Catalog excerpts
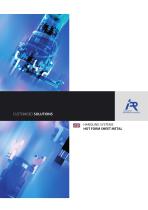
CUSTOMISED SOLUTIONS HANDLING SYSTEMS HOT FORM SHEET METAL
Open the catalog to page 1
Content Handling System for Hot Form Sheet Metal Describtion Page 3. Tool Changer Tool Changer TK-125-R 3.1 4. Components for Gripper Frames Connection Base for single Main Pipe HF-AP01-125/160 4.1 Connection Base for double Main PipeHF-AP02-125/160 4.2 Single Stand Pipe HF-SR50/30-01-... 4.6 Double Stand Pipe HF-SR50/30-02-... 4.7 Suction Cup Bearing Standard HF-SA01 4.22 Suction Cup Bearing Spring Loaded HF-SA02 4.23 IPR - Intelligente Peripherien fur Roboter GmbH IndustriestraUe 29 D-74193 Schwaigern subject to change without notice
Open the catalog to page 2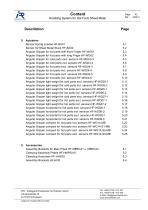
Content Handling System for Hot Form Sheet Metal Describtion Page 5. Actuators Sensor Spring Loaded HF-BA01 5.1 Sensor for Sheet Metal Stuck HF-BA02 5.2 Angular Gripper for hot parts with short Finger HF-WG01 5.3 Angular Gripper for hot parts with long Finger HF-WG02 5.4 Angular Gripper for cold parts excl. sensors HF-WG03-3 5.5 Angular Gripper for cold parts incl. sensors HF-WG03-4 5.6 Angular Gripper for hot parts excl. sensors HF-WG04-3 5.7 Angular Gripper for hot parts incl. sensors HF-WG04-4 5.8 Angular Gripper for hot parts excl. sensors HF-WG04-5 5.9...
Open the catalog to page 3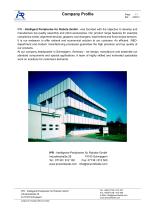
Company Profile Page: 1.1 IPR - Intelligent Peripheries for Robots GmbH - was founded with the objective to develop and manufacture top quality assembly and robot accessories. Our product range features for example compliance wrists, alignment devices, grippers, tool changers, load limiters and force-torque sensors. It is our endeavor to offer rational and economical solution to our customer. An efficient R&D-department and modern manufacturing processes guarantee the high precision and top quality of our products. At our company headquarter in Schwaigern, Germany - we design, manufacure...
Open the catalog to page 4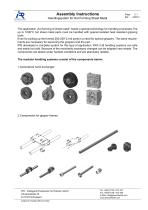
Assembly Instructions Handlingsystem for Hot Forming Sheet Metal The application „hot forming of sheet metal“ needs a special technology for handling processes.The up to 1000°C hot sheet metal parts must be handled with special isolated heat resistant gripping tools. Even for picking up the formed 200-250°C hot parts is a need for special grippers. The same requirements are necessary for sensoring the grippers and the part. IPR developed a complete system for this type of application. With it all handling systems can safe and easily be build. Because of the modularity necessary changes can...
Open the catalog to page 5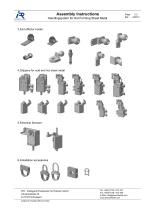
Assembly InstructionsHandlingsystem for Hot Forming Sheet Metal Page: 2.2 4.Grippers for cold and hot sheet metal IPR - Intelligente Peripherien fur Roboter GmbH IndustriestraUe 29 D-74193 Schwaigern subject to change without notice
Open the catalog to page 6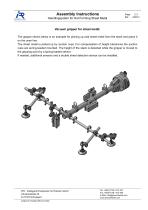
Assembly Instructions Handlingsystem for Hot Forming Sheet Metal Vacuum gripper for sheet metal: The gripper shown below is an example for picking up cold sheet metal from the stack and place it on the oven line. The sheet metal is picked up by suction cups. For compensation of height tolerances the suction cups are spring-loaded mounted. The height of the stack is detected while the gripper is moved to the gripping point by a spring-loaded sensor. If needed, additional sensors and a double sheet detection sensor can be installed. IPR - Intelligente Peripherien für Roboter GmbH...
Open the catalog to page 7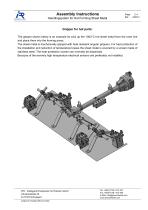
Assembly Instructions Handlingsystem for Hot Forming Sheet Metal Gripper for hot parts: The gripper shown below is an example for pick up the 1000°C hot sheet metal from the oven line and place them into the forming press. The sheet metal is mechanically gripped with heat resistant angular grippers. For heat protection of the installation and reduction of temperature losses the sheet metal is covered by a screen made of stainless steel. The heat protection screen can normally be dispensed. Because of the exremly high temperature electrical sensors are preferably not installed. IPR -...
Open the catalog to page 8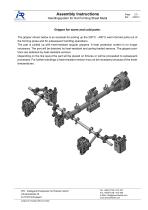
Assembly Instructions Handlingsystem for Hot Forming Sheet Metal Gripper for warm and cold parts: The gripper shown below is an example for picking up the 200°C - 400°C warm formed parts out of the forming press and for subsequent handling operations. The part is picked up with heat-resistant angular grippers. A heat protection screen is no longer necessary. The part will be detected by heat-resistant and spring-loaded sensors. The gripper positions are detected by heat-resistant sensors. Depending on the line layout the part will be placed on fictures or will be proceeded to subsequent...
Open the catalog to page 9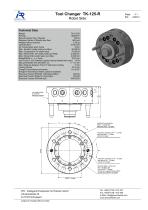
Tool Changer TK-125-R Robot Side Page: 3.1 Technical Data Modell TK-125-R Distance Center of Gravity less than 500 mm Weight (without options) 3,55 kg Air Consumption each Cycle 0,59 l Max. Tensile Fz(static load) at p=6bar 30.000 N Max. Compressive Fd (static load) 70.000 N Max. Moment Mx, My (static load) at p=6bar 2.000 Nm Max. Moment Mz (static load) at p=6bar 2.000 Nm Join Force in Join Direction (against spring loaded ball cover) 110 N Max.permissible Axis Deviation x/y +/- 1,6 mm Max. Distance between R and T Side when locking 3 mm Energie...
Open the catalog to page 10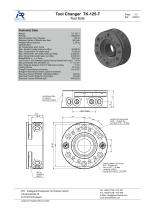
Tool Changer TK-125-T Tool Side Page: 3.2 Technical Data Modell TK-125-T Distance Center of Gravity less than 500 mm Weight (without options) 2,25 kg Air Consumption each Cycle - Max. Tensile Fz(static load) at p=6bar 30.000 N Max. Compressive Fd (static load) 70.000 N Max. Moment Mx, My (static load) at p=6bar 2.000 Nm Max. Moment Mz (static load) at p=6bar 2.000 Nm Join Force in Join Direction (against spring loaded ball cover) 110 N Max.permissible Axis Deviation x/y +/- 1,6 mm Max. Distance between R and T Side when locking 3 mm Energie...
Open the catalog to page 11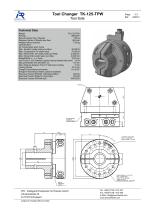
Tool Changer TK-125-TPWTool Side Page: 3.3 Technical Data Modell TK-125-TPW Distance Center of Gravity less than 500 mm Weight (without options) 7,55 kg Air Consumption each Cycle - Max. Tensile Fz(static load) at p=6bar 30.000 N Max. Compressive Fd (static load) 70.000 N Max. Moment Mx, My (static load) at p=6bar 2.000 Nm Max. Moment Mz (static load) at p=6bar 2.000 Nm Join Force in Join Direction (against spring loaded ball cover) 110 N Max.permissible Axis Deviation x/y 1,6 mm Max. Distance between R and T Side when locking 3 mm Energie Transmission...
Open the catalog to page 12All IPR - Intelligente Peripherien für Roboter GmbH catalogs and technical brochures
-
new products
6 Pages
-
7th axis for small robots
2 Pages
-
Robot 7th-Axis
10 Pages
-
IPR Product range
24 Pages
-
Gripping technology catalogue
386 Pages
-
Robot gantry
5 Pages
-
Tool changer
10 Pages
Archived catalogs
-
Robotic peripherals
5 Pages
-
Solar
3 Pages
-
Cavity waxing
4 Pages
-
Hot forming sheet metal
62 Pages
-
Robot 7th axis
6 Pages
-
Special grippers
4 Pages