
Catalog excerpts
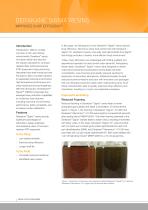
DERAKANE SIGNIA RESINS ™ IMPROVED SHOP EFFICIENCY Introduction Introduced in 1965 to combat corrosion in hot, wet chlorine environments, Derakane™ epoxy vinyl ester resins have become the industry standard for corrosionresistant fiber reinforced polymer (FRP) equipment. High performing derivatives have been introduced over the years to allow vinyl ester solutions for expanded chemical environments, high temperature performance and areas requiring improved toughness. With the introduction of Derakane™ Signia™, INEOS Composites has leveraged new production capabilities to modernize resin features including improved environmental performance, better workability, and increased worker satisfaction. Features Derakane™ Signia™ resins provide significant advantages for fabricators, design engineers and asset/end users of corrosion resistant FRP equipment. Today, many fabricators are challenged with finding qualified and experienced operators to meet current order demands. Anticipating these needs, Derakane™ Signia™ resins were designed to deliver improved processing characteristics driving faster laminate consolidation, lower foaming and greatly reduced sanding for application of secondary laminations. Additional benefits include reduced styrene emissions and odor with innovative cure packages that can eliminate production steps when making thick parts. All of these characteristics lead to greatly improved shop efficiency and cleanliness, resulting in a much more desirable workplace. Improved Laminating Reduced Foaming Reduced foaming in Derakane™ Signia™ resins leads to fewer entrapped gas bubbles and faster consolidation of reinforcement layers. In Figure 1, the foaming of Derakane™ Signia™ 411 (left) and Derakane™ Momentum™ 411-350 resins (right) is compared 90 seconds after adding Norox® MEKP-925H1. The lower foaming observed in the Derakane™ Signia™ sample leads to easier rollout, resulting in laminates with fewer voids. In this study, Derakane™ Signia™ 411 was promoted with 0.2 parts per hundred (pph) cobalt naphthenate 6% and 0.05 pph dimethylaniline (DMA), and Derakane™ Momentum™ 411-350 was promoted with 0.2 pph cobalt naphthenate 6%. Both were initiated with 1 phr of high dimer Norox® MEKP-925H for a 15-minute gel time. Improved shop efficiency In this paper, we will expand on how Derakane™ Signia™ resins improve shop efficiency. Numerous shop trials performed with Derakane™ Signia™ 411 bisphenol-A epoxy vinyl ester resin demonstrate how Signia™ technology provides a cleaner, more efficient shop environment. Longer shelf life Consistent polymer backbone Identifiable resin system Figure 1. Comparison of foaming in promoted and initiated Derakane™ Signia™ 411 (left) and Derakane™ Momentum
Open the catalog to page 1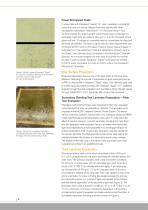
Fewer Entrapped Voids In shop trials with Derakane™ Signia™ 411 resin, operators consistently noted that wet-out and air release improved significantly when compared to Derakane™ Momentum™ 411-350 and Hetron™ 922. To demonstrate this improvement, experiments were conducted on laminates made with two plies of 450 g/m2 (1.5 oz/ft2) chopped strand glass mat with 10 passes of a serrated roller to consolidate the plies and eliminate air bubbles. The resin-to-glass ratio for these experiments was controlled at 65% resin to 35% glass. Figure 2 shows typical images of laminates from this...
Open the catalog to page 2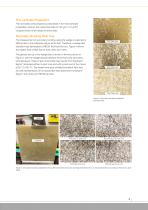
Thin Laminate Preparation Thin laminates were prepared as described in the thick laminate preparation section, but using three plies of 450 g/m2 (1.5 oz/ft2) chopped strand mat instead of seven plies. Secondary Bonding Fiber Tear The measurement of secondary bonding using the wedge or peel test is difficult due to the subjective nature of the test. Therefore, a wedge test standard was developed by INEOS Technical Service. Figure 4 shows the relative level of fiber tear at 20%, 60% and 100%. The general set-up of the wedge test is shown in the first picture of Figure 5, with the wedge placed...
Open the catalog to page 3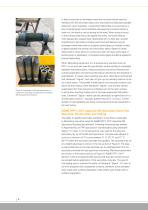
In tests conducted on laminates where the corrosion barrier was the interface with the secondary layer, poor secondary bonding was typically observed. Upon evaluation, it was found disbonding occurred due to a lack of reinforcement at the interface. Because the corrosion barrier is resin rich, the bond is only as strong as the resin. When trying to bond to the surfaces that had cured against the mold, we found residual mold release also caused clean disbonding with no fiber tear. Another impediment to secondary bonding was found with filament wound laminates where there was no chopped...
Open the catalog to page 4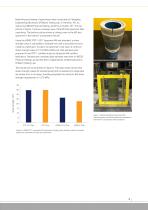
Machining and testing of specimens were conducted by Fiberglass Engineering Mechanics (FEMech) Testing Lab, in Harrison, AR, as well as the INEOS Physical Testing Lab (IPTL) in Dublin, OH. The top picture in Figure 7 shows a closeup view of the M5 test specimen after machining. The bottom picture shows a closeup view of the M5 test specimen in the Instron® compression fixture3. Using the ASME RTP-1-2017 Appendix M5 test standard, a shear strength value is calculated to evaluate how well a secondary bond is made by a fabricator. To pass, the specimen must reach a minimum shear strength value...
Open the catalog to page 5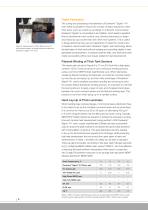
Faster Fabrication Figure 9. Measurement of thick filament wound tank section made in a single continuous step with Derakane™ Signia™ 411 resin. The curing and processing characteristics of Derakane™ Signia™ 411 resin make it possible to reduce the number of steps required to make thick parts, such as a hand lay-up flange on a filament wound vessel. Derakane™ Signia™ is not sensitive to air inhibition, which leads to excellent Barcol development and surface cure, allowing fabricators to begin secondary lay-ups sooner than with other resin systems. This is useful in flange attachment lay-ups...
Open the catalog to page 6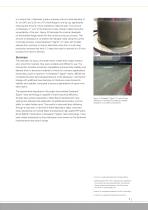
In a recent trial, a fabricator made a manway with an inside diameter of 91 cm (36") and a 20 mm (.75") thick flange in one lay-up, significantly reducing the amount of time needed to make the part. The amount of drawback or “curl” of the final part is also critical in determining the acceptability of the part. Figure 10 illustrates the minimal drawback on the finished flange made with the continuous lay-up process. This amount of drawback is consistent with flanges made using the current multi-step process. Using Derakane™ Signia™ 411 resin with CuNap allowed the customer to reduce...
Open the catalog to page 7All Ineos composites catalogs and technical brochures
-
AROTRAN™ 300
2 Pages
-
DERAKANE™ SIGNIA™
8 Pages
-
DERAKANE™ FABRICATION GUIDE
76 Pages
Archived catalogs
-
DERAKANE CHEMICAL RESISTANCE GUIDE
84 Pages
-
FR Strategist 2011
4 Pages
-
DERAKANE Fabricating Tips
56 Pages