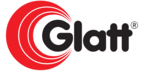

Catalog excerpts
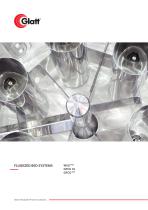
Glatt. Integrated Process Solutions.
Open the catalog to page 1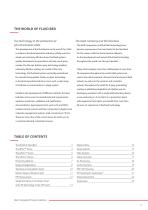
THE WORLD OF FLUID BED Top technology in the production of pharmaceutical solids. The Glatt company and the fluid bed. The Glatt Corporation and fluid bed technology have The development of the fluid bed since the end of the 1950s become synonymous. Our heart beats for the fluid bed. is unique in the pharmaceuticals industry. Initially used as a For this reason, Glatt has had a decisive influence simple yet extremely effective dryer, fluid bed systems on the development and spread of fluid bed technology quickly developed into granulators with the use of spray throughout the world over the...
Open the catalog to page 3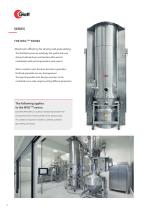
SERIES THE WSG PRO SERIES Maximum efficiency for drying and granulating. The fluid bed ensures an amazingly fast, gentle and even drying. Fluid bed dryers are therefore often used in combination with vertical granulators (wet mixers). When a nozzle is used, the dryer becomes a granulator. Fluid bed granulates are very homogeneous. The type of granulate (size, density, porosity) can be controlled over a wide range by setting different parameters. The following applies to the WSG PRO series: Each WSG PRO offers an optimum relationship between the air volumetric flow and the quantity of the...
Open the catalog to page 4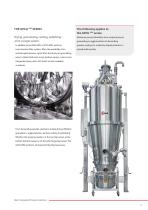
The following applies to the GPCG PRO series: Drying, granulating, coating, pelletizing – all in a single system. Maximum process flexibility: from simple drying to In addition to the WSG PRO, a GPCG PRO, with the powder coating. For uniformly shaped products in twin-chamber filter system, offers the possibility of an reproducible quality. granulating or agglomeration to demanding uninterrupted process. Apart from the drying or granulating insert, a Glatt HS Wurster insert (bottom spray), a rotor insert (tangential spray) and a CPS insert are also available as options. From demanding powder...
Open the catalog to page 5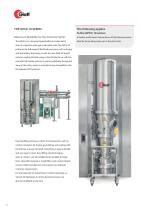
The following applies to the GPCG 10 series: Maximum flexibility for the technical center A flexible multi-talent that performs all fluid bed processes: The GPCG 10 is conceived specifically for smaller batch sizes. It is ideal for scale-ups to the pilot scale. The GPCG 10 performs the full range of fluid bed processes, such as drying and granulating (top spray or with the new Glatt HP nozzle system), coating (bottom spray in the HS Wurster or with the new Glatt HP nozzle system) as well as pelletizing (tangential spray in the rotary insert or manufacturing micropellets with the patented...
Open the catalog to page 6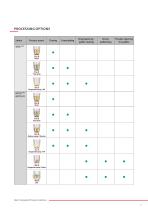
PROCESSING OPTIONS Series Process insert Drug layering / pellet coating Direct pelletizing Powder layering for pellets Bottom spray / Wurster Tangential spray / Rotor
Open the catalog to page 7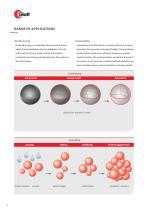
RANGE OF APPLICATIONS Gentle drying. Fluid bed drying is an especially effective way of drying Granulating in the fluid bed is a modern method of creating solids. During fluidization, liquid is withdrawn from the granulates from powder using liquid bridges. The granulation entire surface of every single particle. The benefits: liquid used for spraying can either be aqueous or contain excellent heat exchange, ideal drying time. The product is organic solvents. The moist granulates are dried at the end of also dried gently. the process and, if necessary, cooled. Fluid bed granulates are loose...
Open the catalog to page 8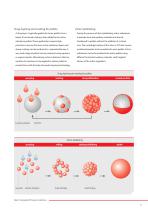
Drug layering and coating for pellets. Direct pelletizing. A drug layer is typically applied to starter pellets from a During the process of direct pelletizing, active substances liquid. A functional coating is then added to the active in powder form and auxiliary materials are directly substance pellets. These applications require high transferred to pellets without the addition of a starter precision to ensure that even active substance layers and core. The centrifugal motion of the rotor or CPS disc causes dense coatings can be produced in a reproducible way. A moistened powder to be...
Open the catalog to page 9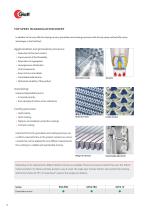
TOP SPRAY IN GRANULATION INSERT In addition to the very effective drying process, granulation and coating processes with the top spray method offer many advantages in the fluid bed. Agglomeration and granulation processes: » Reduction of fine dust content » Improvement of the flowability » Elimination of segregation » Homogeneous distribution of all components » Easier to form into tablets » Controllable bulk density Granulation nozzle Metal sieve fabric Conidur bottom Wedge-wire bottom Nozzle height adjustment » Optimized solubility of the product Instantizing: Improved dispersibility due...
Open the catalog to page 10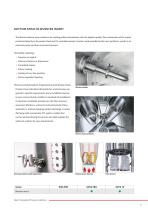
BOTTOM SPRAY IN WURSTER INSERT The Wurster bottom spray method is for coating pellets and particles with the highest quality: The combination of the nozzle positioned directly in the product bed and the controlled product motion made possible by the inner partitions, results in an extremely quick and thus economical process. Versatile coating: » Aqueous or organic » Polymer solutions or dispersions » Controlled release » Enteric coating » Coating of very fine particles » Active-ingredient layering Process and product. Experience and know-how. Products have individual characteristics, and...
Open the catalog to page 11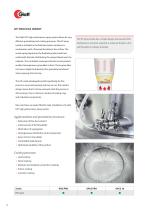
HP PROCESS INSERT The Glatt HP® high-performance spray system allows for very effective granulating and coating processes. The HP spray nozzle is installed in the fluid bed system container in combination with a flow bed that directs the air flow. The The HP spray nozzle has a simple design and requires little maintenance. Incorrect assembly is ruled out thanks to the well thought-out design principle. nozzle sprays liquid into the fluidized product bed from underneath the bed, distributing the sprayed liquid over the material. The controlled movement of both air and product enables...
Open the catalog to page 12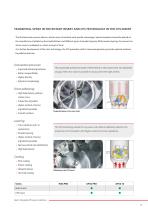
TANGENTIAL SPRAY IN THE ROTARY INSERT AND CPS TECHNOLOGY IN THE CPS INSERT The fluid bed rotor process allows a whole series of methods with specific advantages. Special emphasis should be placed on the manufacture of pellets by direct pelletization and different types of powder layering. With powder layering, the amount on starter cores is multiplied in a short amount of time! As a further development of the rotor technology, the CPS procedure with its improved geometry provides optimal solutions for pellet production. Granulation processes: » Improved dissolving behavior » Better...
Open the catalog to page 13