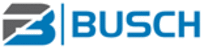
Catalog excerpts
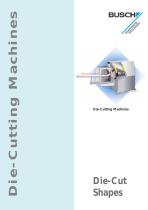
Die-Cutting Machines Die-Cutting Machines Die-Cut Shapes
Open the catalog to page 1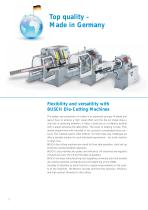
Top quality – Made in Germany Flexibility and versatility with BUSCH Die-Cutting Machines The design and production of a label is an expensive process. Material and layout have to achieve a high visual effect and the die-cut shape plays a vital role in attracting attention. A label, a brochure or a children’s booklet with a shape enhances the sales effect. The scope of shaping is wide, from almost simple forms with rounded or cut corners to complicated fancy contours. The material used is often difficult. To meet these new challenges we offer a suitable solution for each individual...
Open the catalog to page 2
Contents Top quality – Made in Germany What is produced on the machine? – Die-cutting with counter-pressure Production methods for different types of die-cutting 8 Cutting dies Model overview Ancillary equipment Technical data
Open the catalog to page 3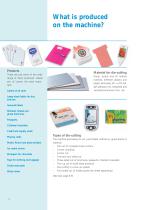
What is produced on the machine? These are just some of the wide range of items produced. Labels are, of course, the most important. Paper, board and all related material, different plastics and plastic laminates, PP- or PE-foil, self-adhesive foil, tempered and varnished aluminium foil, etc. Labels of all sorts Large-sized labels for tins and jars Inmould labels Stitched, folded and glued brochures Passports Children’s booklets Credit and loyalty cards Playing cards Plastic flower and plant stickers Ice cream covers Wrappers for chocolate Tags for clothing and luggage Glued note pads...
Open the catalog to page 4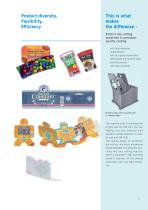
Product diversity, Flexibility, Efficiency This is what makes the difference – BUSCH die-cutting machines in premiumquality casting – – with high damping characteristics with an optimal torsionallyrigid design principle for high punching power with high durability Machine body with punching ram in casting design The machine body is manufactured in grey cast iron (EN-GJL); the ram, feeding tray and clamping arms (except A series machine) in nodular cast iron (EN-GJS). The casting design of all BUSCH die-cutting machines guarantees perfect parallels of cutting die, punching ram and cutting...
Open the catalog to page 5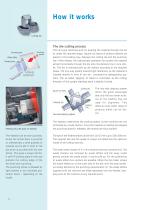
The die-cutting process Punching power Punching ram Waste slitter Clamping arm The ram-type machines work by pushing the material through the die to create the required shape. Square-cut stacks of printed material are placed in the feeding tray, between the cutting die and the punching ram. After release, the hydraulically operated ram pushes the material almost horizontally through the die onto the delivery tray in one stroke. The die is manufactured by die makers according to the required shape. The one-way system ensures tight tolerances, as the material is inserted directly in front of...
Open the catalog to page 6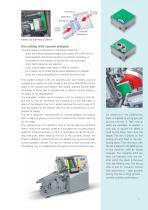
Punching power Punching ram Waste slitter Clamping arm Feeding tray with stack of material Die-cutting with counter-pressure Counter-pressure is required for minimising tolerances – when die-cutting embossed paper and plastics (PP or PE foil) for inmould labels and similar articles to counteract stretching or movement of the material during the die-cutting process – when tight tolerances are required – when cutting large-sized labels of difficult material – for 4-sided cut of folded quires (sheet separating for diaries) – when die-cutting tempered and varnished aluminium foil The...
Open the catalog to page 7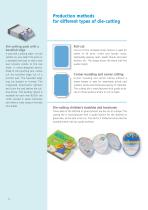
Production methods for different types of die-cutting Die-cutting pads with a bevelled edge A pad with a sloping edge – an eye catcher on your desk! The print on a standard note pad or sticky note pad remains visible to the last sheet. A newly-designed device, fitted to the punching ram, carries out the bevelled edge cut of a printed pad. The bevelled edge may be straight or formed. The integrated pneumatics tightens and turns the pad before the cutting stroke. This ancillary device is available for each new BUSCH die cutter (except A series machines) and offers a wide range of formats and...
Open the catalog to page 8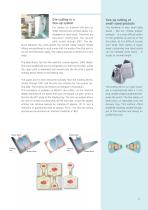
Die-cutting in a two-up system Two-up cutting of small-sized products For saving on material the pre-cut sheet contains two printed labels, e.g. detergent or food labels. The prints are laid-down interlocked, the second print turned through 180°. The distance between the prints shows the normal waste margin! Waste slitters are positioned in such a way that the waste of the first print is cut off and falls down easily. The cutting process is carried out in two steps. The handling of very small label stacks – like our ‘cheese wedge’ example – is a most difficult action on the guillotine as...
Open the catalog to page 9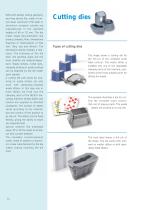
DIES with perfect cutting geometry and long service life, made of normal steel, aluminium HSS steel or aluminium tungsten carbide are manufactured in the standard heights of 60 or 70 mm. The die maker needs documentation like product samples, films, dimensional drawings or transmissions of files (dxf, dwg, eps and others). The dimensions should indicate a tolerance. The thickness of the die back, the grinding angle and the inner chamfer are material-dependent. Waste slitters, milled slots, clamping surfaces or guide surfaces can be attached by the die maker upon request. A cutting die with...
Open the catalog to page 10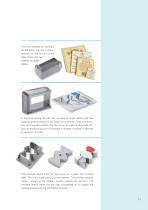
This is an example for cutting a deckle edge. The die is manufactured for the full cut of the label shape with two screwed on waste slitters. A brochure cutting die with two screwed on waste slitters and two optional scribing slitters for the back of the booklet, fitted at the bottom on the guide surface. The die-cut is not made at the guide surface, as the brochure (or for example a children’s booklet) is stitched or glued on this side. This example shows a die for the full-cut of a plastic foil inmould label. The cut is made using counter-pressure. The counter-pressure matrix – shown in...
Open the catalog to page 11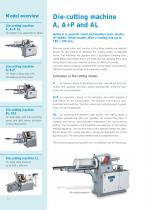
Model overview Die-cutting machine A, A+P, AL For smaller runs, especially for labels Die-cutting machine A, A+P and AL Series A is used for small and medium runs, mostly for labels. These models offer a cutting size up to 180 x 180 mm. Machine construction and function of the three models are identical except for the method of releasing the cutting stroke, as specified below. The machines are supplied with 5 adjustable clamping arms, waste slitters and holders which are fitted into the clamping arms, thus being able to reach any required position for slitting the waste. Once the stack of...
Open the catalog to page 12All Gerhard Busch EBB catalogs and technical brochures
-
Die Cutting Machines
24 Pages
-
Pile hoists
4 Pages
-
Joggers
6 Pages
-
model ZFB 32 inline
4 Pages
-
Pile Turner
18 Pages