Catalog excerpts
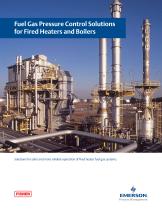
Fuel Gas Pressure Control Solutions for Fired Heaters and Boilers Solutions for safer and more reliable operation of fired heater fuel gas systems. Process Management
Open the catalog to page 1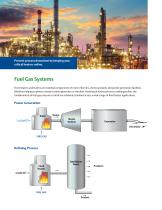
Prevent process downtime by keeping your critical heaters online. Fuel Gas Systems Fired heaters and boilers are essential components of most refineries, chemical plants and power generation facilities. Whether helping to power a steam turbine generator or the direct heating of hydrocarbons to make gasoline, the fundamentals of fuel gas pressure control are relatively standard across a wide range of fired heater applications. Power Generation Steam Steam Turbine Generator Electricity refining Process Fired Heater Distillation Tower
Open the catalog to page 2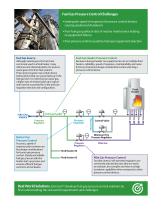
Fuel Gas Pressure Control Challenges • Inadequate speed of response of pressure control devices causing unplanned shutdowns • Poor fuel gas quality or lack of routine maintenance leading to equipment failures • Poor pressure control caused by improper equipment selection Although natural gas is the fuel most commonly used in a fired heater, many refineries and chemical plants mix process waste gases into their fuel systems. These process gases may contain heavy hydrocarbons that can cause build-up in the fuel gas lines. For sites that use waste gas, a higher rate of residue build-up is...
Open the catalog to page 3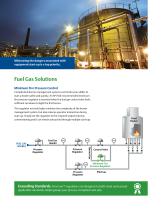
minimizing the dangers associated with equipment start-up is a top priority. Fuel Gas Solutions minimum Fire Pressure Control Complicated burner management systems can hinder your ability to start a heater safely and quickly. An API 556-recommended minimum fire pressure regulator is essential when the fuel gas control valve lacks sufficient turndown to light the first burner. This regulator not only helps minimize the complexity of the burner management system, but also reduces operator interaction during start-up. Simply set the regulator to the required setpoint during commissioning and...
Open the catalog to page 4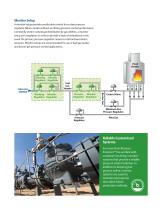
monitor Setup A monitor setup provides predictable control for certain pressure regulator failure modes without sacrificing pressure control performance. Commonly used in natural gas distribution by gas utilities, a monitor setup uses regulators in series to provide a layer of redundancy in the event the primary pressure regulator ceases to control downstream pressure. Monitor setups are recommended for use in fuel gas header and burner gas pressure control applications. Fired Heater Working Monitor Regulator Regulator Working Monitor Regulator Regulator Pressure Monitor Regulator Regulator...
Open the catalog to page 5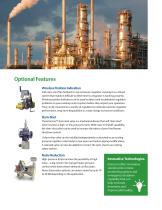
optional Features wireless Position Indication End users are often hesitant to use a pressure regulator, viewing it as a closed system that makes it difficult to determine if a regulator is working properly. Wireless position indicators can be used to detect and troubleshoot regulator problems on your existing control system before they impact your operation. They can be mounted on a variety of regulators to indicate real-time regulator performance, long-term degradation or a step change in process conditions. Slam-Shut The Emerson™ slam-shut valve is a mechanical device that will “slam...
Open the catalog to page 6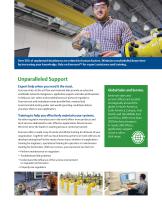
over 50% of unplanned shutdowns are related to human factors. minimize unscheduled down time by increasing your knowledge. rely on Emerson™ for expert assistance and training. Unparalleled Support Expert help when you need it the most. Emerson state-of-the art flow and materials labs provide an extensive worldwide network of engineers, application experts and sales professionals to help you size, select and troubleshoot your pressure regulators. Emerson test and evaluation teams provide flow, material and environmental testing under real-world operating conditions before you place them in...
Open the catalog to page 7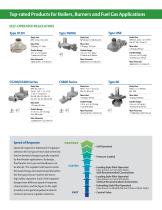
Top-rated Products for Boilers, Burners and Fuel Gas applications SElF-oPEraTEd rEGUlaTorS Type 912n Type y600a Body Size NPS 1/4 or 1/4 x 3/8 max Inlet 250 psig / 17.2 bar outlet range 3 in. w.c. to 5 psig / 7 mbar to 0.35 bar outlet range 4 in. w.c. to 7 psig / 10 mbar to 0.48 bar max Inlet 125 psig / 8.6 bar outlet range 4 in. w.c. to 2.2 psig / 10 mbar to 0.15 bar max Flowrate 4800 SCFH / 129 Nm3/h Type 66 Body Size NPS 1-1/4, 1-1/2 or 2 / DN 32, 40 or 50 outlet range 3.5 in. w.c. to 10 psig / 9 to 690 mbar outlet range 4 in. w.c. to 5 psig / 10 mbar to 0.35 bar outlet range 3.5 in....
Open the catalog to page 8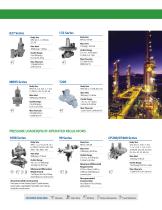
outlet range 2 in. w.c. to 60 psig / 5 mbar to 4.1 bar outlet range 5 to 500 psig / 0.34 to 34.5 bar Body Size NPS 3/4 or 1 / DN 20 or 25 max Inlet 200 psig / 13.8 bar outlet range 1 in. w.c. to 7 psig / 2 mbar to 0.48 bar outlet range 2 to 400 psig / 0.14 to 27.6 bar PrESSUrE loadEd/PIloT-oPEraTEd rEGUlaTorS 1098 Series outlet range 2 in. w.c. to 100 psig / 5 mbar to 6.9 bar outlet range 4 in. w.c. to 300 psig / 10 mbar to 20.7 bar minimum differential requirement minimum differential requirement outlet range 1 to 20 psig / 0.07 to 1.4 bar max Flowrate 17,600 SCFH / 472 Nm3/h recommended...
Open the catalog to page 9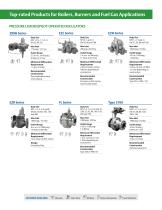
Top-rated Products for Boilers, Burners and Fuel Gas applications PrESSUrE loadEd/PIloT-oPEraTEd rEGUlaTorS Ezl Series outlet range 3.5 in. w.c. to 60 psig / 9 mbar to 4.1 bar outlet range 7 in. w.c. to 300 psig / 17 mbar to 20.7 bar outlet range 14.5 to 1160 psig / 1 to 80 bar minimum differential requirement minimum differential requirement minimum differential requirement recommended Construction recommended Construction Fast open or fast closing Type 61 pilot option recommended Construction Dual registration using 3/4 in. piping outlet range 6 in. w.c. to 1000 psig / 15 mbar to 68.9 bar...
Open the catalog to page 10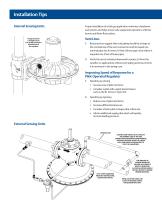
Installation Tips Internal Sensing Units Piping should be a straight run for 8 to 10 pipe diameters downstream of the regulator Proper installation of a fuel gas application minimizes shutdowns and restarts and helps ensure safe equipment operation, with less burner and flame fluctuations. Best practices suggest that vent piping should be as large as the nominal size of the vent connection and increased one nominal pipe size for every 10 feet of linear pipe. (One elbow is equivalent to 3 feet of linear pipe.) 2. Verify the vent is oriented downward to protect it from the weather on...
Open the catalog to page 11All FISHER REGULATORS catalogs and technical brochures
-
™ Control Valves and Instruments
16 Pages
-
Run with higher performing,
16 Pages
-
R Series
2 Pages
-
LP-Gas Technologies
118 Pages
-
Industrial Regulators
2 Pages
-
Type 92B Pressure Reducing Valve
16 Pages
-
Type 630R Relief Valve
8 Pages
-
Fisher™ 585C Piston Actuators
16 Pages
-
Type 630 Regulator
16 Pages
-
Fisher™ YD and YS Control Valves
24 Pages
-
easy-e Cryogenic Valves
12 Pages
-
Large ET and ED Valves
20 Pages
-
1305 Series Regulators
4 Pages
-
H200 Series Relief Valves
4 Pages
-
Air Application Map
1 Pages
-
DeltaV Controller Firewall
11 Pages
-
CSI 6500 Overview
12 Pages
-
The Criticality of Cooling
5 Pages
-
Ovation Security Center
4 Pages
-
DeltaV Smart Switches
28 Pages
-
Smartprocess™ Heater
5 Pages
-
FPSO Industry Solution
2 Pages
-
LP-31
96 Pages
-
CS 200 series
2 Pages
-
Regulators Mini Catalog
24 Pages
-
1301F, 1301G
12 Pages
-
MR95 and MR98
2 Pages
-
Fisher® D and DA Valves
12 Pages
-
Fisher® EZ easy-e Control Valve
40 Pages
-
Fisher® YD and YS Control Valves
24 Pages
-
Fisher® HPNS Control Valve
36 Pages
-
Fisher® HP Series Control Valves
28 Pages
-
Fisher® CAV4 Control Valve
28 Pages
-
Fisher® 377 Trip Valve
20 Pages
-
EZR Pressure Reducing Regulator
36 Pages
-
630 Regulator
16 Pages
-
627F Pressure Reducing Regulator
12 Pages
-
ACE97 Pad-Depad Valve
16 Pages
-
310A Pressure Reducing Regulator
16 Pages
-
S200 series
32 Pages
-
R622 series
8 Pages
-
Type HSR Pressure Regulators
20 Pages
-
cs200 series
40 Pages
-
CS400 Series
60 Pages
-
167D Series Switching Valves
8 Pages
Archived catalogs
-
Vapor Pressures of LP-Gas
1 Pages
-
Pipe and Tubing Sizing
1 Pages
-
Average Properties of LP-Gas
1 Pages
-
Pressure Equivalents
1 Pages