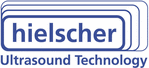

Catalog excerpts
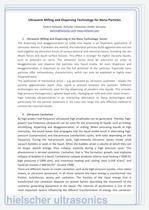
Ultrasonic Milling and Dispersing Technology for Nano-Particles Kathrin Hielscher, Hielscher Ultrasonics GmbH, Germany kathrin@hielscher.com; www.hielscher.com 1. Ultrasonic Milling and Dispersing in the Nano Technology Sector The dispersing and deagglomeration of solids into liquids is an important application of ultrasonic devices. If powders are wetted, the individual particles build agglomerates and are held together by attraction forces of various physical and chemical nature, including van der Waals forces and liquid surface tension. This effect is stronger for higher viscosity liquids, such as polymers or resins. The attraction forces must be overcome on order to deagglomerate and disperse the particles into liquid media. An even dispersion and deagglomeration is important to use the full potential of the particles. Especially nano particles offer extraordinary characteristics, which can only be exploited in highly even dispersed state. The application of mechanical stress – e.g. generated by ultrasonic cavitation - breaks the particle agglomerates apart. Also, liquid is pressed between the particles. Different technologies are commonly used for the dispersing of powders into liquids. This includes high pressure homogenizers, agitator bead mills, impinging jet mills and rotor-stator-mixers. High intensity ultrasonication is an interesting alternative to these technologies and particularly for the particle treatment in the nano-size range the only effectual method to achieve the required results. 2. Ultrasonic Cavitation By high-power/ low-frequency ultrasound high amplitudes can be generated. Thereby, highpower/ low-frequency ultrasound can be used for the processing of liquids such as mixing, emulsifying, dispersing and deagglomeration, or milling. When sonicating liquids at high intensities, the sound waves that propagate into the liquid media result in alternating highpressure (compression) and low-pressure (rarefaction) cycles, with rates depending on the frequency. During the low-pressure cycle, high-intensity ultrasonic waves create small vacuum bubbles or voids in the liquid. When the bubbles attain a volume at which they can no longer absorb energy, they collapse violently during a high pressure cycle. This phenomenon is termed cavitation. Cavitation, that is "the formation, growth, and implosive collapse of bubbles in a liquid. Cavitational collapse produces intense local heating (~5000 K), high pressures (~1000 atm), and enormous heating and cooling rates (>109 K/sec)" and liquid jet streams (~400 km/h)”. (Suslick 1998) There are different means to create cavitation, such as by high-pressure nozzles, rotor-stator mixers, or ultrasonic processors. In all those systems the input energy is transformed into friction, turbulences, waves and cavitation. The fraction of the input energy that is transformed into cavitation depends on several factors describing the movement of the cavitation generating equipment in the liquid. The intensity of acceleration is one of the most important factors influencing the efficient transformation of energy into cavitation. 1
Open the catalog to page 1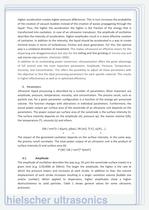
Higher acceleration creates higher pressure differences. This in turn increases the probability of the creation of vacuum bubbles instead of the creation of waves propagating through the liquid. Thus, the higher the acceleration the higher is the fraction of the energy that is transformed into cavitation. In case of an ultrasonic transducer, the amplitude of oscillation describes the intensity of acceleration. Higher amplitudes result in a more effective creation of cavitation. In addition to the intensity, the liquid should be accelerated in a way to create minimal losses in terms of...
Open the catalog to page 2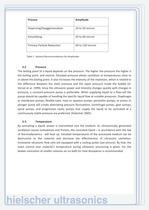
Primary Particle Reduction Table 1 - General Recommendations for Amplitudes 3.2. Pressure The boiling point of a liquid depends on the pressure. The higher the pressure the higher is the boiling point, and reverse. Elevated pressure allows cavitation at temperatures close to or above the boiling point. It also increases the intensity of the implosion, which is related to the difference between the static pressure and the vapor pressure inside the bubble (cf. Vercet et al. 1999). Since the ultrasonic power and intensity changes quickly with changes in pressure, a constant-pressure pump is...
Open the catalog to page 3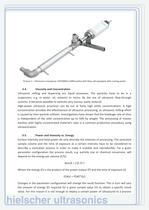
Picture 1 – Ultrasonic transducer UIP1000hd (1000 watts) with flow cell equipped with cooling jacket Viscosity and Concentration 3.4. Ultrasonic milling and dispersing are liquid processes. The particles have to be in a suspension, e.g. in water, oil, solvents or resins. By the use of ultrasonic flow-through systems, it becomes possible to sonicate very viscous, pasty material. High-power ultrasonic processor can be run at fairly high solids concentrations. A high concentration provides the effectiveness of ultrasonic processing, as ultrasonic milling effect is caused by inter-particle...
Open the catalog to page 4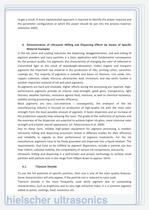
to get a result. A more sophisticated approach is required to identify the power required and the parameter configuration at which the power should be put into the process material. (Hielscher 2005) 4. Demonstration of Ultrasonic Milling and Dispersing Effects by means of Specific Material Examples In the ink, paint and coating industries the dispersing, deagglomeration, and wet-milling of pigment powders and nano particles is a basic application with fundamental consequence for the product quality. For pigments, the characteristic of changing the color of reflected or transmitted light as...
Open the catalog to page 5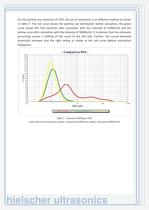
For the particle size reduction of Ti02, the use of ultrasonics is an effective method as shown in table 3. The red curve shows the particle size distribution before sonication, the green curve shows the Ti02 particles after sonication with the intensity of 250Ws/ml and the yellow curve after sonication with the intensity of 500Ws/ml. It is obvious that the ultrasonic processing causes a shifting of the curve to the left side. Further, the curves becomes drastically narrower and the right tailing as visible at the red curve (before sonication) - Comparison Plot - Table 3 - Ultrasonic...
Open the catalog to page 6All Hielscher catalogs and technical brochures
-
Ultrasonic Process Lab
1 Pages
-
Ultrasonic Wire Cleaning
4 Pages
-
Ultrasonic Applications
1 Pages
-
Hielscher Ultrasonic Sieves
2 Pages