steel, free cutting steel Condition annealed annealed quenched and tempered annealed quenched and tempered annealed P low alloy and cast steel (less than 5% of alloying elements) high alloyed steel, cast steel and tool steel stainless steel and cast steel M stainless steel and cast steel gray cast iron (GG) K nodular cast iron (GGG) malleable cast iron aluminum-wrought alloys ≤12% Si aluminum-cast alloys N copper alloys non metallic Fe based high temperature alloys S titanium alloys hardened...
Open the catalog to page 16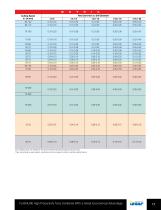
Cutting Speed Vc (m/min) As a starting value, the middle of the recommended machining range should be used. Then, (according to wear results), conditions can be changed in order to optimize performance. FLASHLINE High Productivity Tools Combined W ith a Great E conomical Advantage
Open the catalog to page 17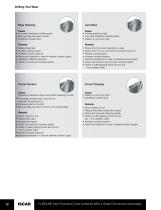
Drilling Tool Wear Edge Chipping Land Wear Cause • Low wear resistance carbide grade. • Built-up edge has been formed. • Insufficient coolant fluid. Cause • Cutting speed too high. • Low wear resistance carbide grade. • Radial run-out is too high. Remedy Reduce feed rate. Increase cutting speed. Increase coolant pressure. Improve jet direction in case of external coolant supply. Change to different geometry. Check tool and part clamping rigidity. Corner Fracture Corner Chipping Cause Caused by excessive edge wear before replacing the drill • The grade and geometry could be too weak for the...
Open the catalog to page 18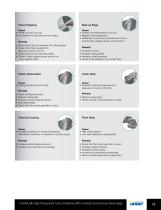
Chisel Chipping Cause • Chisel run-out is too big. • Combination of high feed and low speed. Remedy • Reduce feed rate and increase the cutting speed. • Check that chisel misalignment does not exceed 0.02 mm. • Check tool and part clamping rigidity. • Check if collet gripping forces are too low - if so, replace collet. Built-up Edge Cause • Cutting zone temperature is too low. • Negative cutting geometry. • Machining of very sticky materials such as lowcarbon steel, stainless steels, and aluminum. Remedy • • • • Plastic Deformation Cause • Cutting temperature is too high. Increase the feed....
Open the catalog to page 19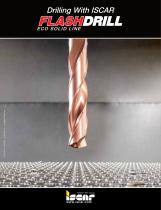
3425134 G 05/2022 © ISCAR LTD All Rights Reserved Drilling With ISCAR
Open the catalog to page 20All Iscar Metals catalogs and technical brochures
-
HOLEMAKING LINES
628 Pages
-
ISCAR TURNING LINES
939 Pages
-
ISCAR MILLING LINES
879 Pages
-
ISCAR New Products 2024
132 Pages
-
FLASH TOOLING
18 Pages
-
FLASH SOLID
80 Pages
-
THREADING LINES
484 Pages
-
DEEP DRILLING LINES
160 Pages
-
FACE GROOVING LINES
185 Pages
-
MACHINING ALUMINUM
172 Pages
-
MULTI-MASTER LINES
112 Pages
-
Barrel Shaped Endmills
20 Pages