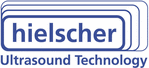

Catalog excerpts
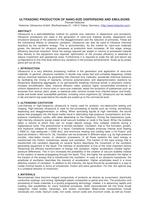
ULTRASONIC PRODUCTION OF NANO-SIZE DISPERSIONS AND EMULSIONS Thomas Hielscher Hielscher Ultrasonics GmbH, Warthestrasse 21, 14513 Teltow, Germany, (http://www.hielscher.com) ABSTRACT Ultrasound is a well-established method for particle size reduction in dispersions and emulsions. Ultrasonic processors are used in the generation of nano-size material slurries, dispersions and emulsions because of the potential in the deagglomeration and the reduction of primaries. These are the mechanical effects of ultrasonic cavitation. Ultrasound can also be used to influence chemical reactions by the cavitation energy. This is sonochemistry. As the market for nano-size materials grows, the demand for ultrasonic processes at production level increases. At this stage, energy efficiency becomes important. Since the energy required per weight or volume of processed material links directly to the equipment size required, optimization of the process efficiency is essential to reduce investment and operational costs. Furthermore it is required to scale the lab and bench top configurations to this final level without any variations in the process achievements. Scale up by power alone will not do this. 1. INTRODUCTION Ultrasound is a very effective processing method in the generation and application of nano-size materials. In general, ultrasonic cavitation in liquids may cause fast and complete degassing: initiate various chemical reactions by generating free chemical ions (radicals); accelerate chemical reactions by facilitating the mixing of reactants; enhance polymerization and depolymerization reactions by temporarily dispersing aggregates or by permanently breaking chemical bonds in polymeric chains; increase emulsification rates; improve diffusion rates; produce highly concentrated emulsions or uniform dispersions of micron-size or nano-size materials; assist the extraction of substances such as enzymes from animal, plant, yeast, or bacterial cells; remove viruses from infected tissue; and finally, erode and break down susceptible particles, including micro-organisms [2]. Ultrasound can be tested in lab and bench-top scale before the results are scaled up to the commercial level. 2. ULTRASONIC CAVITATION Low-intensity or high-frequency ultrasound is mainly used for analysis, non-destructive testing and imaging. High-intensity ultrasound is used for the processing of liquids such as mixing, emulsifying, dispersing and deagglomeration, or milling. When sonicating liquids at high intensities, the sound waves that propagate into the liquid media result in alternating high-pressure (compression) and lowpressure (rarefaction) cycles, with rates depending on the frequency. During the lowpressure cycle, high-intensity ultrasonic waves create small vacuum bubbles or voids in the liquid. When the bubbles attain a volume at which they can no longer absorb energy, they collapse violently during a highpressure cycle. This phenomenon is termed cavitation. Cavitation, that is "the formation, growth, and implosive collapse of bubbles in a liquid. Cavitational collapse produces intense local heating (~5000 K), high pressures (~1000 atm), and enormous heating and cooling rates (>109 K/sec)" and liquid jet streams (~400 km/h)” [4]. Cavitation can be produced in different ways: e.g. by high-pressure nozzles, rotor-stator mixers, or ultrasonic processors. In all those systems the input energy is transformed into friction, turbulences, waves and cavitation. The fraction of the input energy that is transformed into cavitation depends on several factors describing the movement of the cavitation generating equipment in the liquid. The intensity of acceleration is one of the most important factors influencing the efficient transformation of energy into cavitation. Higher acceleration creates higherpressure differences. This in turn increases the probability of the creation of vacuum bubbles instead of the creation of waves propagating through the liquid. Thus, the higher the acceleration the higher is the fraction of the energy that is transformed into cavitation. In case of an ultrasonic transducer, the amplitude of oscillation describes the intensity of acceleration. Higher amplitudes result in a more effective creation of cavitation. In addition to the intensity, the liquid should be accelerated in a way to create minimal losses in terms of turbulences, friction and wave generation. For this, the optimal way is a unilateral direction of movement. 3. MATERIALS Nanomaterials have become integral components of products as diverse as sunscreens, electrically conductive coatings, and strong, lightweight plastic composites or paints and inks. The production and processing of these materials is a quickly progressing technology. Indeed, it is advancing rapidly and creating new possibilities for many industrial processes. Solid nanomaterials fall into three broad categories: metal oxides, nanoclays, and carbon nanotubes. Metal-oxide nanoparticles include nanoscale zinc oxide, titanium oxide, iron oxide, cerium oxide and zirconium oxide, as well as mixed-
Open the catalog to page 1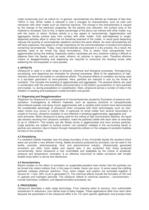
metal compounds such as indium-tin. In general, nanomaterials are defined as materials of less than 100nm in size. When matter is reduced in size it changes its characteristics, such as color and interaction with other matter such as chemical reactivity. The change in the characteristics is caused by the change of the electronic properties. By the particle size reduction, the surface area of the material is increased. Due to this, a higher percentage of the atoms can interact with other matter, e.g. with the matrix of resins. Surface activity is a key aspect of nanomaterials. Agglomeration...
Open the catalog to page 2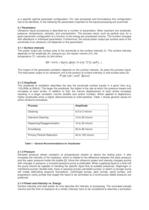
is a specific optimal parameter configuration. For new processes and formulations this configuration has to be identified. In the following the parameters important to the liquid processing are examined. 5.1 Parameters Ultrasonic liquid processing is described by a number of parameters. Most important are amplitude, pressure, temperature, viscosity, and concentration. The process result, such as particle size, for a given parameter configuration is a function of the energy per processed volume. The function changes with alterations in individual parameters. Furthermore, the actual power...
Open the catalog to page 3All Hielscher catalogs and technical brochures
-
Ultrasonic Process Lab
1 Pages
-
Ultrasonic Wire Cleaning
4 Pages
-
Ultrasonic Applications
1 Pages
-
Hielscher Ultrasonic Sieves
2 Pages