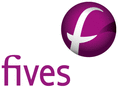
Group: Fives Group

Catalog excerpts
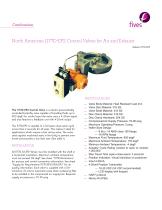
North American 1177D-EP2 Control Valves for Air and Exhaust Bulletin 1177D-EP2 The 1177D-EP2 Control Valve is a electro-pneumatically controlled butterfly valve capable of handling fluids up to 800 degF. For control input the valve uses a 4-20mA signal, and also features a feedback unit with 4-20mA output . The 1177D-EP2 is capable of a full open-close-open cycle in less than 2 seconds for all sizes. This makes it ideal for applications which require a fast acting valve. The valve seats against machined seats in the body to prevent overtravel and provides a low leak rate. (See table 1). INSTALLATION All 1177D-XX-EP2 Valves must be installed with the shaft in a horizontal orientation. Maximum ambient temperature must not exceed 176 degF. See sheet “1177D Dimensions” for process and control connection information. See sheet “Supply Air Requirements 1177D-EP2/1008-EP2” for air quality information. Each valve is supplied with a 1/4" miniature .01 micron automatic pulse drain coalescing filter to be installed in the compressed air supply line. Required supply air pressure is 70-90 psig. Valve Body Material: Heat Resistant Cast Iron — Valve Disc Material: 316 SS — Valve Shaft Material: 316 SS — — Disc Clamp Material: 316 SS Disc Clamp Hardware: 304 SS — Compressed Air Supply Pressure: 70-90 psig — Maximum Operating Pressure: 2 psig — Wafer Style Design — — -6 thru -14 ANSI class 150 flange — -16 RPM flange Maximum Fluid Temperature: 800 degF — Maximum Ambient Temperature: 176 degF — — Minimum Ambient Temperature: -4 degF Actuator Cycle Rating (closed to open to closed): — 1,000,000 Max Travel Time (open-close-open): 2 seconds — Position Indication: Visual Indication on positioner — — Input 4-20mA — 4-20mA Position Transmitter — 10-30 VDC (24 VD
Open the catalog to page 1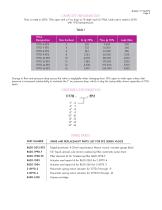
CAPACITY INFORMATION Flow is rated in SCFH, 70% open with a 1"wc drop at 70 degF. and 14.7 PSIA. Leak rate is rated in SCFH with 1 PSI backpressure. Change in flow and pressure drop across the valve is negligible when changing from 70% open to wide open unless inlet pressure is increased substantially to maintain the 1" wc pressure drop, which is why the sizing table shows capacities at 70% open. ORDERING INFORMATION SPARE PARTS SPARE AND REPLACEMENT PARTS LIST FOR EP2 SERIES VALVES Digital positioner, 4-20mA input/output, Namur mount, includes gauge block 1/4" liquid, ^rosol, sub-micron...
Open the catalog to page 2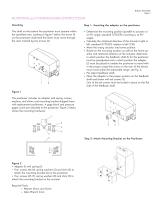
MOUNTING and COMMISSIONING INSTRUCTIONS Mounting Step 1: Mounting the adapter on the positioner The shaft on the bottom the positioner must operate within the specified area. Looking at figure 1 below, the arrow (1) on the positioner shaft (and the lever) must move through the area marked by the arrows (2). • Determine the mounting position (parallel to actuator or at 90° angle, standard 1177D-EP2 mounting is at 90° angle). • Calculate the rotational direction of the actuator (right or left, standard 1177D-EP2 rotation is left CCW). • Move the rotary actuator into home position. • Based on...
Open the catalog to page 3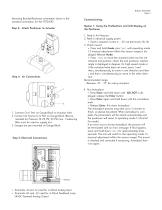
Mounting Bracket/Positioner orientation shown is the standard orientation for the 1177D-EP2 Step 3: Attach Positioner to Actuator Option 1: Using the Pushbuttons and LCD Display on the Positioner 1. Connect Out 1 Port on Gauge Block to Actuator Inlet 2. Connect Air Source to In Port on Gauge Block (Recommended Air Pressure 70-90 PSI, 90 PSI max. Coalescing filter must be used on supply air) 3. Gauges are pre-mounted on Gauge Block Step 5: Electrical Connections • Terminals +11 and -12 used for 4-20mA Analog Input • Terminals +31 and -32 used for 4-20mA Feedback Loop 24VDC Powered Analog...
Open the catalog to page 4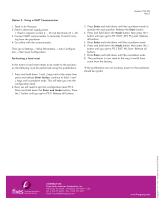
Option 2: Using a HART Communicator 1. Feed in Air Pressure 2. Feed in electrical supply power • Feed in setpoint current 4 ... 20 mA (terminals +11 / -12) 3. Connect HART communicator to terminals 11 and 12 coming from the positioner 4. Go online with the communicator. Then go to Settings→ Valve Parameters→ Auto Configuration→ Start Auto Configuration Performing a hard reset In the event a hard reset needs to be made to the positioner, the following must be performed using the pushbuttons: 3. Press Enter and hold down until the countdown ends to activate the save position. Release the...
Open the catalog to page 5All FIVES PILLARD catalogs and technical brochures
-
Pillard Windcross™
2 Pages
-
Pillard Nocostop Eco
2 Pages
-
Pillard Nocostop Premium™
2 Pages
-
Pillard Opastop® GP4000T-EX
2 Pages
-
Pillard Opastop® GP4000H-EX
2 Pages
-
Pillard Dieselight™
2 Pages
-
Pillard Opastop® GP4000H
2 Pages
-
OPAGAZ
2 Pages
-
Pillard Opastop® GP4000H-C
2 Pages
-
Pillard DarkscanFlex™
2 Pages
-
Pillard Oxycheck™
2 Pages
-
Pillard Packlight™
2 Pages
-
Pillard flame scanners
4 Pages
-
Pillard Smokecheck™
2 Pages
-
Pillard Powerpack™
2 Pages
-
Pillard Windcheck™
2 Pages
-
Pillard Opastop® GP4000H
2 Pages
-
Pillard TK DRAIN
2 Pages
-
Pillard Opastop® GP4000T-EX
2 Pages
-
Pillard TK Drain
2 Pages
-
INDUCTFLAM® L
2 Pages
-
OPASTOP GP4000H-EX
2 Pages
-
OPAGAZ
2 Pages
-
Pillard RotaFlam®
2 Pages
-
Pillard PrecaFlam™
2 Pages
-
Pillard NovaFlam®
2 Pages
-
Pillard Powerpack™
2 Pages
-
Blower Silencers
2 Pages
-
Series 2300 Turbo Blowers
7 Pages
-
SAF – Adjustable Flow Valve
2 Pages
-
Limiting Orifi ce Gas Valves
3 Pages
-
Double Shutoff Valve
2 Pages
-
Oil Shutoff Valves
6 Pages
-
Pneumatic Cycle Valve
2 Pages
-
Air Cycling Valve
2 Pages
-
Wafer Butterfly Valves
4 Pages
-
1008A-C / 1010A-C-1
3 Pages
-
Adjustable Port Valves
4 Pages
-
Butterfl y Valves
4 Pages
-
ITAS Ductflame
4 Pages
-
ITAS Speedflame
4 Pages
-
ITAS Dryflame
4 Pages
-
ITAS Intensityflame
4 Pages
-
Adjustable Port Valves
2 Pages
-
Pillard Opastop® GP4000H
2 Pages
-
Waste heat recovery
48 Pages
-
Pillard Opastop® GP3050ST
2 Pages
-
Pillard SmokecheckTM
2 Pages
-
Pillard Windcheck™
2 Pages
-
Pillard NocostopTM
2 Pages
Archived catalogs
-
Pillard Packlight
2 Pages
-
Pillard flame scanners
4 Pages