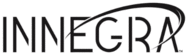
Catalog excerpts
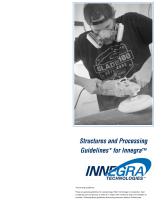
Structures and Processing Guidelines1 for Innegra™ innb($r3} TECHNOLOGIES™ Processing Guidelines These are general guidelines for using Innegra Fiber Technology in composites. Each composite part and process to make it is unique with numerous steps and variables to consider. Following these guidelines does not guarantee a perfect, finished part.
Open the catalog to page 1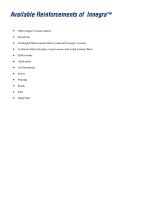
• 100% Innegra™ S woven fabrics • Spread tow • Co-Mingled fabrics (woven fabrics made with Innegra™ H yarns) • Co-Woven fabrics (Innegra™ S yarns woven with a high modulus fiber) • Multi-axials • Uni-Directionals • Scrims • Prepregs • Braids • Knits • Staple
Open the catalog to page 2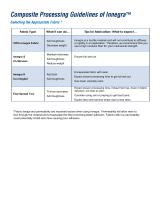
Fabric design and permeability are important factors when using Innegra. Permeability will allow resin to flow through the material and encapsulate the fiber promoting better adhesion. Fabrics with low permeability could potentially inhibit resin flow causing poor adhesion.
Open the catalog to page 3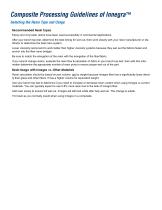
Composite Processing Guidelines of Innegra™ Selecting the Resin Type and Usage Recommended Resin Types Epoxy and vinyl ester resins have been used successfully in commercial applications. After your bench top test, determine the best timing for wet out, then work closely with your resin manufacturer or distributor to determine the best resin system. Lower viscosity resins tend to work better than higher viscosity systems because they wet-out the fabrics faster and anchor into the fiber nano-bridges. Be sure to match the elongation of the resin with the elongation of the fiber/fabric. If you...
Open the catalog to page 4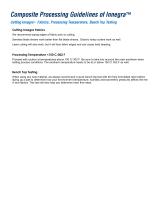
Composite Processing Guidelines of Innegra™ Cutting Innegra™ Fabrics, Processing Temperature, Bench Top Testing Cutting Innegra Fabrics We recommend taping edges of fabric prior to cutting. Serrated blade shears work better than flat blade shears. Electric rotary cutters work as well. Laser cutting will also work, but it will fuse fabric edges and can cause hard beading. Processing Temperature <150 C/302 F Proceed with caution at temperatures above 150 C/ 302 F. Be sure to take into account the resin exotherm when setting process conditions. The exotherm temperature needs to be at or below...
Open the catalog to page 5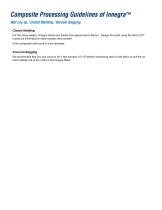
Composite Processing Guidelines of Innegra™ Wet Lay up, Closed Molding, Vacuum Bagging Closed Molding For the same weight, Innegra fabrics are thicker than glass/carbon fabrics. Design the mold using the fabric CPT (cured ply thickness) to obtain proper resin content. Over compaction will result in a dry laminate. Vacuum Bagging We recommend that you pull vacuum for a few minutes (10-15) before introducing resin to the fabric to pull the air and moisture out of the voids in the Innegra fibers.
Open the catalog to page 6All Innegratech catalogs and technical brochures
-
Corporate Presentation
24 Pages