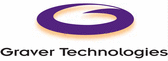
Catalog excerpts

Technical Brief LIQUID PROCESS FILTERS GRAVER TECHNOLOGIES 1-888-353-0303 www.graver tech.com TB–004 Backwash Procedure for Graver VTEC and ZTEC Series Cartridges In order to have a successful cartridge backwash process, the liquid flux needs to be controlled. Graver recommends that the forward liquid flow rate through the cartridge not exceed 10 liters per minute per 10 inch pleated cartridge. This procedure is written for single 10 inch long elements in the filter housing. For longer elements or multi-round housings, please consult Graver. VENT V3 V1 INLET OUTLET • Check to make sure that there is a minimum of a 12 inch long pipe run on the downstream side of the housing, prior to the T joint that leads to valves 3 and 4. This pipe will function as a water reservoir to promote an effective pneumatic-hydraulic pulsating backwash method. V4 R1 AIR INLET • Record the cartridge clean pressure drop across the filter V2 housing at 10 liter per minute flow rate. • Initiate the backwash when the pressure drop DRAIN across the filter housing is four times the initial delta pressure. • For applications where process fluid flow can not be interrupted, it is recommended to install two filter housings in parallel so one can be online while the other is in backwash mode. • Please refer to schematic and note the valve positions prior to initiating backwash. • V1 and V3 are in open position. V2 and V4 are in closed position. • Air pressure regulator R1 needs to be set at 5 to 6 psig. • Note: The R1 regulator is needed to regulate air flow rate. The rate of air brought into the housing should match the amount escaping through V2 or the filter will balloon up from inside-out, damaging the filter integrity. It is recommended to start the backwash at lower pressure and only increase pressure after thoroughly inspecting and evaluating the effectiveness of the backwash. Do not exceed 6 psig back pressure. • It is optional to introduce a valve at the housing head’s vent port. • To initiate backwash, close/open the following valves in the indicated sequence: • Open V2 (let all the liquid drain prior to initiating backpressure, open vent if necessary) • Close vent • Close V3 • Close V1 • Open and close V4 to create a pulsing effect with the compressed air. • To return to normal process flow, follow the indicated sequence: • Close V4. • Open V3. • Open V1. Let the liquid flow flush out the contaminant through the drain. • Close V2. TB-004 3-09
Open the catalog to page 1All Graver Technologies catalogs and technical brochures
-
GLP
2 Pages
-
Citadel
2 Pages
-
Stratum™ C Series
8 Pages
-
Healthcare Brochure
4 Pages
-
Beverage Brochure
6 Pages
-
Products
2 Pages
-
Compressed Gas Filters
8 Pages
-
Exhaust Filters
4 Pages
-
Air Intake Panel Filter
6 Pages
-
Air Intake Filter
4 Pages
-
Coalescing Filters
4 Pages
-
Liquid Filter Housings
7 Pages
-
Low Pressure Gas Filters
4 Pages
-
Oil Mist Coalescers
2 Pages
-
Nitric Acid Filters
4 Pages
-
Ecosorb ® S-406
1 Pages
-
Ecosorb ® C-945
1 Pages
-
Ecosorb ® C-941
1 Pages
-
Ecosorb ® C-908
1 Pages
-
GTX 323-E Brochure
8 Pages
-
Stratum Series Brochure
8 Pages
-
Scepter Product Brochure
8 Pages
-
Vacuum Filters
4 Pages
-
Air - Gas Filter/Separators
6 Pages
-
Housing & Elements
2 Pages
-
Air & Gas Filters
2 Pages
-
W-762 MSDS
4 Pages
-
S-406 MSDS
4 Pages
-
C-906 MSDS
4 Pages
-
W-701
1 Pages
-
S-405
1 Pages
-
C-902
1 Pages
-
Metsorb® HMRG
2 Pages
-
Metsorb® HMRP
2 Pages