Catalog excerpts
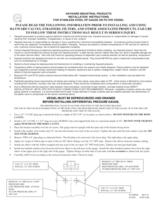
1. Hayward guarantees its products against defective material and workmanship only. Hayward assumes no responsibility for damage or injuries resulting from improper installation, misapplication, or abuse of any product. 2. Hayward assumes no responsibility for damage or injury resulting from chemical incompatibility between its products and the process fluids to which they are subjected. Compatibility charts provided in Hayward literature are based on ambient temperatures of 70F and are for reference only. Customer should always test to determine application suitability. 3. Consult Hayward literature to determine operating pressure and temperature limitations before installing any Hayward product. Note that the maximum recommended fluid velocity through any Hayward product is eight feet per second. Higher flow rates can result in possible damage due to the water hammer effect. Also note that maximum operating pressure is dependent upon material selection as well as operating temperature. 4. Hayward products are designed primarily for use with non-compressible liquids. They should NEVER be used or tested with compressible fluids such as compressed air or nitrogen. 5. Systems should always be depressurized and drained prior to installing or maintaining Hayward products. 6. Temperature effect on piping systems should always be considered when the systems are initially designed. Piping systems must be designed and supported to prevent excess mechanical loading on Hayward equipment due to system misalignment, weight, shock, vibration, and the effects of thermal expansion and contraction. 7. Because PVC and CPVC plastic products become brittle below 40F, Hayward recommends caution in their installation and use below this temperature. 8. Published operating torque requirements are based upon testing of new valves using clean water at 70F. Valve torque is affected by many factors including fluid chemistry, viscosity, flow rate, and temperature. These should be considered when sizing electric or pneumatic actuators. 9. Due to differential thermal expansion rates between metal and plastic, transmittal of pipe vibration, and pipe loading forces DIRECT INSTALLATION OF METAL PIPE INTO PLASTIC CONNECTIONS IS NOT RECOMMENDED. Wherever installation of plastic valves into metal piping systems is necessary, it is recommended that at least 10 pipe diameter in length of plastic pipe be installed upstream and downstream of the plastic valve to compensate for the factors mentioned above. THE DIFFERENTIAL GAUGE IS FACTORY MOUNTED TO THE MOUNTING BRACKET. THE TOP OF THE GAUGE IS MARKED WITH AN HӒ INDICATING THE HIGH PRESSURE (RIGHT SIDE OF THE GAUGE) ғ LҒ IS FOR THE LOW PRESSURE (LEFT SIDE OF THE GAUGE) 1. Use a 1/2-13 UNC plug tap to thread the body to a depth of 5/8Ԕ 1/8є in two places as shown below. DO NOT PENETRATE THE BODY CAVITY. 2. Install a 1/2-13 UNC x 1 1/2Ԕ long set screw (SCR65C) into each tapped body hole to a maximum depth of 3/4. DO NOT OVER TIGHTEN and/or PENETRATE THE BODY CAVITY. 3. Place the bracket assembly over the set screws. The gauge must be upright with the open end of the bracket facing down. 4. Install a flat washer, lock washer and 1/2Ԕ nut into the bracket over each of the set screws. Tighten the nuts until the lock washer is just flat. DO NOT OVER TIGHTEN. 5. Remove TWO 1/4 pipe plugs as indicated below. The left plug to be removed is the lower plug. The right plug is the upper plug. 6. Apply two wraps of Teflon tape to each of the two 90 elbow fittings over the 1/4 NPT ends. Remove the elbows from the stainless tubing. 7. Install one elbow with the Teflon wrapped end into each of the two open 1/4Ԕ NPT body holes. Tighten one turn past hand tight. 8. Install one braided stainless hose from the left lower elbow to the left port on the gauge. Install the other braided stainless hose from the right elbow in the upper port to the right side of the gauge. Tighten fittings on both ends of each tube with two wrenches to obtain leak free joints. 9. Carefully refill Vessel according to the enclosed Instruction sheet. Check for leaks. > REMOVE 1/4 PIPE PLUG ԓHIGH PRESSURE SIDE HIGH PRESSURE SIDE, ATTACH HOSE TO HIGH PRESSURE SIDE 1/4Ԕ NPT TAP TAP 1/2-13 X 5/8Ԕ DEEP INSTALL 1/2 SET SCREW REMOVE 1/4Ԕ PIPE PLUG LOWӔ PRESSURE SIDE LOW PRESSURE SIDE, ATTACH HOSE TO LOW PRESSURE SIDE 1/4 NPT TAP TAP 1/2Ԕ-13 X 5/8 DEEP INSTALL 1/2Ԕ SET SCREW FLTDPISS REV D 8/18/99 ECR 819R size="-1">
Open the catalog to page 1All Hayward Industries catalogs and technical brochures
-
NPP0412A - TB Series in GFPP
2 Pages
-
Industrial Product Guide
164 Pages
-
Hayward Condensed Product Guide
36 Pages
-
Chemical Resistance Guide
13 Pages
-
WPP-19 Corrosion-Resistant Pumps
20 Pages
-
ACT-06 Actuation and Controls
32 Pages
-
Solenoid Valves - IOM
4 Pages
-
Pneumatic Actuator Model PCD/PCS
10 Pages
-
Electric Actuator Model EJM
6 Pages
-
Bag Filter - PVDF
2 Pages
-
Differential Pressure Gauge
1 Pages
-
Bag Filter - PPL
2 Pages
-
Duplex Basket Strainers
4 Pages
-
Cartridge Filter
2 Pages
-
Simplex Basket Strainers
2 Pages
-
Duplex Bag Filter
2 Pages
-
Y Strainers
2 Pages
-
QIC Valves
2 Pages
-
Y Check Valves
2 Pages
-
Pressure Regulators
2 Pages
-
Vacuum Breaker
2 Pages
-
Needle Valves
1 Pages
-
Universal Stopcock
2 Pages
-
Three Way True Union Valves
2 Pages
-
Gauge Guards
2 Pages
-
True Union Ball Check Valves
2 Pages
-
Foot Valve Screens
1 Pages
-
Diaphragm Valves 3" to 6"
2 Pages
-
Diaphragm Valves 1/2" to 2"
2 Pages
-
Bulkhead Fittings
2 Pages
-
Swing Check Valves
2 Pages
-
Butterfly Valves 14" to 24"
2 Pages
-
Relief Valves
2 Pages
-
Angle Valves
2 Pages