
Catalog excerpts
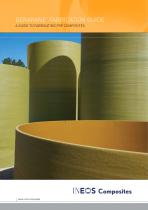
DERAKANE FABRICATION GUIDE ™ A GUIDE TO FABRICATING FRP COMPOSITES
Open the catalog to page 1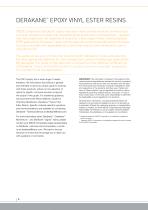
DERAKANE EPOXY VINYL ESTER RESINS ™ INEOS Composites Derakane™ epoxy vinyl ester resins provide excellent chemical and corrosion resistance coupled with outstanding heat performance and toughness – qualities that have made them the materials of choice for a wide range of fiber-reinforced plastic (FRP) applications. Derakane™ resins can be used with conventional fabricating techniques to produce durable and dependable structures that require little maintenance over a long service life. This guide serves as an introduction to working with Derakane™ resins and selecting the most appropriate...
Open the catalog to page 2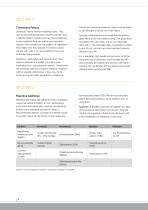
SECTION 1 Thermoset Resins Derakane resins are thermosetting resins. They cure by crosslinking between reactive polymers and a reactive diluent, typically styrene. This crosslinking is accomplished via a free radical polymerization reaction that is initiated by the addition of ingredients that readily form free radicals. Formation can be started with heat or by using additives that work at ambient temperatures. ™ Derakane™ resins begin as a viscous liquid. Once reactive additives are added, the liquid cures irreversibly into a solid polymer network. Cured resins are inherently heat and...
Open the catalog to page 4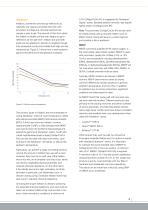
Initiators1 Initiators, sometimes erroneously referred to as catalysts, are organic peroxides that work with promoters to initiate the chemical reaction that causes a resin to gel. The amount of time from when the initiator is added until the resin begins to gel is referred to as the “gel time.” Initiator and promoter levels can be adjusted to shorten or lengthen the gel time somewhat and accommodate both high and low temperatures. Figure 2.1 shows how a resin system’s gel time shortens as the temperature increases. Figure 2.1: Gel time versus temperature. Two primary types of initiators...
Open the catalog to page 5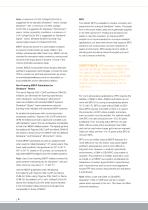
Note: A minimum of 0.2% CoNap/CoOct 6% is suggested for all standard Derakane™ resins, except Derakane™ 470. A minimum of 0.05% CoNap/ CoOct 6% is suggested for Derakane™ Momentum™ resins. Under normal/dry conditions, a minimum of 0.1% CoNap/CoOct 6% is suggested for Derakane™ Signia™ resins. Elevated ambient humidity may require higher levels of CoNap/CoOct 6%. MEKP should be stored in a well-sealed container to prevent contamination by water. Water in the initiator will adversely affect resin cure. MEKP can be checked for excessive water content by mixing small amounts with equal parts of...
Open the catalog to page 6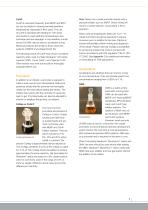
CuHP CuHP is used less frequently than MEKP and BPO, but can be helpful in lowering laminate exotherm temperatures, especially in thick parts. The use of CuHP is standard with Derakane™ 470 resins and results in lower exotherm temperatures, less shrinkage and less warpage. In cool weather, a small amount of DMA may be used to accelerate curing. Mixing procedures are similar to those used with systems of MEKP and CoNap/CoOct 6%. The following brands of CuHP have shown consistent reactivity when used to initiate Derakane™ 470 resins: Luperox CU902, Curox CuHP3, and Trigonox4 K-90. Other...
Open the catalog to page 7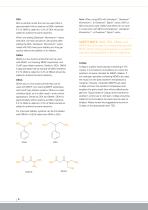
DEA DEA is another amine that can be used. DEA is approximately half as reactive as DMA; therefore, if 0.1% DMA is called for, 0.2% of DEA should be added to achieve the same reactivity. When formulating Derakane™ Momentum™ resins with DEA, the resin should be used shortly after adding the DEA. Derakane™ Momentum™ resins mixed with DEA have poor stability and may gel quickly without the addition of an initiator. DMAA DMAA is a low toxicity amide that can be used with MEKP, non-foaming MEKP substitutes, and CuHP-type initiator systems. Similar to DEA, DMAA is approximately half as reactive...
Open the catalog to page 8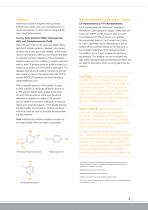
Gel Time Retarder for Derakane™ Resins Inhibitors are used to lengthen resin gel times. Inhibitors are useful when very long gel times (1–2 hours) are required or when resin is curing quickly due to high temperatures. Tertiary Butyl Catechol (TBC), Hydroquinone (HQ), and Toluhydroquinone (THQ) TBC, HQ, and THQ can be used with MEKP, BPO, and CuHP initiator systems. However, care should be taken not to add too much inhibitor, which could result in permanent undercure, low Barcol hardness, or reduced corrosion resistance. Recommended inhibitor levels vary from inhibitor to inhibitor and from...
Open the catalog to page 9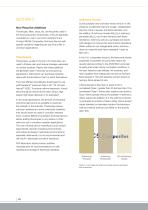
SECTION 3 Non-Reactive Additives Thixotropes, fillers, clays, etc. are frequently used in the structural portion of laminates. They are generally unsuitable for use in corrosion-resistant liners. Contact INEOS Composites Technical Service with specific questions regarding the use of any filler in corrosion applications. Thixotropes Thixotropes, usually in the form of fumed silica, are used to thicken resin and reduce drainage, especially on vertical surfaces. Resins with these additives are generally used in hand lay-up and spray-up applications. Fabricators can purchase polyester resins...
Open the catalog to page 10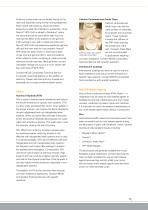
Antimony compounds can be added directly to the resin and dispersed using normal mixing equipment. Resin mixed with antimony should be stirred frequently to keep the materials in suspension. Once Nyacol®3 APE-1540 is added to Derakane™ resins, the mixture should be used within eight hours to minimize the effect of the additive on the gel time. If left overnight, resin with a cobalt promoter and Nyacol® APE-1540 may experience significant gel time drift and the resin may not cure properly. Nyacol® APE-3040 has been shown to have less impact on gel time and gel time drift in resin...
Open the catalog to page 11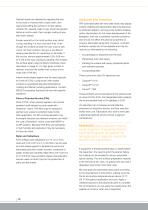
Optimal results are obtained by applying the wax to the mold or mandrel with a clean cloth, then vigorously buffing the surface to a hard, glossy, ultrathin film. Several coats of wax should be applied before a mold is used, then a single coating of wax after each release. Excess wax left on the mold surface may inhibit curing, resulting in a hazy corrosion liner. Even though the surface beneath the wax may be fully cured, the hazy surface may give a low Barcol reading (see Section 8, Inspecting a Laminate). If this occurs, remove approximately 0.05–0.08 mm (2–3 mil) of the wax coating by...
Open the catalog to page 12All Ineos composites catalogs and technical brochures
-
AROTRAN™ 300
2 Pages
-
DERAKANE™ SIGNIA™ RESINS
8 Pages
-
DERAKANE™ SIGNIA™
8 Pages
Archived catalogs
-
DERAKANE CHEMICAL RESISTANCE GUIDE
84 Pages
-
FR Strategist 2011
4 Pages
-
DERAKANE Fabricating Tips
56 Pages