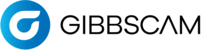

Catalog excerpts

New Business Venture Enabled by CNC and CAM Software Rob Pleas holds a machined tripod-head bracket, during inspection, displaying solid models of brackets in GibbsCAM, which directly opens product and part designs he creates with SolidWorks. When Rob Pleas (pronounced “place”) took the initiative to expand his fabrication business into new areas, he soon realized that manual machines would not be able to keep up with increasing production demands. His new product lines also required extensive programming and testing before production could begin. A more efficient, easy to use and costeffective method was needed. Pleas originally founded The Welding Place, a 1,600 sq. ft. facility in Puyallup, WA, to make custom ornamental railings, gates and fences. When the economy went into recession in 2008, Pleas’ shop survived by providing repair and fabrication services, and also by producing new products, such as a cargo carrier for the Polaris RZR ATV. During this time Pleas also took the opportunity to develop his photography business, a venture that required tripod attachments. The cost of available products was prohibitive and, Pleas joked, he had to adhere to his wife’s restrictive “If you can build it, you can’t buy it.” Pleas had learned manual machining by watching educational videos, and used his manual lathe and mill to prototype a tripod head. “The market offered high-end professional heads that weighed 3 lbs. or more,” said Pleas. “I wanted to create a lighter model for people who did not want the extra weight and expense. My tripod head weighs 1.5 lbs., uses solid aluminum for two L-brackets, instead of tubing with good bearings and nice features.” When he had a working prototype, he approached a Seattle photographic store, which suggested changes that Pleas incorporated. The store liked the result, took a few tripod heads on consignment, and soon began carrying them. Later, at an exposition where photographic vendors, buyers and users congregated to view new products, the Seattle store introduced a customer who needed a way to quickly flip his camera between horizontal and vertical positions. Pleas agreed to build an attachment, launching a sec- ond product, a folding 5” L-bracket with locking pin, which he has since built in a larger version to accommodate larger cameras. Pleas quickly realized that working with manual machines was not productive. It took nine hours to machine parts for a complete prototype head, and revisions took nearly as long. For production, he would need a CNC, and with no desire to learn and use G-code programming, he would need CAM software. In 2012, Pleas sold his manual machines to acquire a used, 1997 Lagun 717-S CNC mill in disrepair. During restoration, Pleas developed a good relationship with Lagun’s service department, which he deemed “fantastic.” The machine has a 58” x 11” table, XYZ travels of 32”, 17” and 7”, 16” knee and 40 taper 55-4,250 RPM spindle. Despite the large amount of restoration work required, the machine acquisition was a sound investment. Pleas then purchased an entry-level CAM system. Although it was almost adequate for programming simple welding supports, it proved to be too problematic, taking hours to program simple parts and yielding programs that nearly always required debugging. When one problem was fixed, another would appear. A program might simulate properly, and then fail at the machine. He could count on losing two to four pieces on a 10-piece run. “I would spend hours, and sometimes days, programming, testing and troubleshooting,” Pleas explained. “I lost all confidence in programming and had no confidence in that software. Compounding problems, the CAM and CAD companies blamed each other.” GibbsCAM Cut Part Rendering displays the toolpath and surface finish Rob Pleas will get at the machine after post-processing the toolpath with the GibbsCAM post, developed precisely to take advantage of the control’s capabilities. Cut Part Rendering, which can use different colors for tools or operations, here displays two tripod brackets as tool chamfers edges. MANUFACTURING NEWS SOUTHWEST
Open the catalog to page 1
Developing his photographic venture during the recent recession, Rob Pleas created these tripod accessories, using GibbsCAM for CNC programming, and his Lagun 717-S for machining components. His first three products, left to right: folding L-bracket; gimbal tripod head to support a camera and long lens for smooth panning; and quick-release balancing clamp for mounting camera or lens on some tripod heads. The general purpose CAD system worked well for ornamental weldments and supporting hardware, but it took too much time to make even minor changes, which prototyping frequently requires. A...
Open the catalog to page 2
To verify toolpath and check for gouges, Pleas relies on Cut Part Rendering, GibbsCAM’s toolpath simulation, which allows verifying single operations or the whole program, at any time during programming or design. His representative said that what he sees on the screen is what he will get on the part, both toolpath and finish. “I did not believe it,” said Pleas, “so I tried to make it fail, using various ways to fool the system, but it never failed. Now I rely on it.” Post-processing proved to be as exacting as toolpath simulation. Programs ran exactly as simulated. “Most surprising of all,...
Open the catalog to page 3All GibbsCAM catalogs and technical brochures
-
GibbsCAM MTM
2 Pages
-
GibbsCAM® 12
2 Pages
-
SolidSurfacer
4 Pages
-
5-Axis MultiBlade
4 Pages
-
System Management Tombstone
2 Pages
-
stems Production G
6 Pages
-
GibbsCAM 13
2 Pages
-
Solar Energy
5 Pages
-
DHP 5000
2 Pages
-
TOMBSTONE MANAGEMENT SYSTEM
2 Pages
-
GibbsCAM 2015 Enhancements
4 Pages
-
Why GibbsCAM?
2 Pages
-
GibbsCAM 5-Axis
2 Pages
-
TOMBSTONE MANAGEMENT SYSTEM
2 Pages
-
CAD Interoperability
2 Pages
-
GibbsCAM® SolidSurfacer®
2 Pages
-
GibbsCAMWire-EDM
2 Pages
-
GibbsCAM® MTM
2 Pages
Archived catalogs
-
Gibbs Overview
2 Pages