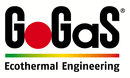
Catalog excerpts
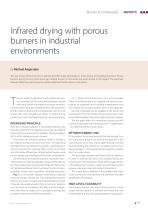
Burner & Combustion Infrared drying with porous burners in industrial environments by Michael Angerstein The use of gas infrared burners in general provides huge advantages in many drying and heating processes. Porous burners, being the only short-wave gas infrared burners in the world, are quite special in this regard. The particular features offered by porous burners will be addressed further down in this article. hey are ready for operation in just a matter of minutes, meaning that the long heat-up phase needed with many convection heaters is no longer necessary. And yet, when using gas infrared burners, the heat transferred is often so high that the drying phase can be much shorter than with circulating air dryers, or higher drying performance can be achieved with the same drying time. Operating principle Heat from infrared radiation is transmitted without any kind of contact from the radiation source (the gas infrared burner) to the recipient of the radiation. The dry air allows 100 % of this radiation to pass through. Only when the infrared radiation meets a surface is the radiated energy converted into heat. This operating principle will be very familiar to anyone in a wintery environment sensing the warming effect of the sun on their skin. The highly efficient gas infrared radiant heaters used for low-energy space heating work in a quite similar fashion. Gas infrared burners used for drying in industrial environments are burners that are operated using a combustion air fan. This provides them among other things with better control facilities and allows them to achieve the kind of reproducibility in output that is required in industrial processes. Fig. 1 is a schematic diagram showing an example structure of a gas infrared unit. The individual burners are lined up in a series to create any desired length. Two lines of burners are usually joined to form a ‘twin row’. Single or twin rows have ducts fitted on the sides, and this arrangement then forms a single unit. It is possible to arrange any number of these units behind one another. heat processing Fig. 1 shows two of these twin rows as an example. Please note that the burner is supplied with gas and combustion air separately and is entirely independent from the ambient air circulation system, which is also depicted. Gas and combustion air are supplied to the burner and burned there. The hot surfaces of the burner emit a very even infrared radiation that is then used for drying or heating. The hot gases from the combustion process and the solvents evaporated in the drying process – usually steam – are collected via the suction ducts. Optimum energy use If the product to be dried permits, the heat energy from the combustion process can be further exploited. In this case, only part of the flow is discharged through the roof, thus preventing the ambient air circulation system from being saturated – for example with the vaporous solvent, which is usually steam. The discharged portion must have fresh air added to it, which is achieved by means of a corresponding valve control system. The largest part of the still-hot gases remain in the ambient air circulation system and are blown via the pressure-side ducts onto the product to be dried. This means that, in addition to the radiated heat, there is also convection, thus deriving the maximum possible benefit from the energy. High level flexibility Gas infrared burners are large-surface burners, which means that the radiation is emitted very evenly from the entire radiating surface. By arranging burners as appropri-
Open the catalog to page 1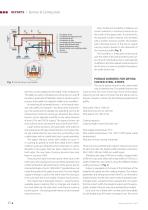
Burner & Combustion Also of interest is the ability to balance out certain variations in moisture content across the width of the paper web. To achieve this, the required number of burner rows are fitted with a ‘profile correction’ system. This enables each individual burner in the row to supply varying output, based on the demands of the moisture profile (Fig. 2). The humidity is measured continuously over the width of the web and the burner output of each individual burner is automatically modified so that the residual moisture beyond the IR zone is as even as possible throughout the...
Open the catalog to page 2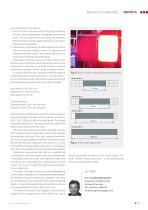
Burner & Combustion joint was fitted for two reasons: 1. The first is that in the event that the strip stops suddenly, the rows can be folded away and operated in low-load mode. This ensures that the strip does not overheat. When the strip is moving again, production can be resumed almost immediately. 2. Furthermore, in the interest of easier maintenance, where strip is running at a height of over 2 m, platforms are integrated into the dryers. This enables easy access to the burners while they are folded away. And replacing a burner is also very simple. Simply remove the four screws on the...
Open the catalog to page 3All GoGaS Goch GmbH & Co. KG catalogs and technical brochures
-
High intensity heaters
8 Pages
-
Control System TriControl
4 Pages
-
Brochure Metal fibre burner
4 Pages
-
Brochure Ceramic burner
3 Pages
-
Solar air system LUBI Wall
10 Pages
-
Stadium heating system
2 Pages
-
Patio heaters VARIOMAX
2 Pages