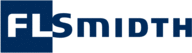

Catalog excerpts

Equipment and Systems for Corn Wet Milling
Open the catalog to page 1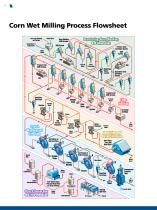
Corn Wet Milling Process Flowsheet
Open the catalog to page 2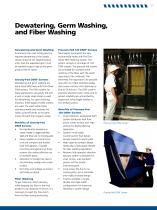
Dewatering and Germ Washing Economical corn wet milling practice requires dewatering of the supply stream ahead of the degerminating mills. Also the separated germ must be washed to get a high purity germ product free of starch. Gravity-Fed DSM® Screens Dewatering and germ washing are done more effectively with Dorr-Oliver DSM screens. The DSM screens for these applications are gravity fed over a weir. A single stage screen is used for dewatering. For germ washing, however, three stages of DSM screens are used. The wash water flows countercurrently and removes the starch quite efficiently...
Open the catalog to page 3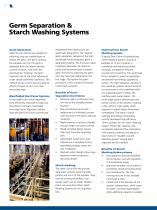
Germ Separation After the corn kernels are steeped for softening, they are cracked open to release the germ. The germ contains the valuable corn oil. The germ is separated from the heavier density mixture of starch, hulls and fiber essentially by "floating" the germ segments free of the other substances under closely controlled conditions. This method serves to eliminate any adverse effects of traces of corn oil in later processing steps. Manifolded DorrClone Systems To accomplish this critical separation most efficiently, most plants today use Dorr-Oliver's compact manifolded two-stage...
Open the catalog to page 4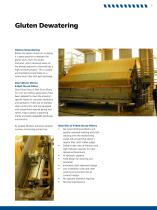
Gluten Dewatering Before the gluten moves on to drying it is good practice to dewater the gluten slurry from the gluten thickener, which obviously saves on the energy required to thermally dry a high moisture product. This is usually accomplished economically on a rotary drum filter with belt discharge. Dorr-Oliver Eimco E-Belt Drum Filter Dorr-Oliver Eimco E-Belt Drum Filters for corn wet milling applications have been adapted to meet the industry's specific needs for corrosion resistance and sanitation. Filters are of stainless steel construction and are equipped with streamlined internal...
Open the catalog to page 5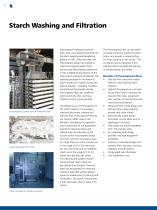
Pneumapress® automatic pressure filters were successfully introduced into the starch washing and dewatering process in 1997. Since that time, the Pneumapress design has evolved to meet the changing needs of the industry and Pneumapress equipment is now installed by the majority of the major starch producers worldwide. The starches processed on the Pneuma-press include corn, wheat, potato and tapioca starches - including modified, industrial and food grade varieties. Pneumapress filters are installed in starch plants the USA, Germany, Thailand, Korea, France and Italy. The design focus of...
Open the catalog to page 6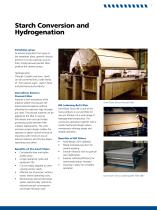
Polishing syrup To remove impurities from syrup in the sweetener plant, general industry practice is to use a precoat vacuum filter, simply because precoat filters produce the clearest syrups. Hydrogenation: Through Catalytic reactions, starch can be converted into a wide family of "low calories sugar" used in food and pharmaceutical products. Dorr-Oliver Eimco's Precoat Filter features a slow and precise knife advance system that assures the lowest precoat expense without affecting the machine's high throughput rates. The precoat material can be applied to the filter in varying thicknesses...
Open the catalog to page 7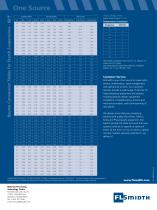
One Source Baume Conversion Tables for Starch Suspensions - 60°F *% D.S. = Be deg x 1.7770 Specific Gravity of Starch 1.5 - 1.6 Temperature Corrections Temperature These tables are based on the work of J.E. Cleland, E.E. Fauser and W.R. Fetzer See Industrial and Engineering Chemistry, Analytical Edition, Vol. 15, pp 193-200, 1943 Customer Service FLSmidth is your One Source for spare parts, service, maintenance, asset management, and operational services. Our Customer Services provide a wide range of services for food processing equipment and systems including process design,...
Open the catalog to page 8All FLSmidth Dorr-Oliver Eimco catalogs and technical brochures
-
Decanter™ centrifuges
4 Pages
-
FLS Discover Mining
19 Pages
-
Caricamat
7 Pages
-
Pneumapress
8 Pages
-
Tailings dewatering press
8 Pages
-
EIMCO AFP IV Filter Press
4 Pages
-
ABON Low Speed Sizers
8 Pages
-
TST jaw crusher
8 Pages
-
Gyratory Crushers
8 Pages
-
Cement plant upgrades
12 Pages
-
HIGHLIGHTS 2016
32 Pages
-
Flotation technology
16 Pages
-
Screen Media
24 Pages
-
KREBS® millMAXTM Pumps
8 Pages
-
Precious Metals Capabilities
7 Pages
-
QCXRoboLab Minerals
24 Pages
-
Mineral Processing Solutions
16 Pages
-
Top service gyratory crusher
8 Pages
-
MHC Twin shaft breaker
4 Pages
-
EV crusher retrofit
4 Pages
-
EV hammer impact crusher
8 Pages
-
Crushing Systems
20 Pages
-
Shriver Filter Press
8 Pages
-
Horizontal Belt filter
4 Pages
-
Dry Process Sampling
9 Pages
-
QCX/RoboLab - Minerals
13 Pages
-
QCX/RoboLab - QCX/Autoprep
2 Pages
-
Centaurus
5 Pages
-
Automation of Train Loader
3 Pages
-
Automation Solutions
11 Pages
-
ECS/ControlCenter
15 Pages
-
Milling of metal samples
5 Pages
-
BulkExpert
7 Pages
-
HyLogging
5 Pages
-
FT Grinding Mills
4 Pages
-
Grinding Mills
8 Pages
-
Screens Brochure
7 Pages
-
Portable Conveyor
1 Pages
-
Morenci
1 Pages
-
Los Filos
1 Pages
-
Zaldivar
1 Pages
-
Radomiro Tomic
1 Pages
-
El Tesoro
1 Pages
-
El Abra
1 Pages
-
Preheater calciner systems
8 Pages
-
Gas Suspension Absorber
9 Pages
-
World Cement Article
3 Pages
-
FabriClean™
34 Pages
-
Hydrocyclones
4 Pages
-
Feeder Breakers
8 Pages
-
HDP Beltpress Filters
8 Pages
-
Raptor XL1100 Brochure
8 Pages
-
Raptor XL300/XL400 Brochure
12 Pages