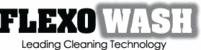
Catalog excerpts
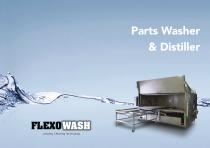
Parts Washer & Distiller Leading Cleaning Technology
Open the catalog to page 1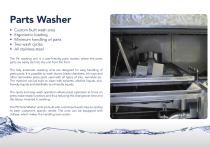
Parts Washer • • • • • Custom built wash area Ergonomic loading Minimum handling of parts Two wash cycles All stainless steel The PK washing unit is a user-friendly parts washer, where the press parts are easily slid into the unit from the front. The fully automatic washing units are designed for easy handling of press parts. It is possible to wash doctor blade chambers, ink trays and other removable press parts used with all types of inks, varnishes etc. The machine can be built to clean with solvents, alkaline liquids, ecofriendly liquids and distillable eco-friendly liquids. The quick...
Open the catalog to page 2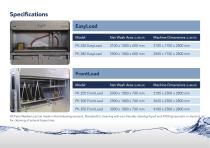
EasyLoad Model Net Wash Area (LxWxH) Machine Dimensions (LxWxH) Model Net Wash Area (LxWxH) Machine Dimensions (LxWxH) All Parts Washers can be made in the following versions: Standard for cleaning with eco-friendly cleaning liquid and ATEX (pneumatic or electric) t/ for cleaning of solvent based inks.
Open the catalog to page 3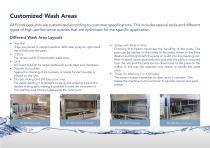
Customized Wash Areas All FrontLoad units are customized according to customer specifications. This includes special racks and different types of high performance nozzles that are optimised for the specific application. Different Wash Area Layouts • Tray Rail: Trays are placed in upright position. With side spray for optimised liquid flow over the parts. • 2-Story: For various parts. Gives double wash area. • Grid: All round solution for larger parts such as ink trays and chambers. • Nozzles for buckets: Special for cleaning of ink buckets. A nozzle for each bucket is placed on the grid. •...
Open the catalog to page 4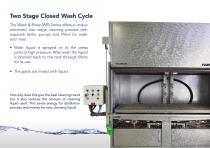
Two Stage Closed Wash Cycle The Wash & Rinse (WR) Series offers a unique automatic two stage cleaning process with separate tanks, pumps and filters for wash and rinse: • Wash liquid is sprayed on to the press parts at high pressure. After wash the liquid is drained back to the tank through filters for re-use. • The parts are rinsed with liquid Not only does this give the best cleaning result but it also reduces the amount of cleaning liquid used. This saves energy for distillation process and money for new cleaning liquid
Open the catalog to page 5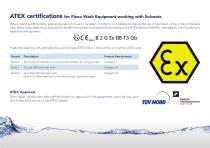
When cleaning with solvent, special precautions have to be taken in order to completely neutralize the risk of explosion or fire in the immediate area. Flexo Wash takes these precautions by delivering washing equipment according to the ATEX directive 94/9/EC intended for use in potentially explosive atmospheres. Inside the washing unit and tanks the unit will have ATEX zone 0. Around the unit will be ATEX zone 1. Hazard Description Product Requirement Zone 0 Explosive atmosphere is continuously present for long periods. Category I Zone 1 10 and 100 hours per year. Category...
Open the catalog to page 6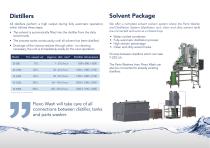
Solvent Package All distillers perform a high output during fully automatic operation, which follows three steps: We offer a complete solvent reclaim system where the Parts Washer and Distillation System (distillation unit, clean and dirty solvent tank) are connected and work as a closed loop. • The solvent is automatically filled into the distiller from the dirty solvent tank. • The process works continuously until all solvent has been distilled. • Drainage of the viscous residue through valve - no cleaning necessary, the unit is immediately ready for the next operation. Model Approx....
Open the catalog to page 7
Leading Cleaning Technology
Open the catalog to page 8All Flexo Wash catalogs and technical brochures
-
MULTI CYLINDER CLEANER
8 Pages
-
WIDE WEB CLEANING EQUIPMENT
20 Pages
-
ANILOX & CYLINDER CLEANING
12 Pages
-
NARROW WEB CLEANING EQUIPMENT
20 Pages
-
SOM 1000
1 Pages
-
SOM 200
1 Pages
-
SOM 100
1 Pages
-
Cleaning liquid
2 Pages
-
SL Sleeve Washers
2 Pages
-
CW Cylinder Washer
8 Pages
-
SPLIT-O-MAT® SOM
1 Pages
-
Anilox Roll Cleaners
2 Pages
-
Plate Wash
2 Pages