Catalog excerpts
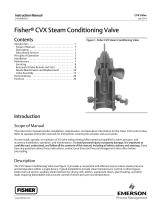
Instruction Manual Fisherr CVX Steam Conditioning Valve Contents Figure 1. Fisher CVX Steam Conditioning Valve Introduction . . . . . . . . . . . . . . . . . . . . . . . . . . . . . . . . . 1 Scope of Manual . . . . . . . . . . . . . . . . . . . . . . . . . . . . . 1 Description . . . . . . . . . . . . . . . . . . . . . . . . . . . . . . . . . 1 Educational Services . . . . . . . . . . . . . . . . . . . . . . . . . 3 Principle of Operation . . . . . . . . . . . . . . . . . . . . . . . . . 3 Installation . . . . . . . . . . . . . . . . . . . . . . . . . . . . . . . . . . 4 Maintenance . . . . . . . . . . . . . . . . . . . . . . . . . . . . . . . . . 7 Servicing . . . . . . . . . . . . . . . . . . . . . . . . . . . . . . . . . . . 8 Removal of Valve Bonnet and Trim . . . . . . . . . . . . . 8 Nozzle Maintenance and Replacement . . . . . . . . . 10 Valve Assembly . . . . . . . . . . . . . . . . . . . . . . . . . . . . 13 Parts Ordering . . . . . . . . . . . . . . . . . . . . . . . . . . . . . . . 20 Parts List . . . . . . . . . . . . . . . . . . . . . . . . . . . . . . . . . . . 20 Introduction Scope of Manual This instruction manual includes installation, maintenance, and operation information for the Fisher CVX control valve. Refer to separate instruction manuals for instructions covering the actuator and accessories. Do not install, operate, or maintain a CVX valve without being fully trained and qualified in valve, actuator, and accessory installation, operation, and maintenance. To avoid personal injury or property damage, it is important to carefully read, understand, and follow all the contents of this manual, including all safety cautions and warnings. If you have any questions about these instructions, contact your Emerson Process Management sales office before proceeding. Description The CVX Steam Conditioning Valve (see figure 1) provides a convenient and efficient way to reduce steam pressure and temperature within a single device. Typical installations include steam backpressure control, turbine bypass, boiler start-up service, auxiliary steam letdown for drying rolls, kettles, equipment drives, plant heating, and other loads requiring dependable and accurate control of steam pressure and temperature.
Open the catalog to page 1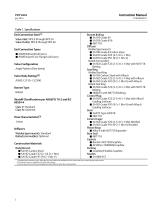
Instruction Manual Table 1. Specifications End Connection Sizes(1) Valve Inlet: NPS 4 through NPS 24 Valve Outlet: NPS 8 through NPS 36 End Connection Types J ASME Buttweld (all sizes) J ASME Raised Face Flanges (all sizes) Valve Configuration Angle Pattern (flow down) Valve Body Ratings(2) ASME: CL150 - CL2500 Bonnet Type Bolted Shutoff Classifications per ANSI/FCI 70-2 and IEC 60534-4 Class V: Standard Class IV: Optional Flow Characteristics(3) Linear Diffusers Welded (permanent): Standard Bolted (removable): Optional Construction Materials Body/Bonnet J SA105 Carbon Steel J SA182 Grade...
Open the catalog to page 2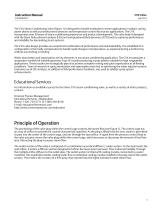
The CVX Steam Conditioning Valve (figure 1) is designed to handle moderate to severe applications in today's cycling power plants as well as provide precise pressure and temperature control for process applications. The CVX incorporates over 30 years of steam conditioning experience and product development. The valve body is designed with the latest finite element analysis (FEA) and computational fluid dynamics (CFD) tools to optimize performance and reliability for demanding steam systems. The CVX valve design provides an exceptional combination of performance and maintainability. The...
Open the catalog to page 3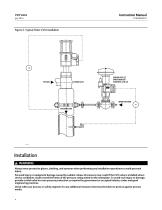
Instruction Manual Figure 2. Typical Fisher CVX Installation FISHER 667-EZ SPRAYWATER CONTROL VALVE Installation WARNING Always wear protective gloves, clothing, and eyewear when performing any installation operations to avoid personal injury. Personal injury or equipment damage caused by sudden release of pressure may result if the CVX valve is installed where service conditions could exceed the limits of the pressure rating noted on the nameplate. To avoid such injury or damage, provide a relief valve for over pressure protection as required by government or accepted industry codes and...
Open the catalog to page 4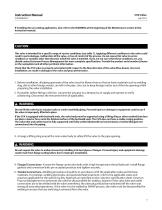
If installing into an existing application, also refer to the WARNING at the beginning of the Maintenance section in this instruction manual. CAUTION This valve is intended for a specific range of service conditions (see table 1). Applying different conditions to the valve could result in parts damage, malfunction of the valve, or loss of control of the process. Do not expose this valve to service conditions or variables other than those for which this valve is intended. If you are not sure what these conditions are, you should contact Emerson Process Management for more complete...
Open the catalog to page 5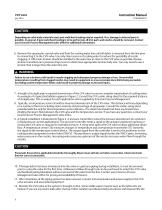
CAUTION Depending on valve body materials used, post weld heat treating may be required. If so, damage to internal parts is possible. In general, if post weld heat treating is to be performed, all trim parts and nozzles should be removed. Contact your Emerson Process Management sales office for additional information. 6. Remove the spraywater control valve and flush the cooling water line until all debris is removed from the line prior to connecting it to the CVX valve. Use only clean sources of cooling water to reduce the possibility of nozzle clogging. A 100 mesh strainer should be...
Open the catalog to page 6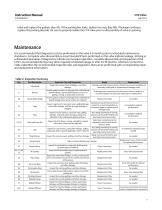
Instruction Manual valve and replace the gaskets (key 43). If the packing box leaks, tighten hex nuts (key 68). If leakage continues, replace the packing (key 64). Be sure to properly isolate the CVX valve prior to disassembly of valve or packing. Maintenance It is recommended that diagnostic tests be performed on the valve 3-6 months prior to scheduled maintenance shutdowns. Complete valve disassembly is recommended if tests performed on the valve indicate leakage, sticking or substandard operation. If diagnostics indicate normal valve operation, complete disassembly and inspection of the...
Open the catalog to page 7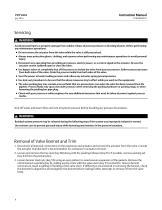
Instruction Manual Servicing WARNING Avoid personal injury or property damage from sudden release of process pressure or bursting of parts. Before performing any maintenance operations: D Do not remove the actuator from the valve while the valve is still pressurized. D Always wear protective gloves, clothing, and eyewear when performing any maintenance operations to avoid personal injury. D Disconnect any operating lines providing air pressure, electric power, or a control signal to the actuator. Be sure the actuator cannot suddenly open or close the valve. D Use bypass valves or completely...
Open the catalog to page 8All FISHER REGULATORS catalogs and technical brochures
-
™ Control Valves and Instruments
16 Pages
-
Run with higher performing,
16 Pages
-
R Series
2 Pages
-
LP-Gas Technologies
118 Pages
-
Industrial Regulators
2 Pages
-
Type 92B Pressure Reducing Valve
16 Pages
-
Type 630R Relief Valve
8 Pages
-
Fisher™ 585C Piston Actuators
16 Pages
-
Type 630 Regulator
16 Pages
-
Fisher™ YD and YS Control Valves
24 Pages
-
easy-e Cryogenic Valves
12 Pages
-
Large ET and ED Valves
20 Pages
-
1305 Series Regulators
4 Pages
-
H200 Series Relief Valves
4 Pages
-
Air Application Map
1 Pages
-
DeltaV Controller Firewall
11 Pages
-
CSI 6500 Overview
12 Pages
-
The Criticality of Cooling
5 Pages
-
Ovation Security Center
4 Pages
-
DeltaV Smart Switches
28 Pages
-
Smartprocess™ Heater
5 Pages
-
FPSO Industry Solution
2 Pages
-
LP-31
96 Pages
-
CS 200 series
2 Pages
-
Regulators Mini Catalog
24 Pages
-
1301F, 1301G
12 Pages
-
MR95 and MR98
2 Pages
-
Fisher® D and DA Valves
12 Pages
-
Fisher® EZ easy-e Control Valve
40 Pages
-
Fisher® YD and YS Control Valves
24 Pages
-
Fisher® HPNS Control Valve
36 Pages
-
Fisher® HP Series Control Valves
28 Pages
-
Fisher® CAV4 Control Valve
28 Pages
-
Fisher® 377 Trip Valve
20 Pages
-
EZR Pressure Reducing Regulator
36 Pages
-
630 Regulator
16 Pages
-
627F Pressure Reducing Regulator
12 Pages
-
ACE97 Pad-Depad Valve
16 Pages
-
310A Pressure Reducing Regulator
16 Pages
-
S200 series
32 Pages
-
R622 series
8 Pages
-
Type HSR Pressure Regulators
20 Pages
-
cs200 series
40 Pages
-
CS400 Series
60 Pages
-
167D Series Switching Valves
8 Pages
Archived catalogs
-
Vapor Pressures of LP-Gas
1 Pages
-
Pipe and Tubing Sizing
1 Pages
-
Average Properties of LP-Gas
1 Pages
-
Pressure Equivalents
1 Pages