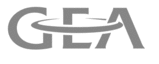

Catalog excerpts
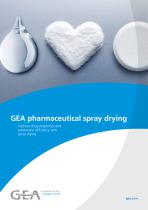
GEA pharmaceutical spray drying Improve drug properties and production efficiency with spray drying
Open the catalog to page 1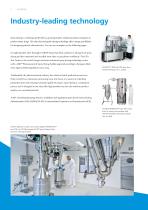
Industry-leading technology Spray drying is a technique preferred by a growing number of pharmaceutical companies to produce better drugs. This ultra-fast and gentle drying technology offers unique possibilities for designing particle characteristics. You can see examples on the following pages. For eight decades, GEA, through its NIRO® brand, has been a pioneer in all aspects of spray drying and has contracted and installed more than 10,000 plants worldwide. The GEA Test Center is the world’s largest and most advanced spray drying technology center with a GMP* Pharmaceutical Spray Drying...
Open the catalog to page 2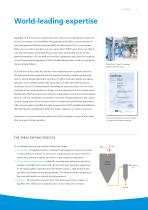
World-leading expertise Regardless of the size of your organisation, GEA experts are well prepared to match the services you require. From feasibility testing during initial R&D, to the production of your Investigational Medicinal Product (IMP) for clinical trials, GEA is your partner. When you are ready to purchase your own spray dryer, NIRO® spray dryers are offered with instrumentation and designs that can document reproducible results for later approval procedures. GEA can fulfil your need for a production spray dryer for excipients, Active Pharmaceutical Ingredients (API) or finished...
Open the catalog to page 3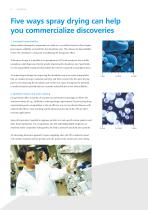
Five ways spray drying can help you commercialize discoveries 1. Increased bioavailability Many modern therapeutic compounds are stable in a crystalline form but often display poor aqueous solubility, and with this, low dissolution rates. This reduces the bioavailability of the API, sometimes to the point of nullifying the therapeutic effect. With spray drying, it is possible to co-precipitate an API with a polymer into a stable amorphous solid dispersion, thereby greatly improving the dissolution rate. Specifically, it is the unparalleled drying rate that enables the API to be captured in...
Open the catalog to page 4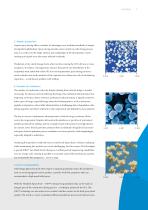
3. Aseptic production Aseptic spray drying offers a number of advantages over traditional methods of aseptic drying like lyophilization. Spray drying provides more control over the drying process and, as a result, over the shape, density and morphology of the final product. Lower running and capital costs also mean reduced overheads. Production of dry sterile dosage forms often involves mixing the API with one or more excipients. To achieve a homogeneous mixture, the particle size distribution of the excipient(s) must match that of the API. In a one-step operation, spray drying can turn a...
Open the catalog to page 5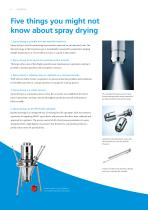
Five things you might not know about spray drying 1. Spray drying is suitable for heat-sensitive materials Spray drying is used for processing heat-sensitive materials on an industrial scale. The thermal energy in the hot process gas is immediately consumed by evaporation, keeping droplet temperatures at a level where no harm is caused to the product. 2. Spray drying turns liquid into particles within seconds The large surface area of the droplets provides near instantaneous evaporation, making it possible to produce particles with amorphous structure. 3. Spray drying is relatively easy to...
Open the catalog to page 6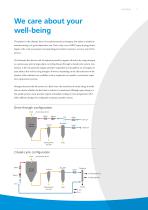
We care about your well-being The patient is the ultimate focus of any pharmaceutical company, but safety in medicine manufacturing is of great importance too. That’s why every NIRO® spray drying project begins with a risk assessment, incorporating preventative measures at every step of the process. We eliminate the obvious risk of explosion posed by organic solvent(s) by using nitrogen as a process gas and, in large plants, recycling the gas through a closed-cycle system. Less obvious is the risk posed by organic powders suspended in atmospheric air and again we may address this risk by...
Open the catalog to page 7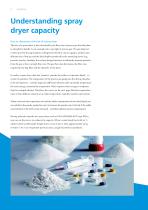
Understanding spray dryer capacity How to characterize the size of a spray dryer The size of a spray dryer is best described by the flow rate of process gas that the plant is intended to handle. As an example, take 1250 kg/h of process gas. The gas disperser in the top of the drying chamber is designed at this flow rate to supply a uniform and efficient mix of hot gas and the feed droplets produced by the atomizing device (e.g. pressure nozzle). Similarly, the cyclone design functions to efficiently separate particles from the gas at the 1250 kg/h flow rate. The gas flow also determines the...
Open the catalog to page 8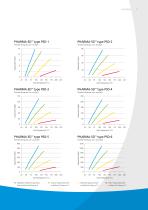
Inlet Temperature (°C) Methylene Chloride Evaporation Rate at Outlet Gas Temp 40 °C Inlet Temperature (°C) Acetone Evaporation Rate at Outlet Gas Temp 50 °C Ethanol Evaporation Rate at Outlet Gas Temp 70 °C Water Evapor
Open the catalog to page 9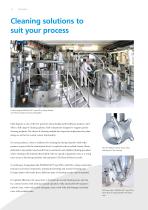
Cleaning solutions to suit your process Custom-designed PHARMA-SD™ type PSD-4 drying chamber roof with gas disperser and top of bag filter. Plant hygiene is one of the first priorities when dealing with healthcare products. GEA offers a full range of cleaning options, with components designed to support specific cleaning methods. The choice of cleaning method has important implications for plant design as well as for control system functionality. For some products, a hose is sufficient for cleaning the drying chamber while other products require that the atomization device is replaced with...
Open the catalog to page 10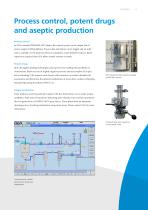
Process control, potent drugs and aseptic production Process control In GEA’s standard PHARMA-SD™ plants, the control system can be simple, but of course support GMP guidelines. Process data and alarms can be logged and an audit trail is available. As the plant increases in complexity, or pre-defined recipes or batch reports are required, then GEA offers control systems to match. Potent drugs GEA also applies leading technologies and expertise for enabling the possibility of containment. Plants are run in slightly negative pressure and may employ GEA split valve technology. GEA experts work...
Open the catalog to page 11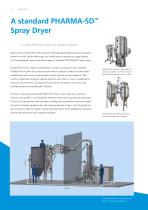
A standard PHARMA-SD™ Spray Dryer A cost-effective path to proven results Based on years of experience with customers of all types (global pharmaceutical companies, producers of API and finished drugs, and small contract manufacture organizations), GEA has developed a proven and robust range of “standard” PHARMA-SD™ spray dryers. Despite the level of customer individuality, in many circumstances GEA’s standard PHARMA-SD™ plants are an ideal and cost-effective solution. With no or only minor modifications, the process set-up and the controls software can be configured. This PHARMA-SD™ type...
Open the catalog to page 12All GEA Westfalia Separator catalogs and technical brochures
-
Pharma Solids Center
20 Pages
-
Crystallization Technology
20 Pages
-
Evaporation Technology
24 Pages
-
Industrial Drying Brochure
10 Pages
-
GEA Blu Chillers - Brochure / EN
16 Pages
-
GEA Powdereye
2 Pages
-
GEA VISIOCOVER
2 Pages