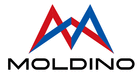
Group: HITACHI

Catalog excerpts
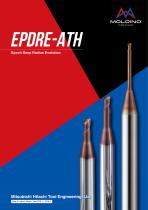
EPDRE-ATH Epoch Deep Radius Evolution
Open the catalog to page 1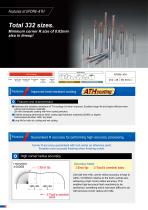
Minimum corner R size of 0.02mm also in lineup! Carbon steel Stainless steel Pre-hardened Alloy steel Tool steel steel EPDRE-ATH Parts processing Mold making Improved heat-resistant coating Features and characteristics Hardness and oxidation resistance of TH coatings is further improved. Enables longer life and higher efficient when cutting high-hardness materials. (Si nano composite coating with finer crystal particles) Exhibits amazing performance when cutting high-hardness materials (55HRC or higher) Cold-worked die steel, HSS, tool steel. Long life for both dry cutting and wet cutting...
Open the catalog to page 2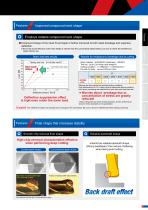
Improved compound neck shape Employs reliable compound neck shape ● Compound shape of tool neck R and taper is further improved to both resist breakage and suppress Static load test results oad 65 Testing tool size φ1×Under neck 6 Convent Conventi al ne sh p Convent onal neck shape Conventional neck shape o en e l Work material:SUS420J2H(Hardness:52HRC) Tool dia.: φ1(r 0.2)×Under neck length10 Cutting condition:n =12800min-1 v f =200mm/min∼ Dry with Air blow ap×ae=0.02mm×1mm Deflection amount【mm】 Deflection suppression effect is high even under the same load. Although the feed rate for the...
Open the catalog to page 3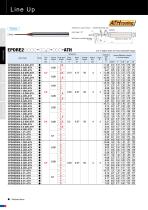
Tolerance on Corner radius r : ±0.005mm(Central axis) Back taper on peripheral edge: -1.5—6° EPDRE2 ATH 0 4 or higher does not have backdraft shape.
Open the catalog to page 4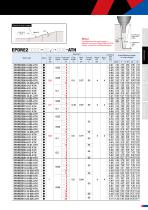
EPDRE2 ATH [Note] The effective under-neck length is different from Epoch Deep Radius EPDR. Please recheck the interference region.
Open the catalog to page 5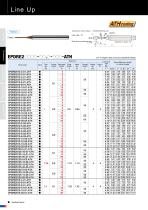
Tolerance on Corner radius r : ±0.005mm(Central axis) EPDRE2 ATH 0 4 or higher does not have backdraft shape.
Open the catalog to page 6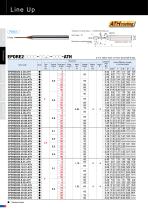
Tolerance on Corner radius r : ±0.005mm(Central axis) EPDRE2 ATH 0 4 or higher does not have backdraft shape.
Open the catalog to page 8
EPDRE2 ATH [Note] The effective under-neck length is different from Epoch Deep Radius EPDR. Please recheck the interference region.
Open the catalog to page 9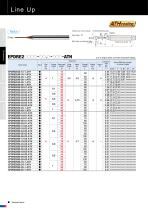
Line Up coating 2 Flutes φD c Back taper on peripheral edge : 1.5~6° High efficiency cutting cutting condition High efficiencycondition High accuracy cutting cutting condition High accuracycondition Technical Data Technical Data ●:Stocked Items. Corner Under neck radius length Flute length φ 4 or higher does not have backdraft shape. Neck dia. Overall length Size(mm) Item Code Tolerance on Corner radius r :±0.005mm(Central axis) Interference Angle Actual Effective Length in Incline Angles 14.08 14.72 16.23 18.64 19.51 No interference 23.20 24.30 No interference 34.61 No interference No...
Open the catalog to page 10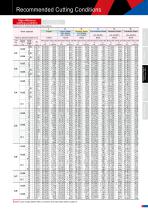
Please refer to P.16 about high accuracy cutting conditions [Note] Upon usage, please refer to comments and notes below table on page 15.
Open the catalog to page 11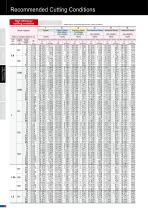
Please refer to P.16 about high accuracy cutting conditions
Open the catalog to page 12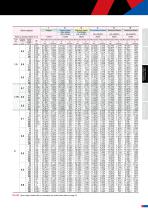
[Note] Upon usage, please refer to comments and notes below table on page 15.
Open the catalog to page 13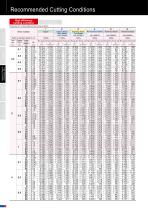
High efficiency cuttiing condition Please refer to P.16 about high accuracy cutting conditions
Open the catalog to page 14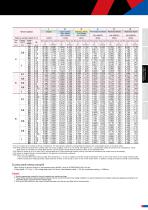
^(1) ap is shown as the criteria for Group 2 workpieces. For other groups, adjust the cutting depth according to the cutting depth factors in the above table. ^(2) When performing cutting where cutting chips may cause clogging, such as for rib cutting, blind grooves, etc., cutting depth setting should be set by multiplying a cutting depth factor to calculate the cutting depth amount, and this amount should then be reduced to 80% of the calculated value. ^(3) Adjust by setting ae to (5 or less)x(ap)x(cutting depth ratio). When performing finishing cutting, calculate the theoretical cusp...
Open the catalog to page 15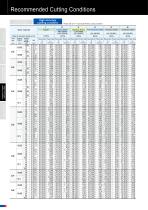
Please refer to P.11 about high efficiency cutting conditions
Open the catalog to page 16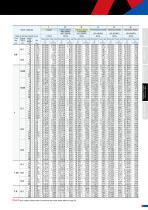
[Note] Upon usage, please refer to comments and notes below table on page 20.
Open the catalog to page 17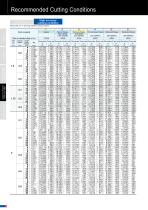
Please refer to P.11 about high efficiency cutting conditions
Open the catalog to page 18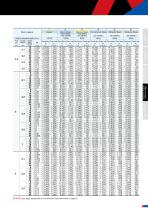
Work material [Note] Jpon usage, please refer to comments and notes below table on page 20.
Open the catalog to page 19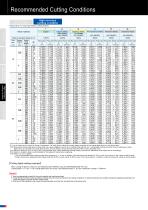
Please refer to P.11 about high efficiency cutting conditions ^(1) ap is shown as the criteria for Group 2 workpieces. For other groups, adjust the cutting depth according to the cutting depth factors in the above table. ^(2) When performing cutting where cutting chips may cause clogging, such as for rib cutting, blind grooves, etc., cutting depth setting should be set by multiplying a cutting depth factor to calculate the cutting depth amount, and this amount should then be reduced to 80% of the calculated value. ^(3) Adjust by setting ae to (5 or less)x(ap)x(cutting depth ratio). When...
Open the catalog to page 20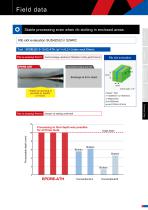
Field data Stable processing even when rib slotting in enclosed areas. Features This is amazing! Point 1 Good breakage resistance! Stabilized cutting performance! Conventional radius end mill 25mm Stable processing is possible to depths of 10mm. Deeper rib slotting achieved! Processing to final depth was possible for all three tools. Technical Data This is amazing! Point 2 High accuracy cutting condition High efficiency cutting condition Target depth Broken Broken
Open the catalog to page 21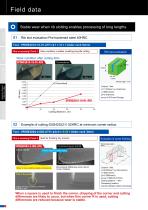
Field data Stable wear when rib slotting enables processing of long lengths. Features This is amazing! Point 1 Wear condition is stable, enabling long-life cutting. Wear condition after cutting 40m EPDRE2010-10-01-ATH High efficiency cutting condition High accuracy cutting condition Technical Data 02 Example of cutting SUS420J2Ⓗ 52HRC at minimum corner radius. Tool:EPDRE2004-2-002-ATH (φ0.4×r 0.02×Under neck 2mm) This is amazing! Point 2 Ideal for finishing tiny corners Conventional Square End Mill Evaluation of corner finishing Work observation point Flute tip edge line before cutting...
Open the catalog to page 22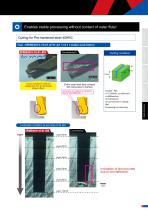
Enables stable processing without contact of outer flute! Features Cutting for Pre-hardened steel 40HRC Tool:EPDRE2010-10-01-ATH (φ1×r 0.1×Under neck10mm) Conventional A Cutting condition Back draft effect Entire outer flank face contacts with work-piece to fracture Inclination of chattering vibrations due to tool deflection. Technical Data Coolant:Wet n=17,350min-1(vc=54m/min) v f =655mm/min (fz=0.018mm/t) ap×ae=0.012mm× Change Wet Processing by contouring High accuracy cutting condition Good conditions without chattering due to backdraft shape effect. High efficiency cutting condition...
Open the catalog to page 23All MOLDINO Tool Engineering Europe GmbH catalogs and technical brochures
-
CBN-EPSB/CBN-EPSR
16 Pages
-
EPBTS
12 Pages
-
EMXR
16 Pages
-
EMXA
12 Pages
-
EPDRF-TH
12 Pages
-
EPDBPE-ATH
20 Pages
-
Epoch TH Power Mill
12 Pages
-
Radius Precision ARPF
20 Pages
-
Carbide Thread Mill series
16 Pages
-
SCE-R
6 Pages
-
RV type
12 Pages
-
ABPFN type
6 Pages
-
TD4N type
8 Pages
-
EHHB-ATH
8 Pages
-
EPCDS
4 Pages
-
Epoch CFRP series
6 Pages
-
EPSM-PN/ EPSW-PN
32 Pages
-
GALLEA series
24 Pages
-
WHMB-TH
12 Pages
-
EMBE-ATH/EMBPE-ATH
16 Pages
-
ETR(P)-TH,ETM(LN/P)-TH
16 Pages
-
CBN-EHB
12 Pages
-
EHHBE-TH3
8 Pages
-
TD6N type
12 Pages
-
EB4HR-ATH
12 Pages
-
EHX
12 Pages
-
EPHB-PN
8 Pages
-
EHHRE-TH3
8 Pages
-
EDT
16 Pages
-
EHSE-TH
8 Pages
-
NSB
12 Pages
-
WHNSB-TH
20 Pages
-
EMSBS
8 Pages
-
Ball Precision F ABPF type
16 Pages
-
Carbide Drill for SR machining
12 Pages
-
Radius Mill RD16B Type
8 Pages
-
GS4TN type
4 Pages
-
Red Screw Arbor
8 Pages
-
ABP4F
8 Pages
-
EPDBE-PN/ATH EPDSE-PN/ATH
32 Pages
-
EPDBEH-TH3
20 Pages
-
MINIATURE DRILL WHMB
8 Pages
-
Epoch ® Combination Rib Ball
8 Pages
-
PRODUCTS CATALOGUE 2015 - 2016
1070 Pages
-
Carbide Non Step Borer series
28 Pages
-
Drills for High-hardness Steels
16 Pages
-
Face Mill : ASF type
8 Pages
-
Face Mill : AFE45 type
8 Pages
-
Ball Precision F : ABPF type
16 Pages
-
Ball End Mill : ASB type
8 Pages
-
Radius Precision : ARPF type
12 Pages
-
Polish Mill V Type : ASPV Type
20 Pages
-
Roughing End Mill : AME Type
12 Pages
-
Radius Mill : AR type
20 Pages
-
JM4060
4 Pages
-
Epoch Micro?End Mill TH : EMM-TH
24 Pages
-
Epoch Deep Radius Evolution
24 Pages
-
Epoch Deep Ball Evolution Hard
16 Pages
-
Epoch Micro Drill?EMD
24 Pages
-
Radius Mill : ASR type
20 Pages
-
Super Excellent MINI : ASM type
12 Pages
-
Epoch "Mirus" Series
12 Pages
-
Epoch G Turbo
8 Pages
-
Roughing End Mill AME Type
12 Pages
-
Z Plunging Borer?ZPB-TH
4 Pages
-
Face Mill AFE45
8 Pages
-
Epoch Micro Step Borer S
8 Pages
-
Epoch CBN End Mill series
16 Pages
-
HX3505 & HX3515
6 Pages
-
GX2140
4 Pages
-
Epoch "Panacea"
16 Pages
-
Epoch Deep Evolution series
24 Pages
-
Epoch SUS End Mill series
32 Pages
-
Epoch Pencil Deep Ball Evolution
20 Pages
-
Epoch Deep Radius F
12 Pages
Archived catalogs
-
Carbide End Mills
280 Pages
-
HSS Non Step Borer
36 Pages
-
Surface Treatment Tribec
8 Pages
-
CBN End Mills
20 Pages
-
Re-grinding & Re-coating
20 Pages
-
Cutters
10 Pages
-
Reamers
16 Pages
-
HSS End Mills
98 Pages
-
Turning Inserts
44 Pages
-
Threading Tools
6 Pages
-
Indexable Tools
160 Pages
-
Milling Inserts
16 Pages
-
Micro Series for Micro Machining
14 Pages
-
2009-2010 New Products Guide
5 Pages