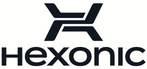

Catalog excerpts
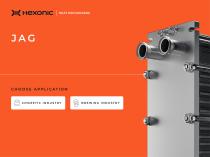
choose application COSMETIC INDUSTRY BREWING INDUSTRY
Open the catalog to page 1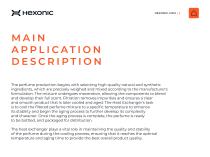
MAIN APPLICATION DESCRIPTION The perfume production begins with selecting high-quality natural and synthetic ingredients, which are precisely weighed and mixed according to the manufacturer's formulation. The mixture undergoes maceration, allowing the components to blend and develop their full scent. Filtration removes impurities and ensures a clear and smooth product that is later cooled and aged. The Heat Exchanger’s task is to cool the filtered perfume mixture to a specific temperature to enhance its stability and begin the aging process to further develop its complexity and...
Open the catalog to page 3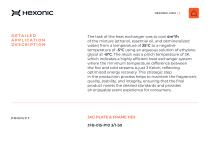
The task of the heat exchanger was to cool 4m3/h of the mixture (ethanol, essential oil, and demineralized water) from a temperature of 25°C to a negative temperature of -5°C using an aqueous solution of ethylene glycol at -8°C. The result was a pinch temperature of 3K, which indicates a highly efficient heat exchanger system where the minimum temperature difference between the hot and cold streams is just 3 Kelvin, reflecting optimized energy recovery. This strategic step in the production process helps to maintain the fragrance's quality, stability, and integrity, ensuring that the...
Open the catalog to page 4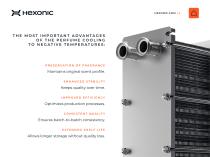
Maintains original scent profile. Enhanced Stability Keeps quality over time. Improved Efficiency Optimizes production processes. Consistent Quality Ensures batch-to-batch consistency. Extended Shelf Life Allows longer storage without quality loss
Open the catalog to page 5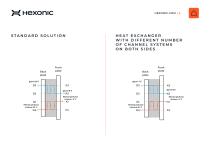
standard solution
Open the catalog to page 7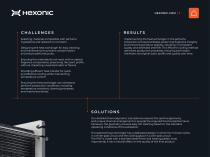
Selecting materials compatible with perfume ingredients and resistant to corrosion. Implementing the heat exchanger in the perfume production process facilitates preserving fragrance integrity and enhancing product stability, resulting in consistent quality and extended shelf life. This efficient cooling method optimizes production processes, ensuring each batch maintains its original scent profile and quality over time. Designing the heat exchanger for easy cleaning and maintenance to prevent contamination and ensure perfume purity. Ensuring the materials do not react with or absorb...
Open the catalog to page 8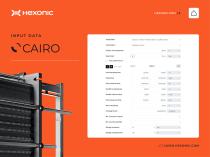
input data
Open the catalog to page 9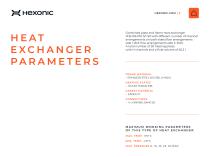
HEAT EXCHANGER PARAMETERS Combined plate and frame heat exchanger JFB-015-P10 3/1-50 with different number of channel arrangements on both sides (flow arrangements side 1: 8x3, flow arrangements side 2: 25x1). A total number of 50 heating plates with H channels and a fluid volume of 20,3 l. frame material – stainless steel AISI 316L (1.4404) gasket material – epdm ht M A X I M U M W O R K I N G P A R A M E T E R S OF THIS TYPE OF HEAT EXCHANGER max. temp. 170°C
Open the catalog to page 10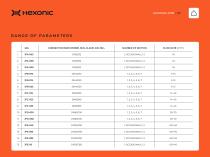
CONNECTION SIZE DIN11851, SMS, CLAMP AISI 316 L
Open the catalog to page 11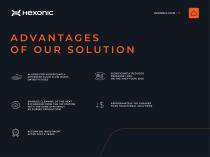
a d v a n t A g e s of our solution Allows for significantly different fluid flow rates on both sides Significantly reduced pressure loss on the high-flow side Enables cleaning of the heat exchanger from the CIP station with the same efficiency as during production Approximately 15% cheaper than traditional solutions Return on investment after j
Open the catalog to page 12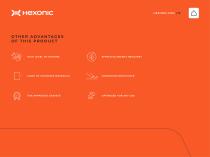
O T H E R A D V A N T A G E S OF THIS PRODUCT high level of hygiene effective energy recovery made of stainless materials corrosion resistance
Open the catalog to page 13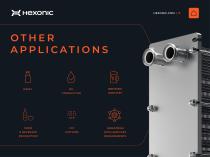
other applications dairy with sanitary
Open the catalog to page 14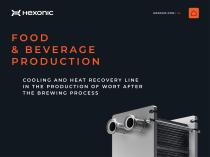
PRODUCTION C o o l i n g a n d h e a t r e c o v e r y l i n e i n t h e p r o d u c t i o n o f w o r t a f t e r the brewing proc
Open the catalog to page 15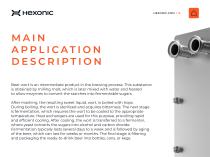
MAIN APPLICATION DESCRIPTION Beer wort is an intermediate product in the brewing process. This substance is obtained by milling malt, which is later mixed with water and heated to allow enzymes to convert the starches into fermentable sugars. After mashing, the resulting sweet liquid, wort, is boiled with hops. During boiling, the wort is sterilized and acquires bitterness. The next stage is fermentation, which requires the wort to be cooled to the appropriate temperature. Heat exchangers are used for this purpose, providing rapid and efficient cooling. After cooling, the wort is...
Open the catalog to page 16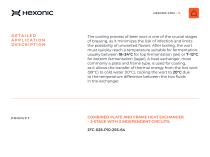
The cooling process of beer wort is one of the crucial stages of brewing, as it minimizes the risk of infection and limits the possibility of unwanted flavors. After boiling, the wort must quickly reach a temperature suitable for fermentation, usually between 18–24°C for top fermentation (ale) or 7–12°C for bottom fermentation (lager). A heat exchanger, most commonly a plate and frame type, is used for cooling, as it allows the transfer of thermal energy from the hot wort (99°C) to cold water (10°C), cooling the wort to 20°C due to the temperature difference between the two fluids in...
Open the catalog to page 17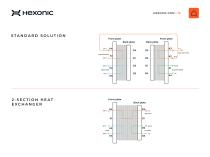
standard solution
Open the catalog to page 19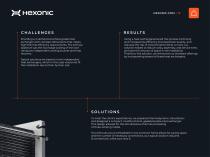
Providing a multifunctional food-grade heat exchanger with compact dimensions that meets high thermal efficiency requirements. The primary objective was the two-stage cooling of the wort using two independent cooling sources and heat recovery. Using a heat exchangerensured the process continuity and increased its efficiency improved beer quality,, and reduced the risk of contamination.What is more, our solution helped to reduce costs, assembly, and service time, and save the amount of space in the installation. Thanks to this solution, we enhanced our standard offerings by incorporating...
Open the catalog to page 20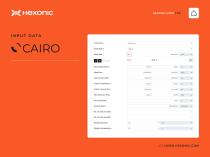
input data
Open the catalog to page 21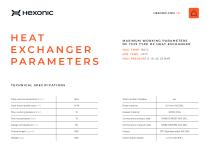
HEAT EXCHANGER PARAMETERS M A X I M U M W O R K I N G P A R A M E T E R S OF THIS TYPE OF HEAT EXCHANGER max. temp. 150°C technical specifications Total volume all sections [litre] Total number of plates Total heat transfer area [m2] Plate material Gasket material Connections product side Connections medium side Intermediary plates STD Stainless steel AISI 304 4 mm AISI 3
Open the catalog to page 22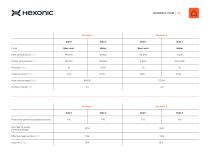
Beer wort Beer wort Flowrate [t/h] Pressure drop [kPa] Heat exchannged [kW] Surface margin [%] Plate arrangement (passeschannels) Number of plates / thermal length Effective heat surface [m2] Volume [litre]
Open the catalog to page 23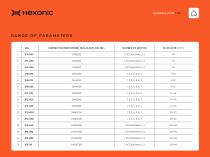
CONNECTION SIZE DIN11851, SMS, CLAMP AISI 316 L
Open the catalog to page 24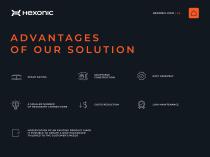
a d v a n t A g e s of our solution Space saving Adaptable construction Easy assembly A smaller number of necessary connections Costs reduction modification of an existing product made it possible to create a new exchanger tailored to the customer's need
Open the catalog to page 25All HEXONIC CZ s.r.o. catalogs and technical brochures
-
LF heat exchanger applications
12 Pages
-
JR heat exchangers applications
13 Pages
-
DNA heat exchangers applications
24 Pages
-
JAD heat exchanger applications
24 Pages
-
Custom heat exchangers
15 Pages
-
Economizer HEXONIC DNA ECO
9 Pages
-
Heat exchangers HEXONIC RAD
5 Pages
-
HAD
7 Pages
-
DNA
5 Pages
-
JAD
13 Pages
-
Asymetric BPHE (en)
5 Pages
-
Dry coolers (EN)
11 Pages
-
HEXONIC KATALOG (EN)
17 Pages
-
BPHE
17 Pages
-
JAG SHIELD
7 Pages
-
HEAT EXCHANGERS POOL
15 Pages
-
Technical card R
3 Pages
-
Technical card Luna
2 Pages
-
BRAZED PLATE HEAT EXCHANGERS
15 Pages
Archived catalogs
-
JAG PLATE HEAT EXCHANGER
13 Pages
-
Oil Coolers
11 Pages
-
Pool
15 Pages
-
P-line
11 Pages
-
JAD
15 Pages
-
HAD
7 Pages
-
BPHE
13 Pages
-
Dry cooler
11 Pages
-
ST
3 Pages
-
L-line
3 Pages
-
DNA ECO
1 Pages
-
R-line
3 Pages
-
Luna
3 Pages
-
Shell and tube
3 Pages
-
Safe plate
3 Pages
-
Pool
15 Pages
-
P-line
3 Pages
-
PHE
3 Pages
-
L-line
3 Pages
-
JAD
3 Pages
-
Industrial
7 Pages
-
HAD
3 Pages
-
DNA
5 Pages
-
Custom
3 Pages
-
P-line
3 Pages