
Catalog excerpts
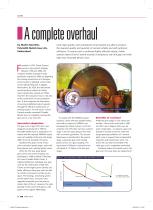
IA complete overhaul by Martin Baechler, Only high-quality, well-maintained cement plants are able to produce FLSmidth MAAG Gear AG, the required quality and quantity of cement reliably and with optimum Switzerland efficiency. To ensure such a continued highly-efficient output, Indian cement maker Orient Cement recently overhauled a raw mill gear unit with help from FLSmidth MAAG Gear. Founded in 1979, Orient Cement pursues a clear growth strategy. Between 1990 and 2009, the company steadily increased its total production capacity to 5Mta by upgrading the existing cement lines at its Devapur cement works in Adilabad, central India, and its split-grinding unit in Jalgaon, Maharashtra. By 2020, the India-based cement producer expects to further raise its production capacity to 15Mta. However, the company's focus is not only on the construction of new production sites. It also recognises the importance of securing established output capacity through the effective maintenance of existing systems. For this reason, Orient Cement recently contacted FLSmidth MAAG Gear to completely overhaul the gear unit of a raw meal mill. Successful adaptation The gear unit, of type CPU-30-2, was designed and produced in 1987 by FLSmidth MAAG Gear in Switzerland. As motors with the required 3800kW output were not available at the time, the design differs from the standard CPU series. Standard CPU gears consist of two series-connected planet stages, each with three planets and a rotating planet carrier. When the first two-stage planet gear unit for the cement industry was developed in 1966 by MAAG Zahnrader AG (now FLSmidth MAAG Gear), it replaced traditional, multistage spur gear units for the central drive of ball mills. Thanks to their higher power density and better efficiency, these gear units are able to transfer more power and take up less space. The bearings, monitoring system and oil system have, of course, been upgraded constantly over the years to remain state of the art. However, the basic principle of the current CPU gears is still based on the original 1966 design. To comply with the 3800kW output required, a drive with two parallel motors, each with an output of 1900kW, was developed for Orient Cement. As its first reduction, this CPU does not have a planet stage. It has two input pinions that mesh with a common gearwheel. The accumulated power is transferred to the second stage, a planetary gear with rotating planet carrier, via a gear coupling. The input speed of 992rpm is reduced to the mill speed of 14.76rpm in the two gear stages. Benefits of overhaul While the gear design is very robust and durable - the first two units built in 1967 are still in use in Belgium after over 46 years of operation - to operate a gear unit beyond its normal service life under the tough operating conditions of a cement plant, more is required than just periodical inspection and maintenance work. The service life can only be extended if the entire gear unit is completely overhauled. Overhauls reduce the overall wear in the gear unit. The wear parts are replaced and
Open the catalog to page 1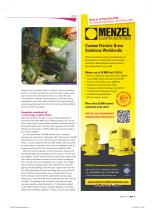
em 2014! Meet us at PetroC 14 ssia · 27-29 April, 20 St. Petersburg, Ru Custom Electric Drive Solutions Worldwide Whenever project-related manufacturing and fast delivery is needed, there is one obvious alternative: Menzel Elektromotoren GmbH – the swift partner by your side! Ultrasonic inspection on planet axle the gear unit is serviced so that it is ready for the next operating period. If overhauls are planned in advance, they can be carried out in periods of low demand and also ensure that the gear unit continues to operate without problems. They help reduce maintenance costs, extend the...
Open the catalog to page 2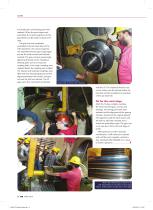
and small parts and wearing parts were replaced. When the gear stages were assembled, the internal alignment of the gearwheels and the tooth contacts were reset. The gear unit was completely assembled in the last three days of the mill’s downtime. The service engineers first assembled the two gear stages again and set the tooth contact and backlash correctly. The gear unit was provisionally aligned and braced on the foundation. Wearing parts such as O-rings and coupling bolts in the output coupling were replaced before the coupling was installed. The cleaned and inspected couplings were...
Open the catalog to page 3All FLSmidth MAAG Gear AG catalogs and technical brochures
-
Open gearing
4 Pages
-
Manufacturing capabilities
6 Pages
-
KPB Transmission Gear Units
2 Pages
-
Redesign of PPU
2 Pages