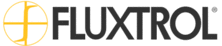
Catalog excerpts
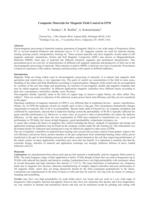
Composite Materials for Magnetic Field Control in EPM V. Neinkov\ R. Ruffini1, A, Kolesnichenko2 1 Fluxtrol Inc. 1388 Atlantic BIvd, Aubum Hills. Michigan 48326. USA 2Nclshape Cast Inc., 17 Lockcrbcc Drive, Valparaiso, IN 46385, USA Abstract Electromagnetic processing of ma tenais requires gnration of ruagnetic field in a very wide range of frequencies (froni DC to scvcral hundred kilohcrt/) and intensifies (up ta 12 J i. AC magnetic Systems arc used for material stirring, castiug, pouring control transportatioiL fonning etc. Th驨se Systems typically may have magnetic circuits made of soft magnetic materials: laminations. ferrites and Sofl Magnetic Composites (SMC) also known as Magnetodielectric Materials (MI)M), Each type of materials h as diffrent electrical, magnetic and mechanical charactcristics. This prsentation gives an overview of ebaracteristics of diff驩rent sofl magnetic materials and perspective of their use in the electromagnetic processing of materials. Main attention is paid to MDM, a relatively new type of materials. Prsentation is bascd on exprience of the authors, litcraturc and discussions with experts in diff驩rent industries. Introduction Magnetic ficlds arc being widcly used in electromagnetic processing of materials. lt is naturel, tbat magnetic field gnration and control play a very important r驴le. The goals of control are concentration of the field in some areas, shielding of the othen* and field distribution according to required pattem. Magnetic field control may be accomplished by van::'ion of the coil turn shape and positiouing, by insertion of non-magnelic shiclds and magnetic tcmplatcs tliat may be called magnetic controllers. In diffrent applications magnetic controllers have diffrent naines according to their r驴le: concentrators, intensifiers, shields, cores, diverfers. Non-magnctic shiclds* typically made in the fonn of copper rings or massive copper blocks, are of (en called "flux robbers". Their use results in rduction of the induction system power factor and efficiency and they are not considered in this paper. Ope rat in g conditions of magnetic materials in EPM is very diffrent than in Iraditional devises 驗 motors* transloraicrs. chokes. etc. In EPM the magnetic circuits are usually open or have a big gap. Tins circumstance drajiialically changes requircments to material, frst of ail to its pcrmcahility. Spcial study made at Kluxtrol Inc. by computer simulation and conflrmed by experiments. sltowcd Uial in induction heating system the penneability of 40-50 is typically sufficicut for good controller performance (f ]. Moreover. in some cases, an excessive value of penneability can reduce the inductor efficiency. At the same time there arc new requircments in HPM arca compared to transformers etc.» stich as good performance in 3D ficlds, low losscs at high frequency. good machiriability* temprature rsistance, etc. A course that contains the basics of magnetic flux control including the theory, methods of simulation and design and application technique guidelincs may be found on the company website under the tab Training [2]. This information was devcloped rnaudy for iuduction heat treating but it may bc efTectively applied to olher areas of EPM. Tlie use of magnetic controllers on induction heat treating coils can provide accurate control of heat panera, improve the coil efficiency and power factor, protect machine or the part components from nnintcndcd heating. better utili/c power transferred to tlie part in local heating processes and reduce cuireut dciuand to the coil thus unproving performance of the whole system. In many appheations controllers give more that one benefit. It is important to mention also that the controller design, slection of material and application technique can strongly influence Itfetimc of heavy loadcd iuduction coils [3|. Materials Laminations are manufacturai from silicon steel and are this material is traditionally used for magnetic field control in EPM. The main frequency range of their application is below 10 kHz though at times they are used at frequencies up to 50 kHz with redueed flux density and intensive cooling. [.animations have very high penneability with maximum values of several thousands and high saturation flux density (1.7-2.0 T), The main drawbacks of laminations are: fiequeucy hmits due to magnetic loss increase. laborious manufacturing of complex shaped controllers and poor perfonnance in iD magnetic ficlds, wherc they arc being intcnsivcly heatcd by the field component petpendicular to the shects* Laminations are rnanufactured in the fonn of sheets or rolls and may be used for very big cores by means of cutting or stamping and assembling. Ferrites may have very high pcrmcabilily (in weak ficlds only!), low losses and can work in a very wide range of frequencies when properly selecled and applied. However tliey have low saturation flux density and Curie temp驩rature, are very sensitive to thermal and mechanical shocks and may not be machined except by grinding and cutting with
Open the catalog to page 1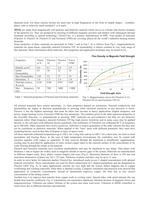
diamond tools. For thse reasons ferrites are used only at high frequencies in the fonn of simple shapes cylinders. plates, rods or rclativcly small standard C or F parts. MDMs arc made from magnctically soft particlcs and diclectric inatcrial whicli serves as a binder and clcctric insulator of the particles [2]. They are produced by pressing of diffrent magnetic powders and binders with subs詩quent thermal treatment according to spcial tcchnology. Fhixtrol Inc. is a primaiy manufacturer of SMC. Four grades of matcrials (Fluxtrol . Fluxtrol 50, Fluxtrol 25 and Feirotron 55911) arc covering...
Open the catalog to page 2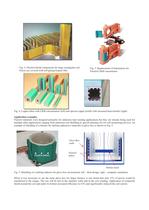
M- 4: Coppcr tube» with I.RM concentrators (left) and spcial copper profile with inercased heat transfer (right) Application cxample* Fluxtrol ma tenais werc destgned primarily for induction heat treating applications but they are already being used for multiple olher applications rangiug from iuduciiou coil shielding to spcial aniecnas for oil well mouitohng devices. An exaniple of shielding of a fiunace for melting radioactive materialsin glove box isshown in Fig. 5. Molten m驪lai Fig .5: Shielding of a melting inductor for glove box environnant: left - final design; right - computer...
Open the catalog to page 3All Fluxtrol catalogs and technical brochures
-
Ferrotron 559H
2 Pages
-
Fluxtrol 50
2 Pages
-
Fluxtrol 25
2 Pages
-
Fluxtrol Brochure
8 Pages
-
Alphaform LF
1 Pages
-
FLUXTROL-A
1 Pages
-
Fluxtrol 100
1 Pages
-
Fluxtrol's AlphaForm
30 Pages
-
fluxtrol Catalog
59 Pages