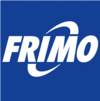

Catalog excerpts
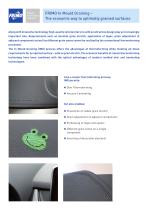
FRIMO In Mould Graining – The economic way to optimally grained surfaces Along with innovative technology high-quality vehicle interiors with an attractive design play an increasingly important role. Requirements such as minimal grain stretch, application of logos, grain adjustment of adjacent components as well as different grain zones cannot be realized by the conventional thermoforming processes. The In Mould Graining (IMG) process offers the advantages of thermoforming while meeting all these requirements for an optimal surface – with no grain stretch. The economic benefits of classic...
Open the catalog to page 2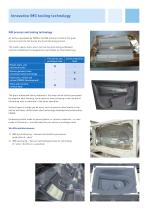
Innovative IMG tooling technology IMG process and tooling technology As further developed by FRIMO, the IMG process transfers the grain structure onto the foil during the thermoforming process. The mold’s upper shell, which carries the grain being embossed onto the molded part is designed air-permeable for thermoforming. Pre-series and prototype tools Serial production tools Plastic tools and aluminum tools Electro-galvanic tools including model technology Steel tools, milled and etched (FRIMO Development) Tools with ceramic surface body The grain-embossed skins produced in this way can be...
Open the catalog to page 3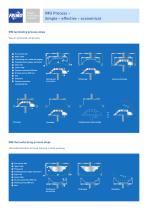
IMG Process – Simple – effective – economical IMG laminating process steps Vacuum laminated components Pre-suction bell Upper table Laminating tool / substrate support Clamping frame (upper and lower) Chain rail Lower table Vacuum connection IMG tool Grained, porous IMG tool Foil Substrate Vacuum connection Vacuum laminating Laminating tool IMG thermoforming process steps Thermoformed skins for back-foaming or back-pressing Pre-suction bell Upper table Plug assist Clamping frame (upper and lower) Chain rail Lower table Vacuum connection IMG tool Grained, porous IMG tool Skin Heating and...
Open the catalog to page 4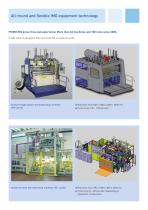
All-round and flexible IMG equipment technology FRIMO IMG know-how and experience: More than 45 machines and 100 tools since 2003. A wide range of equipment that can be tailored to customer needs: EcoForm single-station thermoforming machines (FTE series) VarioForm inline thermoforming machines (FTL series) Mold area from 600 x 1000 to 2000 x 2800 mm Cycle times: 100 – 150 seconds Mold area from 700 x 1000 to 860 x 2700 mm Cycle time 45 – 80 seconds, depending on equipment configuration
Open the catalog to page 5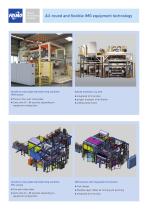
All-round and flexible IMG equipment technology VarioForm rotary table thermoforming machines ■ Three or four-part rotary table ■ Cycle time 45 - 80 seconds, depending on equipment configuration Special machines, e.g. with ■ integrated trim function ■ gripper transport of foil blanks ■ sliding clamp frame VarioForm rotary table thermoforming machines ■ Two-part rotary table ■ Cycle time 45 - 80 seconds, depending on equipment configuration IMG machine with integrated trim function ■ Multiple upper tables for forming and punching ■ Integrated trim function
Open the catalog to page 6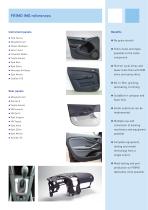
Instrument panels Door panels ■ Grain zones and Logos ■ Shorter cycle times and fewer tools than with RIM skins and spray skins laminating, trimming foam foils single source ■ Mold testing and part laboratory units possible
Open the catalog to page 7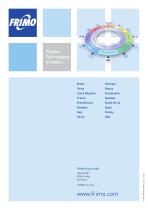
Czech Republic Great Britain South Africa Hansaring 1 49504 Lotte Germany info@frimo.com © FRIMO 08/2012 Subject to change FRIMO Group GmbH
Open the catalog to page 8All FRIMO Group GmbH catalogs and technical brochures
-
Ultrasonic Hand Welding Case
2 Pages
-
Hot Plate Welding
4 Pages
-
Ultrasonic Welding
4 Pages
-
Heat Staking Technology
4 Pages
-
Edgefolding Technology
4 Pages
-
EcoCut Punching Machines
4 Pages
-
FlexTrim Router Systems
4 Pages
-
Hypress Hydraulic Presses
4 Pages
-
CombiCut Punching Machines
4 Pages
-
Infrared Plastics Joining
12 Pages
-
PURe Plant Technology
8 Pages
-
FlexTrim Millilng
4 Pages
-
FlexTrim Scoring Machines
4 Pages
-
Press Laminating
4 Pages
-
Foam Molds
4 Pages
-
EcoCut Punching Machines
4 Pages
-
ErgoCut Punching Machines
4 Pages
-
Image brochure
16 Pages
Archived catalogs
-
FRIMO Composites
4 Pages