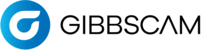

Catalog excerpts
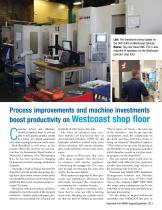
Left: The tombstone being loaded on the DHP 5000 at Westcoast Cylinder. Below: The new Haas UMC-750 5-axis machine in operation on the Westcoast Cylinder shop floor. Customer service and efficiency should go hand-in-hand. If you are able to turn quality product around in a hurry, it’s almost guaranteed your client is going to seek you out for more. Brad Remillard is well aware of the positive effects this can have on your bottom line. As Automation Team Leader at Westcoast Cylinders, New Westminster, B.C., he has been involved in changing its processes to better manage production demands. “Basically, I work as liaison between the shop floor and the production group, giving them ideas about where certain products should be produced on the shop floor, and I help them work on process improvements,” he notes. Westcoast cylinders produces cylinders designed to meet the needs of the resource industries - lumber, pulp and paper production, ore processing, the oil patch and hundreds of other heavy-duty jobs. The lines of cylinders they produce include cast head heavy-duty air and hydraulic cylinders, NFPA air and hydraulic cylinders, welded style, servo driven cylinders, full custom cylinders, plus a wide selection of heavy-duty accessories. The teams at Westcoast, like every other shop, recognize that they have to compete with similar suppliers. Considering the struggle the U.S. economy has had over the past few years, that market has become tighter. With numerous upgrades to their processes and equipment, Westcoast has effectively managed this competitive environment for a number of years. One of the simplest sounding solutions they’ve come up with is turning batch runs, blanking out cylinder models that can then be refined as necessary. “We’ve taken our heads - the end caps of the cylinders - and we pre-turn the components, stock the components on the shelf, and then drill them closer to being on-demand,” Remillard explains. “This reduces set-up costs by giving us the flexibility to run minimum quantities which therefore results in a lot less work-in-progress on the shop floor.” The pre-turned piece could then be specified with different port positions, needle valve positions, lugs welded on for mounting type features, etc. Westcoast uses GibbsCAM’s Tombstone Management software and Machine Simulation to run many of these small runs on the company’s DHP 5000. With this setup, many components can be run with little to no setup time and little to no operator intervention. “It’s the ability to import Solidworks assemblies into GibbsCAM that gave us Reprinted from MP&P, August/September 2013
Open the catalog to page 1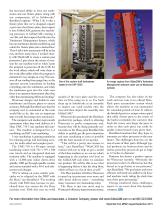
the increased ability to have our tombstones and our fixture plates, along with our components, all in Solidworks,” Remillard explains. “What I do is take a fixture plate that we’ve designed, import a part onto that fixture plate, then import it into GibbsCAM, generate the machining processes in GibbsCAM creating a .vnc file, and then import that file into the Tombstone Management System, which has our tombstone already modeled up, and orient the fixture plate onto a desired face. Then I tell it how many parts will be in the run, and how many faces. I worked closely with WestCAM to create a...
Open the catalog to page 2All GibbsCAM catalogs and technical brochures
-
GibbsCAM MTM
2 Pages
-
GibbsCAM® 12
2 Pages
-
SolidSurfacer
4 Pages
-
5-Axis MultiBlade
4 Pages
-
System Management Tombstone
2 Pages
-
stems Production G
6 Pages
-
GibbsCAM 13
2 Pages
-
Solar Energy
5 Pages
-
TOMBSTONE MANAGEMENT SYSTEM
2 Pages
-
GibbsCAM 2015 Enhancements
4 Pages
-
Why GibbsCAM?
2 Pages
-
GibbsCAM 5-Axis
2 Pages
-
TOMBSTONE MANAGEMENT SYSTEM
2 Pages
-
CAD Interoperability
2 Pages
-
GibbsCAM® SolidSurfacer®
2 Pages
-
GibbsCAMWire-EDM
2 Pages
-
GibbsCAM® MTM
2 Pages
Archived catalogs
-
Gibbs Overview
2 Pages