
Catalog excerpts
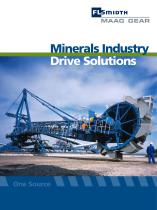
MAAG GEAR Minerals Indust Drive Solutions
Open the catalog to page 1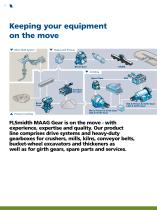
Keeping your equipment on the move Mine Shaft System Heap Leach Process Bevel Gear Grinding Bevel Gear Bevel Gear Primary Crushing WA & Pinion & Girth Gear LGD & Girth Gear WA & Pinion & Girth Gear LGD & Girth Gear FLSmidth MAAG Gear is on the move - with experience, expertise and quality. Our product line comprises drive systems and heavy-duty gearboxes for crushers, mills, kilns, conveyor belts, bucket-wheel excavators and thickeners as well as for girth gears, spare parts and services.
Open the catalog to page 2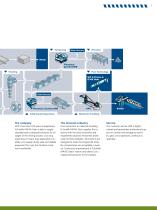
Water Recovery Metal Planetary gearbox/WB Pyro Technology WA & Pinion & Girth Gear Water Recovery Planetary Gearbox/WB Solid/Liquid Separation The company With more than 100 years of experience, FLSmidth MAAG Gear is able to supply standard and customized solutions for all stages of the mining process. Our long experience in heavy duty applications enables us to supply sturdy, safe and reliable equipment for even the harshest conditions worldwide. Materials Handling The minerals industry From extraction to materials handling, FLSmidth MAAG Gear supplies the industry with the most innovative...
Open the catalog to page 3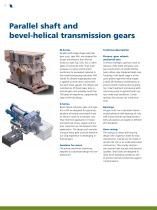
W-Series Parallel-shaft single-stage reduction gear units, type WA, are designed for torque transmission from electric motors to ball, rod, SAG, AG or other types of horizontal mills. Their main purpose is to drive comminution machinery for excavated materials in the mineral processing industries. WB stands for double stage gearbox and is applied to drive other machineries but with lower speeds. The design and manufacture of these heavy duty industrial gear units embody more than 100 years of experience, supported by state-of-the-art design. K-Series Bevel-helical reduction gear units...
Open the catalog to page 4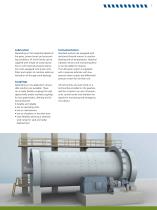
Lubrication Depending on the tangential speeds of the gears, power losses and surrounding conditions, W and K-Series can be supplied with simple oil sump lubrication or with external pressure lubrication units equipped with pump units, filters and coolers to maintain optimum lubrication of the gears and bearings. Couplings Depending on the application, all possible solutions are available. These can include flexible couplings for high speed shafts and/or toothed couplings for low speed shafts, offering the following features: • durable and reliable • low on operating costs • low on...
Open the catalog to page 5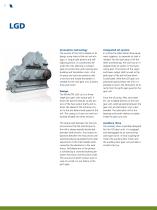
Innovative technology The success of the LGD is based on its design using state-of-the-art technology, i.e. torque split pinions and selfaligning pinions. It is positioned 40° under the mill, allowing a compact type of construction and involving less building and foundation costs. A lot of space and costs are saved as only a very low and simple foundation is needed for the LGD gear unit, auxiliary drive and motor. Design The MAAGTM LGD unit is a three-stage spur gear with torque split. It drives the ball mill directly via the pinions of the two output shafts and reduces the speed of the...
Open the catalog to page 6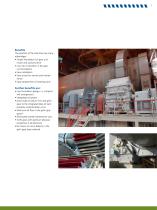
Benefits The position of the side drive has many advantages: • Simple foundation for gear unit, motor and auxiliary drive • Low risk of vibration in the gear unit foundation • Easy installation • Easy access for service and maintenance • Easy replacement of rotating parts Further benefits are: • Low foundation design, i.e. compact mill arrangement • Integrated oil system • Direct lube oil return from the girth gear to the integrated lube oil tank prevents contamination of oil • Minimum oil flow in the girth gear guard • Minimized overall maintenance cost • Girth gear with optimum...
Open the catalog to page 7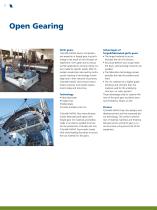
Girth gears FLSmidth MAAG Gear's comprehensive expertise in forged gear ring technology is the result of over 50 years of experience. Girth gears are as various as their applications and are mainly custom-made for specific needs. With its modern production sites and by continuously investing in technology, knowledge and in their network of partners, FLSmidth MAAG Gear ensures that it meets customer and market requirements today and tomorrow. Technology • Fabricated steel • Forged ring • Rolled plate • Ductile (nodular) cast iron FLSmidth MAAG Gear manufactures mainly fabricated girth gears...
Open the catalog to page 8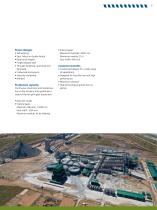
Pinion designs • Self-aligning • Spur, helical or double helical • Bored and integral • Forged alloyed steel • Through-hardened, quenched and tempered • Carburised and ground • Induction-hardened • Nitrided Production capacity Continuous investment and modernization of the machine shop guarantee a state-of-the-art girth gear production. Production range: • External gears Maximum diameter: 11200 mm Face width: 1250 mm Maximum module: 45 by hobbing • Internal gears Maximum Diameter: 6500 mm Maximum module: 25.4 Face width: 400 mm Customer benefits • Customized designs for a wide range of...
Open the catalog to page 9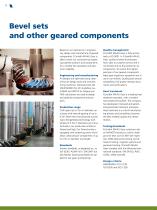
Based on our experience in engineering, design and manufacture of geared components, FLSmidth MAAG Gear is able to assist our customers by supplying tailored solutions and components for a trouble free operation and optimum reliability. Engineering and manufacturing All designs are optimized using state-of-the-art design tools and manufacturing machines. Software tools like SOLIDWORKS for 3D modelling; Au-toFENA and ANSYS for fatigue and FME calculations are used to design and optimize components and systems. Production range Girth gears up to 12m in diameter, annuluses with internal...
Open the catalog to page 10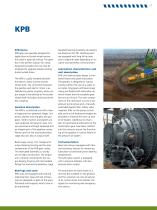
KPB Series KPB gears are specially designed for application on bucket-wheel excavators used in open-pit mining. The gearbox is the perfect solution for newly designed excavators but can also be employed to upgrade already existing bucket-wheel drives. The KPB is usually installed between the electric motor and the bucket wheel shaft. The connection between the gearbox and electric motor is established by elastic coupling, while output torque is transmitted to the bucket wheel shaft via hollow shaft and shrink disc coupling. Gearbox description The KPB is a combined unit with a bevel stage...
Open the catalog to page 11All FLSmidth MAAG® Gears and drives catalogs and technical brochures
-
Open gearing
4 Pages
-
Manufacturing capabilities
6 Pages
-
KPB Transmission Gear Units
2 Pages
-
Redesign of PPU
2 Pages