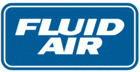

Catalog excerpts
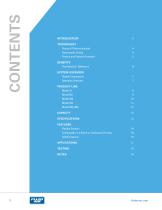
TECHNOLOGY Drying of Pharmaceuticals Electrostatic Drying Particle and Powder Formation BENEFITS The PolarDry® Difference SYSTEM OVERVIEW System Components Operation Overview PRODUCT LINE Model 0.1 Flexible Solution Configurable in a Batch or Continuous Process Safety Features
Open the catalog to page 2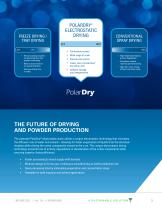
THE FUTURE OF DRYING AND POWDER PRODUCTION The patented PolarDry® electrostatic dryer utilizes a unique electrostatic technology that increases the diffusion rate of water and solvent—allowing for faster evaporation of liquids from the atomized droplets while driving the active components inward to the core. This unique electrostatic drying technology prevents loss of activity, degradation or denaturation of the active components while ensuring superior drying efficiency. • Faster processing to match supply with demand Modular design to fit into your continuous manufacturing or batch...
Open the catalog to page 3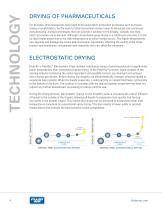
For decades, pharmaceuticals have been dried using batch production processes such as freezedrying or lyophilization. As the world of pharmaceuticals moves towards advanced and continuous manufacturing, drying technologies that can provide a solution to the lengthy, complex and slow batch processes are in demand. Although conventional spray drying is a continuous process, it is not an ideal replacement due to the high temperatures at which drying occurs. The higher temperatures can degrade and damage the active pharmaceutical ingredients, affecting the quality of the dried product and...
Open the catalog to page 4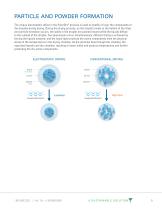
PARTICLE AND POWDER FORMATION The unique electrostatic effect in the PolarDry® process is used to stratify or layer the components of the droplets during drying. During the drying process, as the droplet travels to the bottom of the dryer and particle formation occurs, the solids in the droplet are pushed inward while the liquids diffuse to the outside of the droplet. Two phenomena occur simultaneously: efficient drying is achieved by forcing the liquids outward, and the liquid layer protects the active components from the physical stress of the temperatures in the drying chamber. As the...
Open the catalog to page 5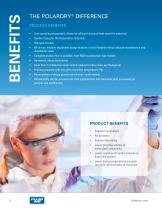
THE POLARDRY® DIFFERENCE PROCESS BENEFITS • Low operating temperature allows for efficient drying of heat-sensitive materials Gentler drying for thermosensitive materials All-in-one, modular equipment design features a small footprint which reduces maintenance and installation costs Complete product line is scalable, from R&D to production-size models Contained, robust processing Inner liner in production scale models makes for easy clean-up/changeover Process products with low glass transition temperature (Tg) Recirculation of drying gases in production-scale models Substantially shorter...
Open the catalog to page 6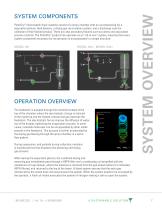
PolarDry® electrostatic dryer systems consist of a spray chamber with an accompanying lid, a separation plenum, feed delivery, a drying gas recirculation system, and a discharge cone for collection of the finished product. There are also secondary fixtures such as valves and associated process controls. The PolarDry® product line operates as an “all-in-one” system, meaning that every system component necessary for its operation is encompassed in a single structure. MODEL 001 MODEL 004 – MODEL 050+ Purge Air Heater Drying gas supply Atomized Gas Supply Heater Feed Drying Chamber Drying...
Open the catalog to page 7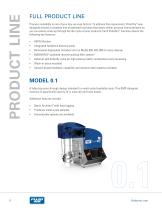
FULL PRODUCT LINE Process scalability is one of your key success factors. To address this requirement, PolarDry® was designed around a complete line of patented machines that share similar process characteristics so you can easily scale-up through the life cycle of your products. Each PolarDry® machine shares the following key features: • HEPA filtration Integrated feedstock delivery pump Removable disposable chamber liner on Model 004, 032, 050 for easy cleanup MAGNAFLO® patented reverse-pulsing filter system* Optional split butterfly valve for high potency batch containment and processing...
Open the catalog to page 8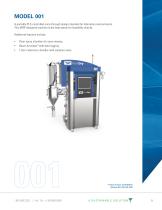
MODEL 001 A portable PLC-controlled once-through design intended for laboratory environments. This GMP-designed machine is the best option for feasibility checks. Additional features include: • Clear spray chamber for easy viewing Batch Architect™ with data logging 1-liter collection chamber with isolation valve
Open the catalog to page 9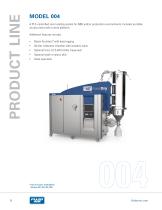
PRODUCT LINE MODEL 004 A PLC-controlled recirculating system for R&D and/or production environments. Includes portable access stairs with a work platform. Additional features include: • Batch Architect™ with data logging 20-liter collection chamber with isolation valve Optional 5-ton (17,5 kW) chiller (required) Optional wash-in-place skid Quiet operation
Open the catalog to page 10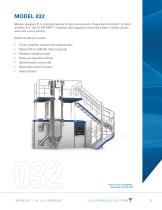
MODEL 032 Modular-designed, PLC-controlled systems for pilot environments. Choose Batch Architect™ or Batch Architect Pro™ with 21 CFR PART 11 compliant data logging to control this system. Includes access stairs with a work platform. Additional features include: • 15-liter collection chamber with isolation valve Optional 30-ton (105 kW) chiller (required) Feedstock handling system Swing-out separation plenum Optional wash-in-place skid Optional pneumatic conveyor Quiet operation
Open the catalog to page 11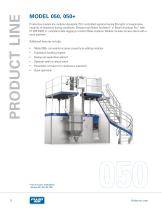
PRODUCT LINE MODEL 050, 050+ Production models are modular-designed, PLC-controlled systems having 50+ kg/hr of evaporative capacity at maximum drying conditions. Choose from Batch Architect™ or Batch Architect Pro™ with 21 CFR PART 11 compliant data logging to control these systems. Models include access stairs with a work platform. Additional features include: • Model 050+ can easily increase capacity by adding modules Feedstock handling system Swing-out separation plenum Optional wash-in-place lance Pneumatic conveyor for continuous operation Quiet operation
Open the catalog to page 12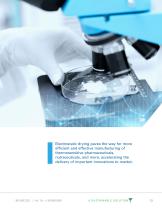
Electrostatic drying paves the way for more efficient and effective manufacturing of thermosensitive pharmaceuticals, nutraceuticals, and more, accelerating the delivery of important innovations to market.
Open the catalog to page 13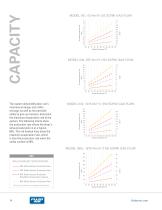
Dry powder production rate MODEL 001, 43 Nm3/h (25 SCFM) GAS FLOW Dry powder production rate MODEL 004, 255 Nm3/h (150 SCFM) GAS FLOW Dry powder production rate The system dehumidification coil’s mechanical design and chiller tonnage, as well as the particles’ ability to give up moisture, determine the maximum evaporation rate of the system. The following charts show the production rate where the dryer’s exhaust saturation is at a typical 60%. The red dashed lines show the maximum evaporation rate, which is also the production rate when the solids content is 50%. 50% Solids Solution...
Open the catalog to page 14All Fluid Air Inc. catalogs and technical brochures
-
SOLID DOSAGE processing
17 Pages
-
GRANUMILL® JR
2 Pages