
Catalog excerpts
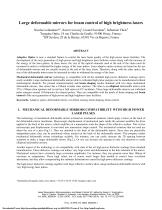
Large deformable mirrors for beam control of high brightness lasers Nicolas Lefaudeux*a, Xavier Levecqa, Lionel Escolanob, Sebastien Theisb a Imagine Optic, 18 rue Charles de Gaulle, 91400 Orsay, France; b ISP System, ZI de la Herray, 65501 Vic en Bigorre, France ABSTRACT Adaptive Optics is now a standard feature to control the laser beam quality of the high power lasers facilities. The development of the next generation of high power and high brightness laser facilities comes along with the increase of the energy of the laser pulses. In these lasers, the size of the optical elements used at the end of the chain must be increased in order to withstand the higher energy of the laser pulses. Laser adaptive optics systems are based on the use of deformable mirrors and are usually located at the end of the laser chain. Therefore, along with the other optics, the size of the deformable mirror must be increased in order to withstand the energy of the laser. Mechanical deformable mirror technology is compatible with all the standard high power dielectric coatings and is easily scalable. Large mechanical deformable mirrors able to withstand high pulse energies can be manufactured without technological obstacle. We present characterization and beam shaping results obtained with two large mechanical deformable mirrors. One mirror has a 180mm circular clear aperture. The other is an elliptical deformable mirror with 270 x 190mm clear aperture and is used as a fold mirror at 45° incidence. These large deformable mirrors can withstand pulse energies around 10 kilojoules for chirped pulses. They are compatible with the needs of beam shaping and beam control of the next generation of high power and high brightness laser facilities. Keywords: Adaptive optics, deformable mirror, wavefront sensing, beam shaping, beam control 1. MECHANICAL DEFORMABLE MIRRORS COMPATIBILITY WITH HIGH POWER LASER PULSES The technology of mechanical deformable mirror is based on mechanical actuators which apply a force on the back of the deformable mirror membrane. Macroscopic displacement of mechanical parts inside the actuator modifies the force applied to the back of the mirror, which modifies on a nanometric scale the shape of the reflective surface. This is how macroscopic part displacement is converted into nanometric shape control. The mechanical actuators that are used are about the size of a pen (Fig.1.). They are attached to the back of the deformable mirror. Since they are physically independent parts, they can be positioned where needed on the back of the deformable mirror. This property makes mechanical deformable mirror technology scalable. For instance, one can easily increase the 2D spacing between actuators to make a larger deformable mirror (Fig.2.). Or one can increase the spacing in only one direction to make elliptical deformable mirrors. Another aspect of the technology is its compatibility with state of the art high power dielectric coatings from standard manufacturers. These dielectric coatings can induce very large stress and deformation to the thin substrate of the mirror. Mechanical mirrors have extremely large correction amplitudes. For instance, they can generate more than 100µm of curvature or astigmatism. These high values are of course much larger than needed to correct laser wavefront aberrations, but they allow compensating the substrate deformations caused by high power dielectric coatings. The high power dielectric coatings together with large reflective surface allow using mechanical deformable mirrors with very high energy laser pulses. Laser Resonators, Microresonators, and Beam Control XV, edited by Alexis V. Kudryashov, Alan H. Paxton, Vladimir S. Ilchenko, Lutz Aschke, Kunihiko Washio, Proc. of SPIE Vol. 8600, 86000W · © 2013 SPIE · CCC code: 0277-786/13/$18 · doi: 10.1117/12.2001841 Proc. of SPIE Vol. 8600 86000W-1 Downloaded From: http://proceedings.spiedigitallibrary.org/ on 04/02/2013 Terms of Use: http://spiedl.org/te
Open the catalog to page 1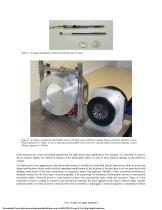
Figure 1. A single mecha anical actuator is about the size of a pen. i e Figure 2. At right, a mechanical deform mable mirror wit high power dielectric coatin Beam correc th d ng. ction diameter is up to i 95mm, ap perture is 110mm At left, a me m. echanical deform mable mirror fo use in vacuum Beam correc or m. ction diameter is up to i 180mm, a aperture is 200m mm. Some feature have been d es developed spe ecifically for h high power la applicatio For instan aser on. nce, it is possi ible to remove e and to replac rapidly the reflective sur ce rface of the de eformable mi irror in case of...
Open the catalog to page 2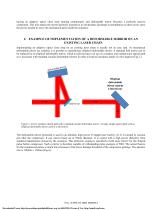
having an adaptive optics close loop running continuously and deformable mirror becomes a perfectly passive component. This also makes the mirror perfectly insensitive to electrostatic discharge or perturbation as these never carry the power needed to move the mechanical parts inside the actuators. 2. EXAMPLE OF IMPLEMENTATION OF A DEFORMABLE MIRROR ON AN EXISTING LASER CHAIN Implementing an adaptive optics close loop on an existing laser chain is usually not an easy task. As mechanical deformable mirror are scalable, it is possible to manufacture elliptical deformable mirror. A standard...
Open the catalog to page 3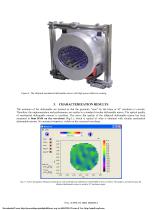
Figure 4. The elliptical mechanical deformable mirror with high power dielectric coating. 3. CHARACTERIZATION RESULTS The actuators of the deformable are located so that the geometry “seen” by the beam at 45° incidence is circular. Therefore, the implementation and performance are similar to a standard circular deformable mirror. The optical quality of mechanical deformable mirrors is excellent. The active flat quality of the elliptical deformable mirror has been measured at 8nm RMS on the wavefront (Fig.5.), which is typical of what is obtained with circular mechanical deformable mirrors....
Open the catalog to page 4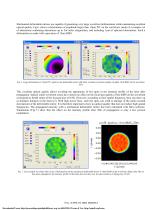
Mechanical deformable mirrors are capable of generating very large wavefront deformations while maintaining excellent optical quality. Fig.6. shows a deformation of amplitude larger than 10µm PtV on the wavefront, made of a complex set of aberrations containing aberrations up to 5th order astigmatism, and including 1µm of spherical aberrations. Such a deformation is made with a precision of 12nm RMS Wavefront Eile Wave front Fig. 6. Large deformations (>10µm PtV, right) on the deformable mirror still allow excellent correction quality (residual 12nm RMS on the wavefront, left). This...
Open the catalog to page 5All Imagine Optic catalogs and technical brochures
-
WAVE Suite
3 Pages
Archived catalogs
-
Microtraps
4 Pages
-
AO inside laser chain
5 Pages
-
AO in femtosecond laser
5 Pages
-
NIR optics characterization
6 Pages
-
Telescope characterization
3 Pages
-
absolute measurement
4 Pages
-
HASO R.FLEX
4 Pages
-
HASO3
2 Pages
-
bendAO?
3 Pages
-
HASO?3 WSR Wavefront Sensors
2 Pages
-
HASO R-Flex
3 Pages
-
SL-Sys LIQUID
2 Pages
-
SL-Sys neo
2 Pages
-
HASO™3 Wavefront Sensors
3 Pages