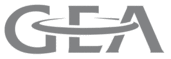

Catalog excerpts
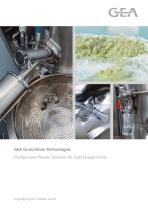
'«cce?, Cfcertr iitcrrr. mtccr, uu,,, GEA Granulation Technologies Multipurpose Process Solutions for Solid Dosage Forms engineering for a better world
Open the catalog to page 1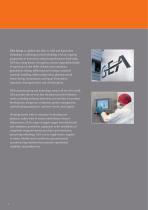
GEA Group is a global specialist in solid and liquid dose technology. Combining trusted technology with an ongoing programme of innovation and price/performance leadership, GEA has a long history of expertise and an unparalleled depth of experience in the fields of batch and continuous granulation, drying, pelletizing and coating, contained materials handling, tablet compression, pharmaceutical freeze drying, fermentation and liquid formulation, separation, homogenization and cell disruption. With manufacturing and technology centres all over the world, GEA provides the services that the...
Open the catalog to page 2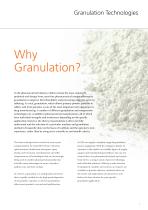
Granulation Technologies Why Granulation? In the pharmaceutical industry, tablets remain the most commonly produced oral dosage form; most fine pharmaceutical compounds require granulation to improve their flowability and processing properties prior to tableting. As such, granulation, which allows primary powder particles to adhere and form granules, is one of the most important unit operations in drug manufacturing. A number of different granulation and compression technologies are available to pharmaceutical manufacturers, all of which have individual strengths and weaknesses depending on...
Open the catalog to page 3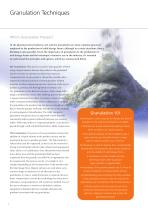
Granulation Techniques Which Granulation Process? In the pharmaceutical industry, wet and dry granulation are most common processes employed in the production of solid dosage forms, although in certain situations, direct blending is also possible. Given the importance of granulation in the production of oral dosage forms and the technique’s extensive use in the industry, it’s essential to understand the principles and options, which are summarised below. Dry Granulation: This process is used to form granules without using a liquid solution, because the product to be granulated may be...
Open the catalog to page 4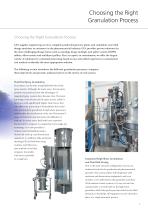
Choosing the Right Granulation Process Choosing the Right Granulation Process GEA supplies engineering services, complete production/process plants and standalone oral solid dosage machines to customers in the pharmaceutical industry. GEA provides proven solutions for the most challenging dosage forms such as oncology drugs, multiple unit pellet system (MUPS) tablets, effervescents and multilayer pellets. Also, as experts in containment, we offer the largest variety of solutions for contained processing, based on our unrivalled experience in containment risk analysis to identify the most...
Open the catalog to page 5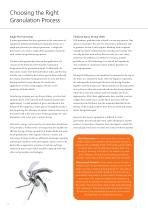
Choosing the Right Granulation Process Single Pot Processing Fluidized Spray Drying (FSD) A mixer/granulator that dries granules in the same piece of FSD produces granules from a liquid in a one-step process. One equipment without discharging is commonly known as a option is to produce the active in the primary production step single pot processor (or one-pot processor). A single pot as granules, so that it only requires blending with excipients processor is, in essence, a high shear granulator enhanced suitable for direct compression for secondary processing. This with various integrated...
Open the catalog to page 6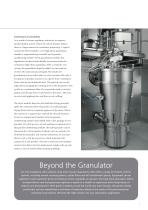
Continuous Granulation As a result of various regulatory initiatives to improve product quality and to reduce the risk of product failure, there is a huge interest in continuous processing. A typical system has three modules: a wet high shear granulation module, a segmented dryer module and a granuleconditioning module. In the granulation module, dry ingredients are dosed individually or premixed into the continuous high shear granulator. After a small dry mix section, the granulation liquid is added, so each particle receives the same amount of liquid. The whole wet granulation process...
Open the catalog to page 7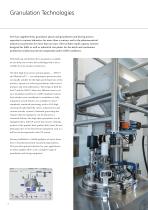
Granulation Technologies GEA has supplied shear granulator plants and granulation and drying process expertise to various industries for more than a century, and to the pharmaceutical industry in particular for more than 50 years. This includes small capacity systems designed for R&D as well as industrial size plants for the batch and continuous production of pharmaceutical compounds under cGMP conditions. With both top and bottom drive granulators available, we can help you to select the technology that is most suitable for your product and process. The GEA high shear mixer and granulators...
Open the catalog to page 8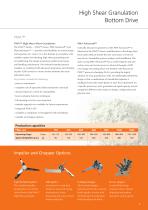
PMA™ High Shear Mixer Granulators The PMA™ family — PMA™ classic, PMA-Advanced™ and PharmaConnect™ — provides total flexibility in system design and capacities of 1-1800 L. It is the ultimate in versatility, with modular options for blending, high shear granulating and wet pelletizing. The design maximises product processing and handling containment. User-selected standard process modules are combined with advanced automation and cleaning-in-place (CIP) systems to create custom solutions that meet individual needs. Key features include the following: • process containment • complete ease of...
Open the catalog to page 9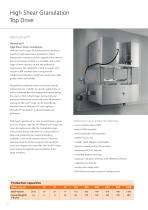
UltimaGral™ UltimaGral™ High-Shear Mixer Granulators With the Gral™ range, GEA pioneered the market for top-driven high shear mixer granulators. Still in demand after numerous product upgrades, this state-of-the-art processing workhorse is available with a wide range of bowl capacities to suit any production requirement. The equipment is built to comply with current cGMP standards and is recognised by companies worldwide as being low maintenance, high quality, robust and reliable. Designed for production-scale functionality, special mixing tools are available for specific applications, as...
Open the catalog to page 10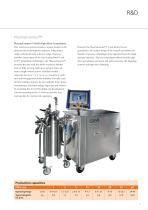
PharmaConnect™ PharmaConnect™ R&D High Shear Granulation This innovative system provides a unique benefit to the pharmaceutical development industry, integrating a single control unit with a diverse range of process modules. Based upon GEA's class-leading PMA™ and Gral™ granulation technologies, the PharmaConnect™ provides the user with the ability to process batches from as little as 100 g, right up to 25 kg or more, all from a single control system. Standard module capacities are set at 1, 3, 5, 10, 15, 20, 30 and 60 L (with each unit being geometrically scalable). Critically, each of...
Open the catalog to page 11All Grasso International catalogs and technical brochures
-
Chiller GEA BluAir
52 Pages
-
GEA Hilge NOVALOBE
76 Pages
-
Batch Formula® Test Mixer
8 Pages
-
Containment Technology
20 Pages
-
The GEA Pharma Solids Center
20 Pages
-
GEA Screw Packages
20 Pages
-
GEA Blu Chillers
16 Pages
-
Process Automation Solutions
8 Pages
-
Omni control panel
12 Pages
-
Hygienic Valves and Components
278 Pages
-
LHP-NDC
2 Pages
-
LHP-DAD
2 Pages
-
Compression heat pumps
12 Pages
-
GEA screw compressors
8 Pages
-
GEA Grasso M Series
2 Pages
-
FES Motor Starter
2 Pages
-
FES Ammonia Dryer
2 Pages
-
FES Galaxy Series
2 Pages
-
GEA OmniTM control panel
12 Pages
-
Ammonia Dryer
2 Pages
-
Grasso DX R
4 Pages
-
GEA AWP product program
12 Pages
-
Bock HG Compressors - R410A
20 Pages
-
GEA Grasso Ammonia Dryer
2 Pages
-
GEA Bock Plusbox
8 Pages
-
GG Purger
5 Pages
-
Grasso BluAstrum
4 Pages
-
GEA Grasso chillers
12 Pages
-
GEA Grasso GSC
4 Pages
-
5HP Series
2 Pages
-
GEA Piston and Screw Compressors
12 Pages
-
Bock Compressor Units
44 Pages
-
Bock CO2 Verdichter
56 Pages
-
GEA Bock Open Type Compressors F
64 Pages
-
Bock ATEX Compressors
20 Pages
-
Catalogue Mobile Applications
100 Pages
-
HG HC
32 Pages
-
Grasso 12 Series
2 Pages
-
GM
2 Pages
-
5 HP
2 Pages
-
GEA Grasso 12E series
2 Pages
-
control devices
4 Pages
-
Sc series
12 Pages
Archived catalogs
-
GEA Grasso 5HP Series
16 Pages
-
Crasso reciprocating series
8 Pages
-
FX series
4 Pages
-
chillers
8 Pages
-
Grasso 6
2 Pages
-
Grasso Ammonia Dryer (GAD)
4 Pages