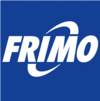

Catalog excerpts
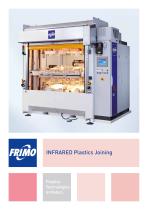
INFRARED Plastics Joining
Open the catalog to page 1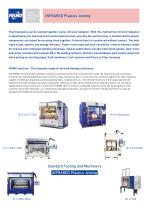
INFRARED Plastics Joining Thermoplastics can be welded together using infrared radiation. With this method the infrared radiation is absorbed by the material and transformed into heat, whereby the surface layer is melted and the plastic components are joined by pressing them together. Infrared heat is transferred without contact. The heat input is fast, specific and energy-efficient. Power-controlled and time-controlled infrared emitters allow for precise and controlled welding processes. Typical applications include instrument panels, door trims and center consoles with complex 2D or 3D...
Open the catalog to page 2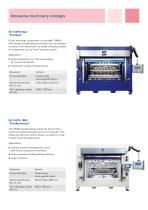
Innovative machinery concepts IR-V-RPS-Maxi "The Maxi" Do you need large components to be welded? FRIMO’s Maxi-design infrared welding unit offers the only standard machine on the market that can handle infrared processes for components such as truck instrument panels. Applications: Large components, e.g. instrument panels for commercial vehicles with multiple welding stations 3 axles using servo-geared motors IR-V-RPS-1800 “The Workhorse” This FRIMO standard design stands the test of time in numerous production projects and is our bestseller. This robust and effective machine design is...
Open the catalog to page 3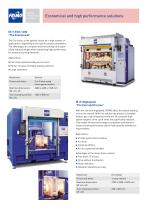
Economical and high performance solutions IR-V-ECO-1600 “The Economical” The Eco-series is the optimal choice for a high number of applications, depending on the specific project parameters. The advantages are compact machinery design and significantly reduced weight while maintaining high performance for numerous joining demands. Applications: Instrument enter C Large panels (airbag and air duct) consoles (multiple welding stations) 2 or 3 axles using servo-geared motors IR-H-Highspeed “The Fast and Precise” With the JoinLine Highspeed, FRIMO offers the fastest welding unit on the market....
Open the catalog to page 4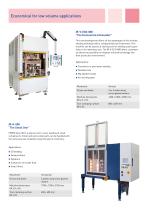
Economical for low volume applications IR-V-ECO-800 “The Economical Allrounder” This new development offers all the advantages of the infrared welding technique with a comparatively low investment. This machine can be used as a starting unit for welding small quantities or for laboratory use. The IR-V-ECO-800 offers customers an attractive possibility to integrate infrared technology into their production environment. Applications: Containers Glovebox speaker boxes ducting pipes Movement: Drives and Axles: Speakers Containers Small 2 axles using servo-geared motors FRIMO also offers a...
Open the catalog to page 5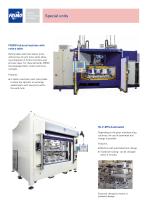
Special units FRIMO Infrared machine with rotary table Rotary tables offer fast station times without loss of cycle times while allowing integration of further functions and process steps. For these demands FRIMO has developed tailor-made machinery concepts. Features: 2-station machinery with rotary table to allow the operator to exchange welded parts with new parts within the weld cycle IR-V-RPS Automated Depending on the given manufacturing solutions, the use of automated tool change is possible Features: Machine with automated tool change. tooling” can be changed within 3 minutes Easy...
Open the catalog to page 6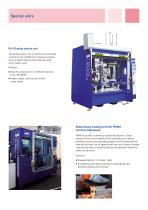
Special units IR-V Double station unit The double station unit is used for the combined manufacturing of different component variants which enables higher output rates by using multi-station units. Features: Ideal for components in 2 different versions (e.g. LHD+RHD) output rates by use of multi cavity molds Robot based welding with the FRIMO JoinLine Highspeed FRIMO also offers numerous automated solutions. These solutions offer more flexibility to the manufacturer. Several welding consoles and assembly grippers can be combined and existing functions can be adapted with the use of robots,...
Open the catalog to page 7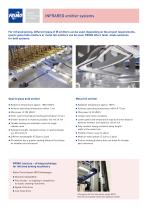
INFRARED emitter systems For infrared joining, different types of IR emitters can be used. Depending on the project requirements, quartz glass bulb emitters or metal foil emitters can be used. FRIMO offers tailor-made solutions Quartz glass bulb emitter ■ Radiation temperature approx. 1800-2400°C ■ Achieves operating temperature within 1 sec ■ Short cycle times (typical heating period about 12 sec) ■ Greater distance to material possible; low risk of fire ■ Flexible heating via individual control of single radiator units ■ Standard straight, standard contour or special design, ■ IR...
Open the catalog to page 8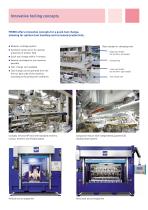
Innovative tooling concepts FRIMO offers innovative concepts for a quick tool change, allowing for optimal tool handling and increased productivity. cartridge system Basic design for changing tools construction for optimal protection of emitter field Upper part holder (for the IR-H: left holder) tool change within 3 minutes cartridges for one machine possible Infrared field change cart available Lower part holder (for the IR-H: right holder) change can be operated from the front or back side of the machine, according to the production conditions Tool change cart Complex infrared (IP) tool...
Open the catalog to page 9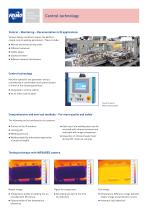
Control technology Control – Monitoring – Documentation in IR applications Various design conditions require the ability to closely control welding parameters. These include: Narrow and broad joining zones Different Visible material thicknesses Control technology Machine operation and parameter entry is controlled by a comfortable touch panel located in either of the following positions: Integrated As an offset control panel Touch screen in offset control panel Comprehensive and new test methods – For more quality and safety The following can be monitored in our systems: Current depth (by...
Open the catalog to page 10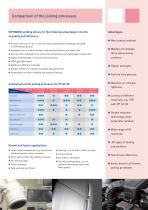
Comparison of the joining processes INFRARED welding allows for the following advantages in terms ■ Particle free; e.g. for air- or oil-ducting components (increasingly indicated ■ Increased use of reinforced high-performance plastics, e.g. glass fiber ■ Use of reinforced plastics for structural components and lightweight construction ■ Higher yield strength in security-relevant areas ■ Welding of different materials ■ Design freedom in regards to complex 3D geometries ■ Productivity, economic viability and energy efficiency Comparison of the joining processes for PP GF 30 Simple machine...
Open the catalog to page 11All FRIMO Group GmbH catalogs and technical brochures
-
Ultrasonic Hand Welding Case
2 Pages
-
Hot Plate Welding
4 Pages
-
Ultrasonic Welding
4 Pages
-
Heat Staking Technology
4 Pages
-
Edgefolding Technology
4 Pages
-
EcoCut Punching Machines
4 Pages
-
FlexTrim Router Systems
4 Pages
-
Hypress Hydraulic Presses
4 Pages
-
CombiCut Punching Machines
4 Pages
-
PURe Plant Technology
8 Pages
-
FlexTrim Millilng
4 Pages
-
FlexTrim Scoring Machines
4 Pages
-
Press Laminating
4 Pages
-
Foam Molds
4 Pages
-
EcoCut Punching Machines
4 Pages
-
ErgoCut Punching Machines
4 Pages
-
Image brochure
16 Pages
-
IMG-Technology
8 Pages
Archived catalogs
-
FRIMO Composites
4 Pages