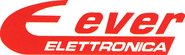

Catalog excerpts
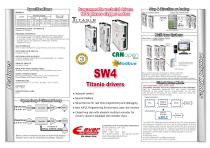
MODELS Code Specifications Power supply Power Logic Programmable vectorial drivers for 2 phases stepper motors Step & Direction or Analog VECTOR - STEPPER - DRIVES COMMUNICATION INTERFACE Modbus or CANbus Multi Axes Systems ENCODER INTERFACE - incremental encoder not isolated input 5V Differential (RS422) or 5V Single-Ended (TTL/CMOS) (SW4D2070 and SW4A3070) or absolute encoder input 5V BISS-C or SSI (SW4A3070x261-02 only) - encoder output not isolated 5V Differential (RS422) (SW4A3070 only) Slave Mode - c0380 CANopen DS402 - c0490 Modbus ANALOG INPUTS 2 analog inputs EMULATED STEP RESOLUTION Stepless Control Technology (65536 positions per turn) SAFETY PROTECTIONS Over/UnderVoltage, OverCurrent, OverTemperature, Phase/Phase and Phase/Ground Short TEMPERATURE operating from 5°C to 40°C, storage -25°C to 55°C Titanio drivers HUMIDITY 5% ÷ 85% PROTECTION CLASS IP20 ● Serial Service for real time programming and debugging ����� ����������� ������������������������� ���������� ����������� ����������� ������������������������� Better control compared to both an open loop stepper solution and a servo-controlled brushless solution Drive control through commands by Master Controller. Suitable for multi axes systems (up to 127 drives). Built in powerfull Motion Module functionality assures perfect synchronization among axes and reduces Master Controller workload. Stand Alone Mode FIELDBUS DRIVES WITH AUTONOMOUS FUNCTIONING that, by integrating advanced PLC and motion controller functions in one single device, programmable by the user with the IDE for Windows PC and e3PLC, allows to reduce the traditional machine control solution. ������ ������ ● New e3PLC Programming Environment, easy and intuitive ● Closed loop also with absolute multiturn encoder for driver’s versions equipped with encoder input Traditional Solution Open loop / Closed Loop Closed Loop �������� Control Up to 25 drives can be connected through the GWC Gateway ELETTRONICA PER AUTOMAZIONE INDUSTRIALE Via del Commercio, 2/4 - 9/11 Loc. S. Grato - Z.I. 26900 - LODI (LO) - Italy Tel. +39 0371 412318 - Fax +39 0371 412367 email infoever@everelettronica.it www.everelettronica.it The e3PLC IDE allows the user to access all the I/O control functions and resources, provided by the drive, and to locally program its Motion Control Module, which can also be synchronized with other drives and events of the controlled process. Thanks to the advanced functionalities of the Power Motion Module, an integrated Real-time Process Module, applications can be easily created for special applications such as: ● Labelling ● Electronic cams ● Control Sequences of cable processing ● Many o
Open the catalog to page 1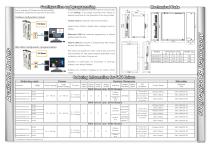
Mechanical Data Autonomous management of the firmware for the execution Ever co. proprietary PC Software Tools for easy and quick development, configuration and supervision of each system. of the homing, of the target movement with relative or absolute quota and for the generation of the ramp profiles Fieldbus configuration (slave) Torque mode for operation with torque limitation � � Speed control thanks to digital inputs, analogue inputs or profiles inside the drive Electric shaft with encoder or analogue input with variable tracking ratio (Electric Gear) Available Models Fast inputs and...
Open the catalog to page 2All Ever Elettronica catalogs and technical brochures
-
SW3A Titanio drivers
2 Pages
-
SW1 Programmable Drives
3 Pages
-
High Efficiency stepper motors
28 Pages
-
Integrated servomotor SM2A
2 Pages
-
Application catalogue
28 Pages
-
Stepper drivers catalogue
64 Pages
-
SM1A integrated systems
2 Pages
Archived catalogs
-
ATOMIC Environment Introduction
20 Pages