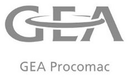
Catalog excerpts
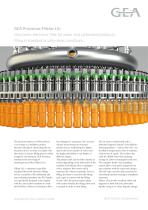
The present tendency of CSD products is to emerge as a healthier product, thereby reducing or eliminating the use of preservatives. In order to comply with the need of a cleaner filling process within a hygienic environment, GEA Procomac introduces the new range of counterpressure fillers Fillstar LXi. Fillstar LXi, a volumetric type filler machine fitted with electronic filling valves, is suitable to fill carbonated and non-carbonated products into PET bottles. It is specifically designed to be coupled with the Airstar blow moulder to create the ONE bloc. Fillstar LXi machines offer: fast changeover; automatic CIP; accurate volume measurement to minimize product losses; small footprint; higher speed with a low number of valves and the highest flexibility to run bottles of different shapes. The product tank can be either annular or central depending on the dimension of the machine. Each filling valve is equipped with a magnetic flow meter which measures the volume of product. Prior to filling, the bottle is raised by the lifting jack to get in contact with the filling nozzle. After the pressurization phase with carbon dioxide, the filling valve stem is opened in order to start filling. The air return is performed with a dedicated separate channel. Even difficult foaming products - such as diet CSD - can be filled at temperatures close to ambient, with no loss of speed. This reduces the need for chilled water thus attaining savings in power consumption and costs. The complete bottle “neck handling" system allows very quick changeover for any container with the same neck design. The CIP cups insertion and extraction for closed-loop internal cleaning is completely automatic. Fillstar LXi provides excellent safety and hygiene for both still and carbonated liquids owing to its clean, hygienic design. engineering for a better world
Open the catalog to page 1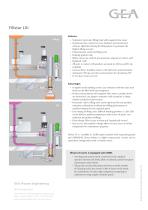
Fillstar LXi Features Filling • Volumetric electronic filling head with magnetic flow meter • Continuous flow control (via new hardware and customized software algorithm) during the filling phase to guarantee the highest filling accuracy • Full pneumatic control of filling cycle • Rotating product tank • Bellow valves are used for pressurisation, separate air return, snift • Pipelined “snift” • All parts in contact with products are made in AISI 304 (AISI 316 available) • Carousel drive: brushless motors with electronic synchronization • Automatic CIP cups insertion and extraction for...
Open the catalog to page 2All GEA Procomac S.p.A. catalogs and technical brochures
-
Gas Cleaning Systems
12 Pages
-
SMART LYO High quality
12 Pages
-
Industrial Drying Brochure
10 Pages
-
CIP/SIP Solutions
20 Pages
-
GEA BluAir
16 Pages
-
DICAR-B™ Carbonation System
2 Pages
-
ABF 1.2 Aseptic Blow Fill
8 Pages
-
GEA Aseptic piston doser
2 Pages
-
GEA Fillstar FX
2 Pages