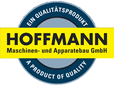
Catalog excerpts
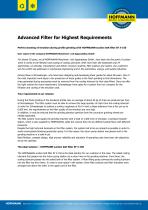
Advanced Filter for Highest Requirements Perfect cleaning of emulsion during profile grinding with HOFFMANN suction belt filter SF 3-150 User report of the company HOFFMANN Maschinen- und Apparatebau GmbH For almost 50 years, we at HOFFMANN Maschinen- und Apparatebau GmbH, have been the first point of contact when it comes to the filtration and cooling of cooling lubricants. With more than 200 employees and 24 apprentices, we develop, manufacture and deliver conveyor systems, filter systems and coolers. Our customers are the world's top addresses in mechanical engineering and in the automotive, energy, and supply industries. Among these is Schneeberger, who have been designing and developing linear guides for about 80 years. One of the most important work steps in the production of linear guides is the finish grinding to final dimensions. The chips generated during processing must be removed from the cooling lubricant by first-class filters. Since we offer the right solution for every requirement, Schneeberger have opted for a system from our company for the filtration and cooling of the emulsion used. Your requirement is our mission During the finish grinding of the hardened profile rails, an average of about 60 kg of chips are produced per hour at Schneeberger. The filter system must be able to remove this large quantity of chips from the cooling lubricant. In order for Schneeberger to achieve a surface roughness of Ra 0.4 and a shape tolerance from a few μm up to 6,000 mm, the requirements on the filter quality of the emulsion are very high. In addition, it must be ensured that the grinding abrasion particles from the corundum grinding wheels are reliably separated. The filter system must supply the grinding machine with a total of 1,300 l/min of emulsion. A pressure booster station, which is also supplied by HOFFMANN, splits this volume flow into six different partial flows with different pressures. Despite the high technical demands on the filter system, the system had to be as compact as possible in order to avoid unnecessarily blocking production space. For this reason, the return pump station was placed next to the grinding machine in a walk-in pit. Best filtration, compact design, high process reliability and reduction of operating costs have been the objectives set by the operator. The ideal solution – HOFFMANN suction belt filter SF 3-150 The HOFFMANN suction belt filter SF 3-150 is the ideal solution for our customer in this case. The soiled cooling lubricant first passes into the return pump station via a return line on the grinding machine. From there, the cooling lubricant passes into the soiled tank of the filter system. A filter lifting pump conveys the cooling lubricant into the filter top from there. In order to save space in the system, three filter surfaces and filter chambers were arranged one above the other in the upper part of the filter. Maschinen- und Apparatebau GmbH | Hauerstraße 2–4 | 38268 Lengede | Germany | +49 5344 9009-0 | info@hoffmann-filter.de | www.hoffmann-filter
Open the catalog to page 1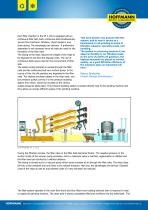
Each filter chamber in the SF 3-150 is equipped with an "We have broken new ground with this continuous filter belt. Each continuous belt simultaneously system, and by now it serves as a serves three functions: Filtration, chips transport, and benchmark in rail grinding in terms of chips drying. The advantages are obvious: A preliminary filtration capacity, operating costs, and separation is not necessary since all chips are used for the handling. The system is convincing because it can formation of the filter cake. adapt so flexibly to our filtration tasks. The drying of the chips reduces...
Open the catalog to page 2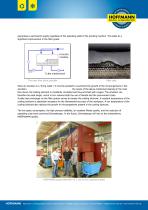
guarantees a permanent supply regardless of the operating state of the grinding machine. This leads to a significant improvement in the filter grade. The main flow shunt principle Filter cake Since an emulsion is a "living water", it must be aerated to counteract the growth of the microorganisms in the emulsion. By means of the above-mentioned cleaning in the main flow shunt, the cooling lubricant is constantly circulated and thus enriched with oxygen. The emulsion can therefore be used longer, which in turn reduces both the use of biocide and the procurement costs. A plate heat exchanger...
Open the catalog to page 3All HOFFMANN APPARATE catalogs and technical brochures
-
IMMERSION COOLER ERK
2 Pages
-
WATER COOLER WRK
2 Pages
-
WATER COOLER WRK
2 Pages