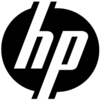

Catalog excerpts
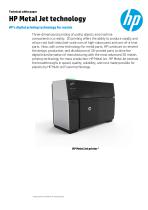
Technical white paper HP Metal Jet technology HP’s digital printing technology for metals Three-dimensional printing of useful objects and machine components is a reality. 3D printing offers the ability to produce rapidly and at low cost both industrial-scale runs of high-value parts and one-of-a-kind parts. Now, with a new technology for metal parts, HP continues to reinvent the design, production, and distribution of 3D-printed parts to drive the digital transformation of manufacturing with the most advanced 3D metals printing technology for mass production: HP Metal Jet. HP Metal Jet extends the breakthroughs in speed, quality, reliability, and cost made possible for plastics by HP Multi Jet Fusion technology. Image shown may differ from actual product.
Open the catalog to page 1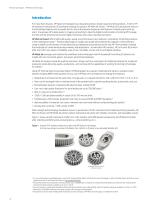
Technical white paper | HP Metal Jet technology Introduction For more than 30 years, HP inkjet technologies have disrupted and led a broad range of printing markets. In 2014, HP introduced a revolutionary 3D printing technology for plastics: HP Multi Jet Fusion. 2 HP Multi Jet Fusion places drops of functional liquid agents onto a powder bed to control the physical properties and features of plastic parts point-bypoint. It leverages HP’s deep assets in imaging and printing to take the digital transformation of printing off the page and into a three-dimensional world of highly-functional,...
Open the catalog to page 2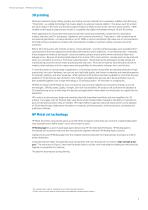
Technical white paper | HP Metal Jet technology 3D printing Whereas manufacturing by milling, grinding, and cutting removes material from a workpiece, additive manufacturing— “3D printing”—is a digital technology that creates objects by selective material addition. This allows each 3D-printed part to be unique in the same way that each page printed by an inkjet or laser printer can have unique content. 100% variable content page to page and part to part is a capability that digital technologies bring to 2D and 3D printing. Prime applications for 3D-printed metal parts include the functional...
Open the catalog to page 3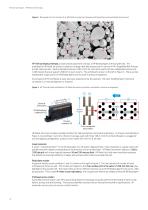
Technical white paper | HP Metal Jet technology Figure 2. Micrograph of cross-section of an HP Metal Jet green part showing metal particles and cured binder (red arrows) HP Thermal Inkjet printheads provide precise placement of drops of HP Binding Agent in the powder bed. The printhead for HP Metal Jet printers is based on a design that has been proven in-service in HP’s PageWide Web Presses and HP Latex printers. Each printhead produces a 108-mm (4.25-inch) print swath with two independent columns of 5,280 nozzles that are spaced 1200/inch in each column. The printhead is shown on the left...
Open the catalog to page 4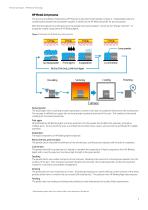
Technical white paper | HP Metal Jet technology HP Metal Jet process The process of building a metal part by HP Metal Jet is described schematically in Figure 4. A detachable build unit, containing the powder bed and powder supplies, is rolled into the HP Metal Jet printer for part production. Note that throughout the printing process, the powder bed may be heated—shown by the “Energy” element—to evaporate volatile components of HP Binding Agent. Figure 4. Schematic of HP Metal Jet printing process Spread powder The build begins with a scanning recoater laying down a uniform, thin layer of...
Open the catalog to page 5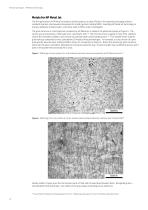
Technical white paper | HP Metal Jet technology Metals for HP Metal Jet The first generation of HP Metal Jet printers will be based on an Open Platform for materials leveraging industrystandard stainless steel powders developed for metal injection molding (MIM). Extending HP Metal Jet technology to process additional metal powders commonly used in MIM is under investigation. The grain structure in a test specimen produced by HP Metal Jet is visible in the photomicrograph of Figure 5. The section was processed by a 10% oxalic acid - electrolytic etch.10 The microstructure is typical of Type...
Open the catalog to page 6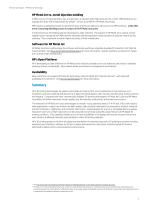
Technical white paper | HP Metal Jet technology HP Metal Jet vs. metal injection molding In MIM, a slurry of metal particles, wax, and polymers is injected under high pressure into a mold. MIM feedstocks are typically less than 93% metal powder by weight 11 versus up to 99% for HP Metal Jet printing. MIM requires a debinding process to remove the wax, and this can add up to 20 hours to the MIM workflow. Unlike MIM, a time-consuming debinding process is not part of the HP Metal Jet process. In both processes, the binding polymer decomposes under sintering. The polymer in HP Metal Jet is used...
Open the catalog to page 7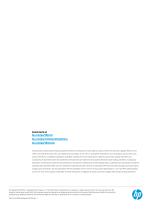
Learn more at hp.com/go/3Dprint hp.com/go/JetFusion3Dsolutions hp.com/go/3Dmetals This document contains forward-looking statements within the meaning of the safe harbor provisions of the Private Securities Litigation Reform Act of 1995. Such statements involve risks, uncertainties and assumptions. If such risks or uncertainties materialize or such assumptions prove incorrect, the results of HP and its consolidated subsidiaries could differ materially from those expressed or implied by such forward-looking statements and assumptions. All statements other than statements of historical fact...
Open the catalog to page 8All Hewlett Packard catalogs and technical brochures
-
HP Jet Fusion 4200
12 Pages
-
HP Jet Fusion 5200 Series
12 Pages
-
HP Jet Fusion 540 3D Printer
4 Pages
-
VESTOSINT® 3D Z2773
2 Pages
-
HP 3D High Reusability PA 12
2 Pages
-
HP 3D High Reusability PA 11
2 Pages
-
HP 3D PA 12 Glass Beads
2 Pages
-
Product datasheet
4 Pages