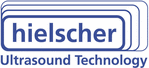

Catalog excerpts
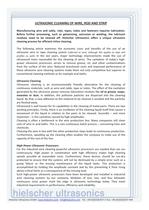
ULTRASONIC CLEANING OF WIRE, ROD AND STRIP Manufacturing wire and cable, rods, tapes, tubes and fasteners requires lubrication. Before further processing, such as galvanizing, extrusion or welding, the lubricant residues need to be cleaned off. Hielscher Ultrasonics offers a unique ultrasonic cleaning process for efficient inline cleaning. The following article examines the economic costs and benefits of the use of an ultrasonic wire or tape cleaning system (referred as wire, although this applies to tape and profiles as well). In the last years, major technology improvements made the use of ultrasound more reasonable for the cleaning of wires. The cavitation of today’s highpower ultrasonic processors serves to remove grease, oil, and other contaminations from the surface of the wire. Reduced investment costs and improved performance of these ultrasonic wire cleaning systems made them not only competitive but superior to conventional cleaning methods as for example acid baths. Ultrasonic Cleaning Ultrasonic cleaning is an environmentally friendly alternative for the cleaning of continuous materials, such as wire and cable, tape or tubes. The effect of the cavitation generated by the ultrasonic power removes lubrication residues like oil or grease, soaps, stearates or dust. In addition, the pollution particles are dispersed into the cleaning liquid. By that, a new adhesion to the material to be cleaned is avoided and the particles are flushed away. Ultrasound is well known for its capabilities in the cleaning of metal parts. There are two working principles. Firstly, there is an oscillation of the cleaning liquid itself that causes a movement of the liquid in relation to the parts to be cleaned. Secondly – and more important – is the cavitation caused by high amplitudes. Cleaning is often a bottleneck in the wire production line. Many companies still clean coils of wire in acid baths. This is a non-continuous batch process – consuming time and chemicals. Cleaning the wire in line with the other production steps leads to continuous production. Furthermore, speeding up the cleaning often enables the company to make use of the capacity of the rest of the line. High-Power Ultrasonic Processors For the industrial wire cleaning powerful ultrasonic processors are needed that can run continuously. High power in combination with high efficiency makes high cleaning speeds possible at reasonable costs. Furthermore, these devices should be run-dry protected to ensure that the systems will not be destroyed by a simple error such as a pump failure or the missing maintenance of the liquid tanks. This protection is accomplished by holding the amplitude constant and by this preventing it from rising above critical limits as a consequence of the missing load. Such high-power ultrasonic processors have been developed and installed in industrial wire cleaning systems by our company. Modules of one, two, and four kilowatts continuous sonic power mark the edge in ultrasonic technology today. They meet industrial requirements in performance, efficiency and reliability. Hielscher Ultrasonics GmbH www.hielscher.com; info@hielscher.com Tel.: +49 (0)3328/437-3 Fax: +49 (0)3328/437-444
Open the catalog to page 1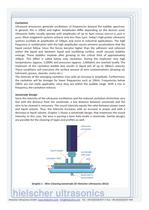
Cavitation Ultrasonic processors generate oscillations of frequencies beyond the audible spectrum. In general, this is 20kHz and higher. Amplitudes differ depending on the devices used. Ultrasonic baths usually operate with amplitudes of up to 4µm (always referred as peek to peek). Most megahertz-systems achieve only less than 1µm. Today’s high-power ultrasonic systems oscillate at amplitudes of 100µm and more in industrial applications. The high frequency in combination with the high amplitudes causes extreme accelerations that the liquid cannot follow. Since the forces become higher than...
Open the catalog to page 2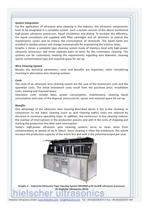
System Integration For the application of ultrasonic wire cleaning in the industry, the ultrasonic components have to be integrated in a complete system. Such a system consists of the above mentioned high-power ultrasonic processors, liquid circulations and drying. To increase the efficiency, the liquid circulations are supplied with filter cartridges and oil skimmers to extend the maintenance cycles and to reduce the consumption of chemicals. The liquid tanks are installed in double version and change automatically for maintaining the inactive tanks. Graphic 2 shows a complete tape...
Open the catalog to page 3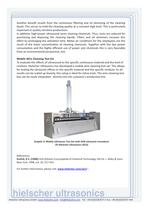
Another benefit results from the continuous filtering and oil skimming of the cleaning liquid. This serves to hold the cleaning quality at a constant high level. This is particularly important in quality sensitive productions. In addition, high-power ultrasound saves cleaning chemicals. Thus, costs are reduced for purchasing and disposing the cleaning liquids. Filters and oil skimmers increase this effect by prolonging the utilization time. Better air conditions for the employees are the result of the lower concentration of cleaning chemicals. Together with the low power consumption and the...
Open the catalog to page 4All Hielscher catalogs and technical brochures
-
Ultrasonic Process Lab
1 Pages
-
Ultrasonic Wire Cleaning
4 Pages
-
Ultrasonic Applications
1 Pages
-
Hielscher Ultrasonic Sieves
2 Pages