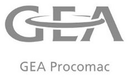
Catalog excerpts
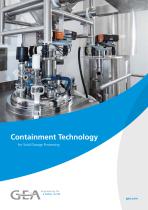
Containment Technology for Solid Dosage Processing
Open the catalog to page 1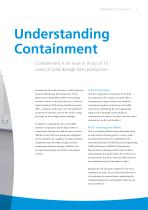
Understanding Containment Containment is an issue in 9 out of 10 cases of solid dosage form production. Containment issues have become a vitally important Containment Experts aspect of solid dosage form production. Active GEA has a long history of expertise in the field pharmaceutical ingredients (APIs) are becoming of containment. The company not only offers a evermore effective, with more than 50% of all new comprehensive range of robust and compliant chemical entities (NCEs) being classified as potent containment products, it also boasts unrivalled (OEL <10 μg/m3); at the same time, the...
Open the catalog to page 3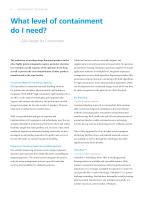
The production of oncology drugs, hormonal products and/or other highly potent compounds requires particular attention: it is essential to avoid exposure of the operators to the drug as well as prevent the cross-contamination of other products manufactured in the same facility. Contained Materials Handling Expertise GEA specializes in contained materials handling solutions for primary and secondary pharmaceuticals and healthcare companies. With BUCK® high containment split butterfly valves, we offer a wide range of technologies and equipment that improve and enhance the efficiency and...
Open the catalog to page 4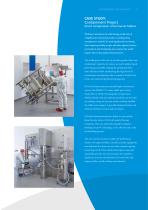
CASE STUDY: Containment Project Direct Compression of Hormonal Tablets Wishing to maximize the solid dosage production of a highly potent hormonal product, a leading drug manufacturer tasked GEA with significantly increasing their output, providing a safer and more efficient factory environment and introducing new systems that would replace the existing isolator-based process. The challenge for GEA was to use their product flow and containment expertise to remove as much isolator-based processing as possible, making the production flow more efficient, whilst maintaining the high levels of...
Open the catalog to page 5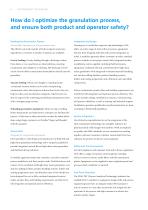
Feeding the Granulation Process Process flow interfaces for the granulation area The effective and safe transfer of both excipients and active ingredients is essential. A number of options are available: Gravity feeding: Gravity loading through a discharge station from above or via a post hoist are ideal solutions, ensuring containment and simplicity of cleaning. API discharge vessels can be used to deliver more potent formulations directly into the granulator. Vacuum feeding: When room height is a limiting factor, a contained vacuum station can be used: incorporating containment valves...
Open the catalog to page 6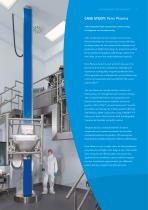
CASE STUDY: Penn Pharma Fully integrated, high-containment, contract drug development and manufacturing After conducting extensive market research, Penn Pharma identified an increased need in the solid dose oncology market for the outsourced development and production of highly toxic drugs. Its production site had been manufacturing potent solid dosage products for more than 20 years but needed additional capacity. Penn Pharma elected to work with GEA because of its proven track record in containment technology and expertise in creating fully integrated production lines. GEA’s approach was...
Open the catalog to page 7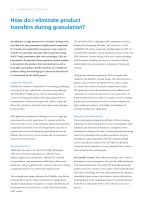
How do I eliminate product transfers during granulation? By definition, a single-pot process is contained, making it the The UltimaPro™-HC is equipped with containment tools for first choice for the granulation of highly potent compounds. loading and discharging (Hicoflex®, MC valves, etc.); a full, No transfers are required between process steps, except to validatable CIP system; contained sampling options or PAT for load the raw materials and unload the dry granules (using end-point determination; and an optimized vacuum system with BUCK high containment split-valve technology). This not...
Open the catalog to page 8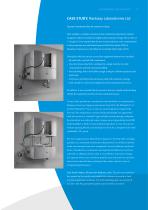
CASE STUDY: Ranbaxy Laboratories Ltd Top-end containment line for anticancer drugs GEA supplied a complete containment line to Ranbaxy Laboratories Limited (Gurgaon, India) to manufacture highly potent anticancer drugs with an OEL of 1–10 μg/m3. It was essential that the process prevented any cross-contamination in the production area and limited operator Real Daily Intake (RDI) of hazardous substances to well within the Acceptable Daily Intake (ADI). During the selection process, several key equipment features were specified: • all units had to provide full containment the entire process...
Open the catalog to page 9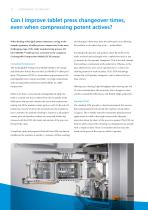
Can I improve tablet press changeover times, even when compressing potent actives? When dealing with highly potent substances, owing to the and cleaning is done away from the tablet press area, allowing complex geometry of tablet presses, compression is the most the machine to do what it has to do — make tablets. challenging stage of the tablet manufacturing process. All GEA MODUL™ tablet presses are based on the company’s Providing both operator and product safety, the ECM can be Exchangeable Compression Module (ECM) concept. easily removed and exchanged with a replacement unit in just 30...
Open the catalog to page 10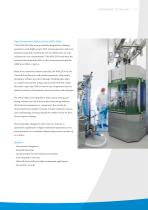
High-Containment Wash-off-Line (WOL-ECM) TThe WOL-ECM has been specifically designed for tableting operations using highly potent APIs to keep operators safe from harmful compounds, without the use of cumbersome air suits, and prevent cross-contamination. The WOL-ECM maintains the concentration of harmful APIs in the environment around the tablet press below 1 pg/m3. Made from corrosion-resistant materials, the WOL-ECM can be removed from the press and washed separately, using strong detergents, without any risk of damage. Washing takes place in a sealed environment using a special wash...
Open the catalog to page 11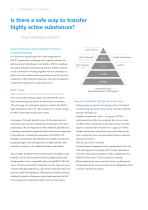
Is there a safe way to transfer highly active substances? Smart Hardware Solutions System Integration with Containment Interfaces (Loading/Unloading) Our distinctive specialization lies in the integration of BUCK containment technology into complete solutions for ® pharmaceutical solid dosage form facilities. With an emphasis on quality and good manufacturing practice (GMP) standards, BUCK® Valve UMC BUCK® Valve UHC BUCK® Valve MC BUCK® Valve HC Hicoflex® Suction Device we are committed to working together with our customers to 10-100 deliver first-class tailored solutions for projects of...
Open the catalog to page 12All GEA Procomac S.p.A. catalogs and technical brochures
-
Gas Cleaning Systems
12 Pages
-
SMART LYO High quality
12 Pages
-
Industrial Drying Brochure
10 Pages
-
GEA BluAir
16 Pages
-
DICAR-B™ Carbonation System
2 Pages
-
GEA Procomac Fillstar LXi
2 Pages
-
ABF 1.2 Aseptic Blow Fill
8 Pages
-
GEA Aseptic piston doser
2 Pages
-
GEA Fillstar FX
2 Pages