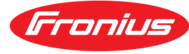

Catalog excerpts
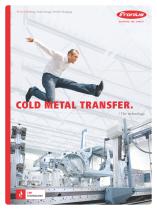
/ Perfect Welding / Solar Energy / Perfect Charging Cold metal transfer. / The technology.
Open the catalog to page 1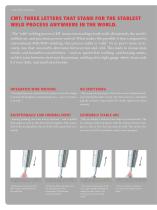
CMT: Three letters that stand for the stablest weld process anywhere in the world. / The “cold” welding process CMT means outstanding results with all materials, the world’s stablest arc, and precision process-control. What makes this possible is that compared to conventional MIG/MAG welding, this process really is “cold”. Or to put it more accurately, one that constantly alternates between hot and cold. This leads to immaculate results and boundless possibilities – such as spatter-free welding- and brazing seams, welded joins between steel and aluminium, welding ultra-light gauge sheets...
Open the catalog to page 2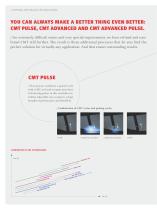
4 / CMT Pulse, CMT Advanced, CMT Advanced Pulse You can always make a better thing even better: CMT Pulse, CMT Advanced and CMT Advanced Pulse. / For extremely difficult seams and very special requirements, we have refined and combined CMT still further. The result is three additional processes that let you find the perfect solution for virtually any application. And that ensure outstanding results. / / / / / / / / / / / / / / / / / / / / / / / / / / / / / / / / / / / / / / / / / / / / / / / / / / / / / / / / / / / / / / / / / / / / / / / / / / / / / / / / / This process combines a pulsed...
Open the catalog to page 4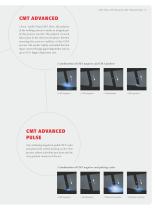
CMT Pulse, CMT Advanced, CMT Advanced Pulse / 5 / / Even “cooler” than CMT. Here, the polarity of the welding current is made an integral part of the process-control. The polarity reversal takes place in the short-circuit phase, thereby ensuring the proven stability of the CMT process. The results: tightly controlled thermal input, extremely high gap bridgeability and an up to 60 % bigger deposition rate. / Combination of CMT negative and CMT positive / By combining negatively poled CMT cycles and positively poled pulsing cycles, this process achieves absolute precision and the very...
Open the catalog to page 5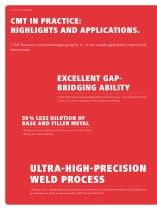
CMT in practice: Highlights and applications. / CMT has some crucial advantages going for it – as our sample applications impressively demonstrate. Excellent gapbridging ability / With CMT Advanced, gap bridgeability increases on e.g. 2 mm aluminium from 1 mm to 2.5 mm as compared with pulsed-arc welding. 50 % less dilution of base and filler metal / Dilution of base and filler metal is as much as 50 % lower, cutting costs when cladding. Ultra-high-precision weld process / Boasting 100 % reproducibility and the best process-control you’ll find anywhere in the world, CMT opens up radically...
Open the catalog to page 6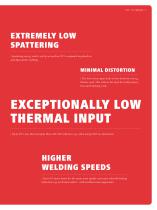
Extremely low spattering / Spattering on e.g. steel is cut by as much as 99 % compared to pulsed-arc and dip-transfer welding. Minimal distortion / The lower heat input leads to less distortion on e.g. thinner steel. This reduces the need for weld preparation and finishing work. Exceptionally low thermal input / Up to 90 % less thermal input than with TIG cold-wire, e.g. when using CMT on aluminium Higher welding speeds / Up to 10 times faster for the same seam quality and same sidewall-wetting behaviour, e.g. on chrome-nickel – with excellent seam appearance.
Open the catalog to page 7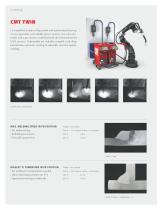
CMT TWIN / A simplified system configuration and synchronised start-up of two separately controllable power sources, two wire electrodes and a gas nozzle, combined with the tried-and-tested CMT process. Unbeatable arc stability coupled with deep penetration, optimum wetting to sidewalls, and low-spatter welding. / CMT Twin weld process MAX. WELDING SPEED IN PB POSITION / No undercutting / Reliable penetration / Virtually spatter-free Vweld = 3.0 m/min VwireL = 15.5 m/min VwireT = 6.2 m/min 407 A BIGGEST ‘a’ DIMENSION IN PB POSITION / No weldment manipulation needed / Ideal weld-seam...
Open the catalog to page 8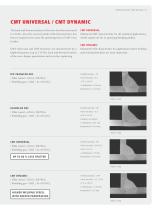
CMT UNIVERSAL / CMT DYNAMIC The back-and-forward motion of the wire has been increased to 130 Hz. Also, the current profile of the characteristics has been re-engineered to raise the operating limit of CMT even further. CMT Universal and CMT Dynamic are characterised by a higher-frequency (up to 130 Hz) back-and-forward motion of the wire, deeper penetration and even less spattering. Dip-transfer arc / Filler metal = G3Si1 / ER70S-6 / Shielding gas = M21 / Ar+18%CO2 CMT Universal Enhanced CMT characteristic for all standard applications, which stands out for its good gap-bridging ability....
Open the catalog to page 9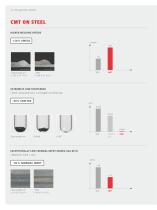
CMT on steel Higher welding speeds Extremely low spattering / Steel, measured over 1 m length of weld-seam Exceptionally low thermal input (mixed gas M 21) / Material: Steel 1 mm kJ/cm
Open the catalog to page 10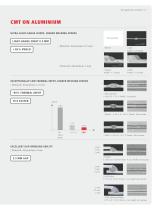
CMT on aluminium Ultra-light-gauge joints, higher welding speeds / Not possible / Pulsed – Vweld = 1.1 m/min Exceptionally low thermal input, higher welding speeds / Material: Aluminium 1.6 mm - 90 % thermal input 10 x faster / TIG cold-wire– I: 84 A, U: 17.4 V, Vweld: 24 cm/min kJ/cm 4.92 / Pulsed – I: 88 A, U: 18.6 V, Vweld: 100 cm/min Excellent gap-bridging ability / Material: Aluminium 2 mm 2 mm 1 mm 2 mm / Pulsed I: 100 A, U: 18.9 V, Vwire: 4.5 m, Vweld: 60 cm/min / CMT Pulse I: 97 A, U: 16.9 V, Vwire: 5 m, Vweld: 60 cm/min 2 mm 2.5 mm 2 mm / CMT Advanced Pulse I: 97 A, U: 11.9 V,...
Open the catalog to page 11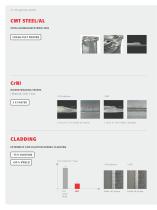
CMT steel/Al Steel/aluminium hybrid join Crash-test proven CrNi Higher welding speeds / Material: CrNi 2 mm Cladding Extremely low dilution during cladding % Fe content in 1st pass / TIG cold-wire
Open the catalog to page 12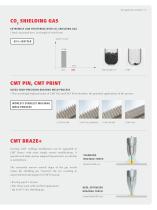
CO2 shielding gas Extremely low spattering with CO2 shielding gas / Steel, measured over 1 m length of weld-seam CMT Pin, CMT Print Ultra-high-precision MIG/MAG weld process / The exceedingly high precision of CMT Pin and CMT Print broadens the potential applications of the process World’s stablest MIG/MAG weld process CMT Braze+ Existing CMT welding installations can be upgraded to CMT Braze+ with some simple system modifications. A special torch body and an adapted characteristic are all that is needed here. STANDARD MIG/MAG TORCH Normal GMA arc The extremely narrow conical shape of the...
Open the catalog to page 13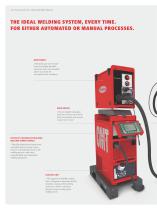
14 / System overview: robots and CMT Manual The ideal welding system, every time. For either automated or manual processes. Wirefeeder / Wirefeed unit with 4-roller drive for feeding the filler metal precisely and smoothly all the way from the wire-spool to the workpiece. Wire buffer / The wire buffer decouples the front and rear wire-drives from one another and ensures smooth wire travel. Digitally controlled MIG/MAG welding power source / The fully digitised microprocessorcontrolled inverter power source ensures unrivalled precision in the welding process, with exact reproducibility and...
Open the catalog to page 14All FRONIUS catalogs and technical brochures
-
Vizor 4000 Plus
1 Pages
-
Fazor 1000 Plus
1 Pages
-
Arctig
4 Pages
-
TransPocket 150/180
4 Pages
-
TPS/i Intelligent REvolution
4 Pages
-
LaserHybrid
1 Pages
-
TRANSPOCKET 180
2 Pages
-
AccuPocket 150/400
16 Pages
-
ACCTIVA Professional Flash
2 Pages
-
ACCTIVA Seller
2 Pages
-
ACCTIVA Standard
2 Pages
-
ACCTIVA Twin 15A
2 Pages
-
ACCTIVA Brochure
8 Pages
-
Plasma welding
4 Pages
-
WF 25i Case
1 Pages
-
WF 25i / VR 4000 / VR 5000
2 Pages
-
LSC
12 Pages
-
Magic cleaner
1 Pages
-
TransPuls Synergic 2700
6 Pages
-
VR 5000 Case
2 Pages
-
TransSteel 3500 / 5000
12 Pages
-
ACCTIVA
8 Pages
-
Flyer Ri charging process
2 Pages
-
Virtual Welding
8 Pages
-
Automated welding systems
10 Pages
-
TransTig 1600 / 1700
6 Pages
-
VarioStar 1500 / 2500 / 3100
2 Pages
-
Solar Electronics
88 Pages
-
SELECTIVA
12 Pages
-
CLAMP CHUCK FMC
1 Pages
-
GRIPPER CHUCK FSG
2 Pages