Catalog excerpts
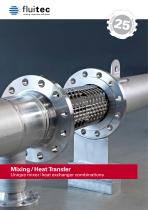
mixing + reaction solutions Mixing / Heat Transfer Unique mixer / heat exchanger combinations
Open the catalog to page 1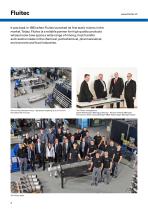
It was back in 1993 when Fluitec launched its first static mixers in the market. Today, Fluitec is a reliable partner for high quality products whose know-how spans a wide range of mixing, heat transfer and reaction tasks in the chemical, petrochemical, pharmaceutical, environment and food industries. View of the production shop – apparatus weighing up to 3.5 tons is manufactured in-house The Fluitec management: Daniel Altenburger (Managing Director), Silvano Andreoli (Manager Production), Alain Georg (Manager R&D), Tobias Vögeli (Manager Sales)
Open the catalog to page 2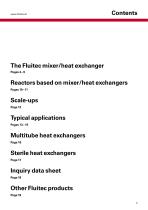
www.fluitec.ch Contents The Fluitec mixer/heat exchanger Pages 4 - 9 Reactors based on mixer/heat exchangers Pages 10 - 11 Scale-ups Page 12 Typical applications Pages 13 - 15 Multitube heat exchangers Page 16 Sterile heat exchangers Page 17 Inquiry data sheet Page 18 Other Fluitec products Page 19
Open the catalog to page 3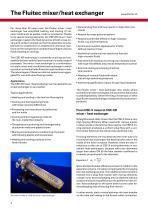
The Fluitec mixer/heat exchanger For more than 20 years now, the Fluitec mixer / heat exchanger has simplified heating and cooling of viscous media such as pastes, melts or emulsions. Thanks to its special mixing elements, the CSE-XR mixer / heat exchanger masters the fluid dynamics of both cross-mixing and surface renewal, so that the apparatus is suitable both for exothermic or endothermic chemical reactions and for temperature conditioning of highly viscous fluids (heating or cooling). The CSE-XR technology is constantly evolving and meanwhile delivers optimal performance in a wide range...
Open the catalog to page 4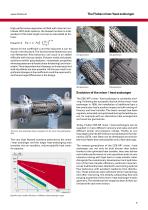
The Fluitec mixer/heat exchanger High performance apparatus is fitted with internal multitubes. With both systems, the Nusselt number is independent of the tube length and can be calculated as follows: Equation 2 Values for the coefficient a and the exponent b can be found in the literature.The fact that both Newtonian and non-Newtonian flow behaviour can occur is an added difficulty with viscous media. Polymer melts and plastic solutions exhibit pseudoplastic, viscoelastic properties whereas pastes are dilatant (shear thickening) and viscoplastic.Time dependencies (rheopexy or thixotropy)...
Open the catalog to page 5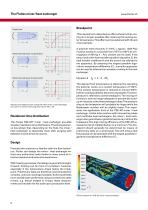
The Fluitec mixer/heat exchanger Empty tube Rohr-ø This internal term describes an effect where further cooling is no longer possible after reducing the cooling water temperature.This effect can be explained with the aid of an example: Mixer/heat exchanger 1st generation Rohr-ø A polymer melt (viscosity @ 215°C = approx. 1500 Pas) must be cooled in a process from 215°C to 190°C at a throughput of 900 kg h-1. Any coolant can be used. If we take a look at the heat transfer equation (equation 3), the heat transfer coefficient k and the area A are referred to the apparatus. By selecting the...
Open the catalog to page 6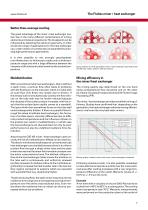
The Fluitec mixer / heat exchanger Better-than-average cooling The great advantage of the mixer / heat exchanger system lies in the many different combinations of mixing elements and tube arrangements.The breakpoint can be influenced by selecting the optimum geometry, in other words the range of applications for the heat exchanger can, under certain circumstances, be expanded by choosing high performance geometries. Maldistribution With conventional tube heat exchangers, that is without a static mixer, a laminar flow often leads to problems with the fluid layer on the tube wall, which in a...
Open the catalog to page 7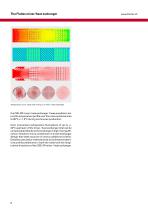
The Fluitec mixer/heat exchanger Temperature curve, shear and mixing in a mixer / heat exchanger the CSE-XR mixer / heat exchanger. It was possible to adjust the temperature profile over the cross-sectional area to 80°C +/- 1.0°C during continuous production. Even momentary temperature fluctuations of up to +/20°C upstream of the mixer / heat exchanger inlet can be compensated thanks to the exchanger’s high mixing efficiency. However, this is conditional on a heat exchanger design that takes account of various additional criteria. Detailed calculation methods exist to facilitate temperature...
Open the catalog to page 8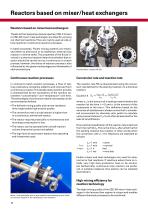
Reactors based on mixer/heat exchangers Reactors based on mixer-heat exchangers Thanks to their special process properties, CSE-X mixers or CSE-XR mixer / heat exchangers are ideal for carrying out chemical reactions. They are mainly used as tube or loop reactors in continuous reaction processes. In batch processes, Fluitec mixing systems are employed either as premixers or as additional, external loop reactors in stirred tanks. The properties of the fluids involved in a chemical reaction determine whether that reaction should be carried out as a continuous or a batch process; however, the...
Open the catalog to page 10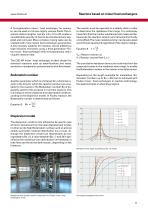
Reactors based on mixer/heat exchangers A first-generation mixer / heat exchanger, for example, can be used to mix two highly viscous fluids.The required relative lengths, namely L/D = 12 to 20, enable a considerable quantity of heat to be simultaneously supplied and removed. More complex mixing tasks can be realised with more recent heat exchanger generations. A low-viscosity catalyst, for instance, can be added to a high-viscosity monomer using a third-generation Flui-tec mixer / heat exchanger while simultaneously removing the reaction heat. The CSE-XR mixer / heat exchanger is often...
Open the catalog to page 11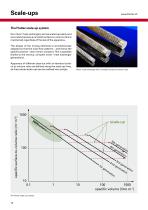
The Fluitec scale-up system Our mixer / heat exchangers can be scaled up easily and accurately because a constant surface-to-volume ratio is maintained regardless of the size of the apparatus. The design of the mixing elements is simultaneously adapted so that the local flow patterns – and hence the specific powers – also remain constant. This is possible thanks to the various, complex mixer / heat exchanger generations. Apparatus of different sizes but with an identical surface-to-volume ratio are defined along the scale-up lines, so that precise scale-ups can be realised very simply....
Open the catalog to page 12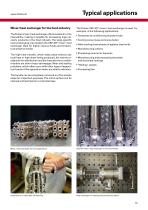
Mixer/heat exchanger for the food industry The Fluitec mixer / heat exchanger offers excellent in-line cleanability, making it suitable for processing high-viscosity products in the food industry. The large specific heat-exchanging area renders the CSE-XR® mixer / heat exchanger ideal for highly viscous fluids and temperature sensitive media. The high heat transfer, which takes place without any local heat or high shear being produced, the narrow residence time distribution and the insensitivity to maldistribution are other major advantages. Wear and sealing problems, which often occur with...
Open the catalog to page 13All Fluitec mixing + reaction solutions AG catalogs and technical brochures
-
Fluitec Mixer 2018
20 Pages
-
Fluitec product overview 2018
16 Pages