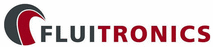
Catalog excerpts
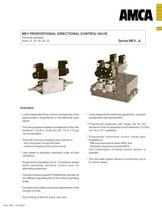
Publ. MEV...A-E-06/07 FEATURES * Load independent flow control corresponds to the spool-position proportional to the electrical input signal. * The pump pressure always corresponds to the user pressure, +3,6,8 or 12 bar (43, 86, 114 or 172 psi) Äp compensator. * The built-in pump-unloading valve results in: - very low power turned into heat; - minimum loading of the prime mover. * User speed is precisely controlled under all load conditions. * Progressive regulating curve; no pressure peaks when switching; sensitive control even for alternating pressures. * Constant working speed of differential cylinders at the different regulating flow to the valve by grinding angle. * Constant recirculation pressure independent of the number of units. * Any limiting of flow for every user port. * Load independent switching adjustment, constant acceleration and deceleration. * Proportional solenoids with longer life for the armature in the oil (explosion proof solenoids “II 2 EEx mII T4 or T5”, available). * Proportional directional control valves also available as: - Manual proportional series MHV and - Hydraulic proportional series MOV. Any combination of these control options is possible. * The sub plate system allows a construction up to 8 control valves. MEV PROPORTIONAL DIRECTIONAL CONTROL VALVE Electrical operation Sizes 12, 16, 20, 25, 32 Series MEV...A
Open the catalog to page 1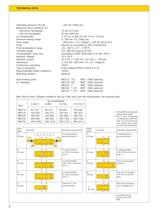
2 TECHNICAL DATA Operating pressure (P,A,B) ...350 bar (5000 psi) Maximum return pressure (T): - aluminium springcaps 15 bar (214 psi) - cast iron springcaps 30 bar (428 psi) Äp compensator 3; 6; 8 or 12 bar (43; 86; 114 or 172 psi) Pressure setting range 5...350 bar (72...5000 psi) Flow range ...800 l/min (...211 USgpm) - with 32 cSt at 40oC Fluid Mineral oil according to DIN 51524/51525 Fluid temperature range -35...+80°C (-31°...+176°F) Viscosity range 2,8...380 cSt, optimal 30 cSt Contamination level max. according to NAS 1638 Class 9 or ISO 18/15 Nominal voltage 12 V, 24 V Nominal...
Open the catalog to page 2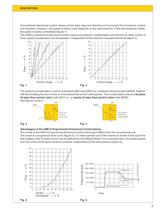
3 DESCRIPTION Conventional directional control valves control start, stop and directions of movement from hydraulic motors and cylinders. However, the speed of these users depends on the load pressure. If this load pressure varies, the speed is hardly controllable (figure 1) The AMCA proportional directional control valves are pressure compensated and achieve an ideal control of force, speed, acceleration and deceleration, independent of the load and increased demands (figure 2) The pressure compensator could be a pressure relief valve (MUV) or a pressure reducing valve (MDM), together with...
Open the catalog to page 3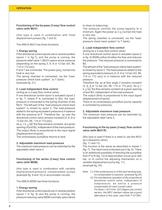
4 Functioning of the by-pass (3-way) flow control valve (with MUV) (this type is used in combination with fixed displacement pumps) (fig. 7 and 8) The AMCA-MUV has three functions: 1. Energy saving If the directional control spools are in neutral position (spool 1 in fig.7), and the pump is running, the pressure relief valve 1 (MUV) opens at low pressure (depending on the spring 3, 6, 8 or 12 bar (43, 86, 114 or 172 psi)). P and T are connected. The power (pxqv) turned into heat is very low. The spring chamber is connected, via the “loadpressure check back system”, to T (tank). (example...
Open the catalog to page 4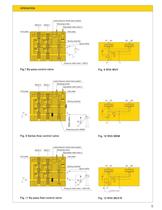
5 OPERATION another circuit Spool 2 B2 End plate A2 MDM orifice Pressure relief valve 1 (MUV) Pressure relief valve 1 (MUV/R) 0 Reducing valve (MDM) 0 M Inlet plate Spring chamber B1 T P A1 spool orifice T1 End plate Load-pressure check back system Adjustable relief valve 2 Spool 1 Damping-screw B2 B1 A2 A1 spool orifice R P M Spring chamber Inlet plate Damping-screw Load-pressure check back system Spool 2 Spool 1 Adjustable relief valve 2 Adjustable relief valve 2 Load-pressure check back system T1 B2 B1 End plate A2 A1 P Spring chamber Inlet plate Spool 2 Spool 1 Damping-screw P A1 B1 P T...
Open the catalog to page 5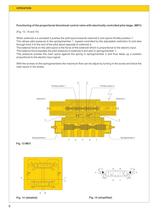
6 OPERATION Functioning of the proportional directional control valve with electrically controlled pilot stage. (MEV) (Fig. 13, 14 and 15) When solenoid a is actuated it pushes the pilot spool towards solenoid b and opens throttle position 1. This allows pilot pressure to the springchamber 1 (speed controlled by the adjustable restriction 5) and also through bore 3 to the end of the pilot spool opposite to solenoid a. The balance force on the pilot spool is the force of the solenoid which is proportional to the electric input. The balance force equates the pilot pressure in solenoid b and...
Open the catalog to page 6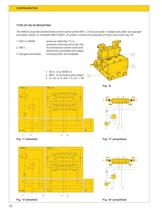
10 A..DM AP P MDM..A A A..EV T2 MEV..A b B a a A B P T b A..UV T P MUV..A A..EV A B AP A P MEV..A b a a T B b 3 1 2 CONFIGURATION TYPE OF VALVE MOUNTING The AMCA proportional directional control valves series MEV...A are sub-plate-, multiple sub-plate- and ganged sub-plate valves. A complete AMCA-MEV..A system consists for example of three main parts (fig 16) 1. MUV or MDM : pressure relief (fig 17) or pressure reducing valve (fig 18)). 2. MEV : 4/3 directional control valve with electrically controlled pilot stage. 3. Ganged sub-plates : including inlet- and endplate Fig. 17 (detailed)...
Open the catalog to page 10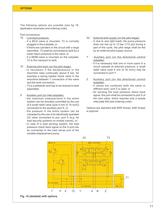
11 OPTIONS The following options are possible (see fig 19, application (example) and ordering code). Port connections: T2 : Low back pressure. - if a MUV-valve is mounted, T2 is normally plugged in the subplate, or - if there are cylinders in the circuit with a large returnflow, T2 shall be connected to tank for a lower return pressure in the valve, or - if a MDM-valve is mounted on the subplate, T2 is the mainport to tank. T3 : External pilot drain (on the pilot stage). - is neccesary if the backpressure in the returnline rises continually above 6 bar, for example a spring loaded check...
Open the catalog to page 11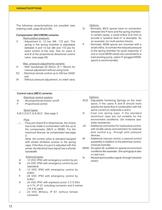
12 VARIANTS/OPTIONS The following variants/options are possible (see ordering code, page 26 and 28). Compensator (MUV/MDM) variants: Recirculation pressure: V : Adjustment 6...12 bar (86...172 psi). The spring in the spring chamber is adjustable between 6 and 12 bar (86 and 172 psi) for exact control of the max. flow on users A and B of the proportional directional control valve. (see page 26) Max. pressure adjustments variants: H : With handwheel (Ø 30mm, Ø 1.18inch) for manual adjustment without using tools E2 : Electrical remote control up to 350 bar (5000 psi) W : Without pressure...
Open the catalog to page 12All Fluitronics GmbH catalogs and technical brochures
-
AMCA Hydraulic power packs
1 Pages
-
CC-KL - Filtercart
2 Pages
-
Radio remote control system
3 Pages
-
HK - Tipping valve
2 Pages
-
MDM-5 - Electrical operation
4 Pages
-
MOV - Hydraulic operation
2 Pages
-
MHV - Manual operation
28 Pages