Catalog excerpts
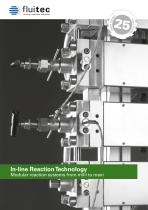
Modular reaction systems from milli to maxi
Open the catalog to page 1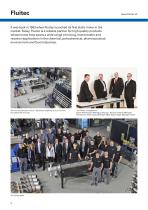
It was back in 1993 when Fluitec launched its first static mixer in the market.Today, Fluitec is a reliable partner for high quality products whose know-how spans a wide range of mixing, heat transfer and reaction applications in the chemical, petrochemical, pharmaceutical, environment and food industries. View of the production shop – apparatus weighing up to 3.5 tons is manufactured in-house The Fluitec management: Daniel Altenburger (Managing Director), Silvano Andreoli (Manager Production), Alain Georg (Manager R&D), Tobias Vögeli (Manager Sales)
Open the catalog to page 2
www.fluitec.ch Contents Fluitec in-line reaction technology Pages 4 - 7 Reactor concepts Pages 8 - 13 ContiplantLAB reactor series Page 14 ContiplantPILOT reactor series Pages 15 - 18 ContiplantMODULE reactor series Page 19 Heating and cooling systems for Contiplant Page 20 Large reactor systems Page 21 Enquiry data sheet Page 22 Other Fluitec products Page 23
Open the catalog to page 3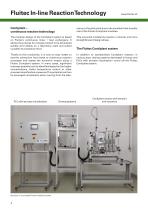
Fluitec In-line Reaction Technology Contiplant – continuous reaction technology ratory to the pilot plant due to the excellent heat transfer rate of the Fluitec Contiplant modules. The modular design of the Contiplant system is based on Fluitec’s continuous mixer / heat exchangers. It allows the process for a target product to be developed quickly and reliably on a laboratory scale and scaled up safely to production level. This universal modularity results in a shorter and more straightforward design phase. Thanks to this modularity, it is now an easy matter to test the conversion from...
Open the catalog to page 4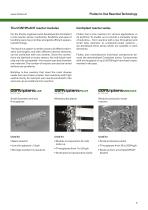
Fluitec In-line ReactionTechnology The CONTIPLANT reactor modules For the Fluitec engineers who developed the Contiplant in-line reactor series, modularity, flexibility and ease of handling were top priorities alongside efficient apparatus technology. The result is a system in which reactors of different diameters and lengths, and with different internal elements, can be combined with one another. Since the connections are identical on every reactor, the individual modules are fully compatible - the reactor type and diameter are irrelevant.The number of reactors can also be varied without...
Open the catalog to page 5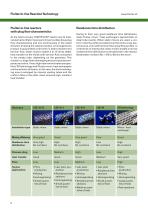
Fluitec In-line ReactionTechnology Fluitec in-line reactors with plug flow characteristics At the heart of every CONTIPLANT reactor are its internal elements. Static mixers and mixer bundles have plug flow characteristics and mix continuously in the radial direction all along the reaction section. A homogeneous product is guaranteed at all times in both turbulent and laminar flow. Static mixers enable 3 to 15 times better heat transfer on the inside with laminar flow compared to the empty tube, depending on the geometry. This results in a large heat-exchanging area and precise temperature...
Open the catalog to page 6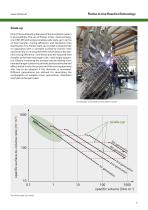
Fluitec In-line Reaction Technology Scale-up One of the outstanding features of the Contiplant system is its scalability. The use of Fluitec mixer / heat exchangers (CSE-XR technology) enables safe scale-up in terms of heat transfer, mixing efficiency and residence time distribution.The Fluitec scale-up concept is based firstly on apparatus with a constant surface-to-volume ratio and secondly on mixing elements which assure the specific mixing efficiency – and hence also the required heat transfer at the heat exchanger tube – with larger apparatus. Simply increasing the surface area by...
Open the catalog to page 7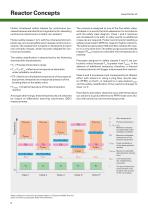
Reactor Concepts Fluitec introduced safety classes for continuous processes because standards and regulations for assessing continuous reactions are virtually non-existent. Fluitec safety classes 1 to 5, with four characteristic temperatures, are one possible way to assess continuous re-actions.The assessment is based on Stoessel's division into criticality classes, which has been adapted for continuous processes. The safety classification is determined by the following characteristic temperatures: • Tp = Processtemperature range • Tm =T0+ATad = Maximum temperature attainable under...
Open the catalog to page 8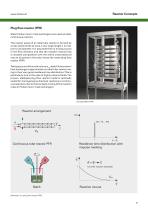
Reactor Concepts Plug flow reactor (PFR) Static Fluitec mixer / heat exchangers are used as ideal, continuous reactors. The reactor space of an ideal tube reactor is formed by a tube which tends to have a very large length L in relation to its diameter. It is assumed that no mixing occurs in the flow direction and that the reaction mixture has a constant composition over the entire cross-sectional area at all points in the tube, hence the name plug flow reactor (PFR). Taking account of the void volume εm, static Fluitec mixer / heat exchangers approximate an ideal tube reactor owing to...
Open the catalog to page 9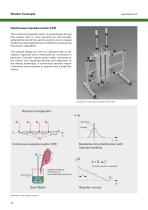
Reactor Concepts Continuous cascade reactor CCR The continuous cascade reactor is a special type of plug flow reactor. One or more reactants are only partially added at the start of the reaction section and are instead divided up and supplied at several different points along that section (cascaded). The cascade design can have an influence both on the reaction in general and on heat build-up / conversion in particular. Cascade reactors place higher demands on the control and regulating devices and especially on the dosing technology. A continuous cascade reactor is therefore more complex...
Open the catalog to page 10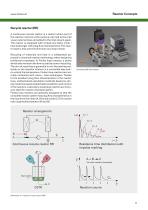
Reactor Concepts Recycle reactor (RR) A continuous recycle reactor is a reactor where part of the reaction mixture at the outlet is returned to the inlet via an external loop and added to the inlet stream again. The reactor is equipped with at least one static mixer / heat exchanger with plug flow characteristics. This reactor type is also commonly known as a loop reactor. Recycling of materials and heat is a widespread approach in chemical reaction technology when designing production processes. In Fluitec loop reactors, a pump which also monitors the flow is used to control recycling. The...
Open the catalog to page 11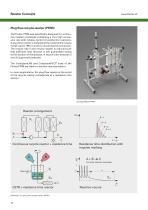
Reactor Concepts Plug flow recycle reactor (PFRR) The Fluitec PFRR was specifically designed for continuous reaction processes combining a very high conversion rate with reliable control of exothermic reactions. A plug flow reactor is installed at the outlet of the recycle (loop) reactor (RR) in order to maximise the conversion. The recycle rate in the recycle reactor is reduced such that sufficient heat removal is still guaranteed owing to the dilution of the product. A recycle ratio between 2 and 10 is generally selected. The ContiplantLAB and ContiplantPILOT sizes of the Fluitec PFRR are...
Open the catalog to page 12All Fluitec mixing + reaction solutions AG catalogs and technical brochures
-
Fluitec heat exchanger 2018
20 Pages
-
Fluitec Mixer 2018
20 Pages
-
Fluitec product overview 2018
16 Pages