
Catalog excerpts
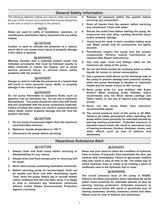
The following attention notices are used to notify and advisethe user of this product of procedures that may be dangerous tothe user or result in damage to the product. Notes are used to notify of installation, operation, ormaintenance information that is important but not safety related.Caution is used to indicate the presence of a hazard,which will or can cause minor injury or property damage if the notice is ignored.Warning denotes that a potential hazard exists andindicates procedures that must be followed exactly to either eliminate or reduce the hazard, and to avoid serious personal...
Open the catalog to page 2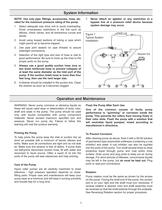
air must be kept out. Plugports or seal port connections. Flush the Pump After Each UseOne of the common causes of faulty pumpperformance is gummingӔ or corrosion inside the pump. This prevents the rollers from moving freely in their rotor slots. Flush the pump with a solution that will neutralize liquid pumped, mixed according to manufacturers directions.To Prevent Corrosion Rotation Never attach an agitator or any restriction to abypass line of a pressure relief device because system damage may occur. After cleaning pump as above, flush it with a 50-50 solutionof permanent type automobile...
Open the catalog to page 3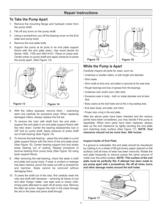
1.Remove the mounting flange and hydraulic motor fromthe pump shaft.2.File off any burrs on the pump shaft. 3.Using a screwdriver, pry off the bearing cover on the Endplate and pump body4.Remove the end plate bolts. 5.Support the pump at its ports in an end plate supportfixture with the end plate down. Use wood blocks for Series 1500, 1700 and 4001/4101. Place on press bed. Center press on pump shaft and apply pressure to press the pump apart. (See Figure 13). > Carefully inspect all parts for wear, such as: Undersize or swollen rollers, in both length and diameter.ՕWorn seals. Worn shaft...
Open the catalog to page 4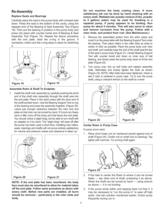
Do not machine the body casting clean. Amore satisfactory job can be done by hand cleaning with an emery cloth. Wettable talc powder mixture (5 lbs. powder to 5 gallons water) may be used for breaking in a repaired pump, if pump appears to be binding. Run pump for about 5 minutes. This will also serve to clean and remove corrosion from the pump. Follow with a clear rinse, and protect from rust. (See Maintenance.) Replace Seals and Bearings Carefully place the seal in the pump body with crimped sidedown. Press the seal to the bottom of the cavity, using the stepped end of the Bearing & Seal...
Open the catalog to page 5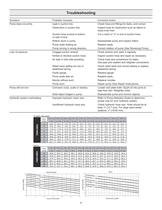
SymptomProbable Cause(s)Corrective ActionPumpdoes not prime.Leak in suction line.Check hose and fittings for leaks, and correct.Obstruction in suction line.Inspect hose for obstruction such as debris or loose inner liner.Suction hose sucked to bottomCut a notch or VӔ in end of suction hose.orside of tank.Rollers stuck in pump.Disassemble pump and inspect rollers. Pump seals leaking air.Replace seals. Pump turning in wrong direction.Correct rotation of pump (See Reversing Pump).Loss of pressure.Clogged suction strainer.Check strainer and clean it regularly.Kinked or blocked suction...
Open the catalog to page 6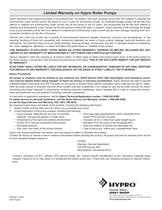
Hypro warrants to the original purchaser of its products (the PurchaserӔ) that such products will be free from defects in material andworkmanship under normal use for the period of one (1) year for all products except: oil crankcase plunger pumps will be free fromdefects in material and workmanship under normal use for the period of five (5) years, and accessories will be free from defects inmaterial and workmanship under normal use for the period of ninety (90) days. In addition, Hypro warrants to the purchaser all forgedbrass pump manifolds will be free from defects in material and...
Open the catalog to page 8All Hypro Pressure Cleaning catalogs and technical brochures
-
PRODUCT CATALOG
236 Pages
-
Transfer Pumps
7 Pages
-
Gear Driven
3 Pages
-
Centrifugal Pumps
41 Pages
-
9302 Series
2 Pages
Archived catalogs
-
ULD Sales Sheet
2 Pages
-
ESI Sales Sheet
2 Pages
-
TwinCap Sales Sheet
2 Pages
-
HP Stainless Steel Nozzles
2 Pages
-
UAS Ceramic Nozzles
2 Pages
-
9302 Series Sales Sheet
2 Pages
-
Hydraulic Pump Selection Guide
38 Pages
-
Foam Marker OIPM
20 Pages
-
Cleanload OIPM
12 Pages
-
Series 2100 Versa-Twin OIPM
16 Pages
-
Hydraulic Pressure Washer OIPM
20 Pages
-
PowerLine Plunger OIPM
24 Pages
-
2535S OIPM
12 Pages
-
Series 5200 Piston Pump OIPM
8 Pages
-
Series 5300 OIPM
20 Pages
-
DBS & DBA Diaphragm Pump OIPM
20 Pages