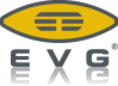

Catalog excerpts
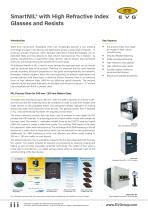
SmartNIL® with High Refractive Index Glasses and Resists Introduction Wafer-level nanoimprint lithography (NIL) has increasingly become a key enabling technology to support new devices and applications across a wide range of markets. In particular complex structures, which typically need direct writing technologies, can be replicated easily and thus allowing to high-volume manufacturing. This is realized by leading manufacturers of augmented reality devices, optical sensors and biomedical chips who are already utilizing the benefits of this technology. ■■ Full process chain from single ■■ ■■ ■■ ■■ ■■ An additional benefit of NIL is that for many devices the replicated layer can be directly used as functional layer in the product. Therefore it is important that the used materials provide according functional properties but also good nanoimprintability and reliability. Nowadays, material suppliers follow this trend especially for photonic applications and provide polymers with broad span of refractive indices. However, there is an enhanced focus on high refractive index (HRI) for e.g. diffractive optical elements. The required materials, resists and glass substrates, are available with refractive indices n > 1.7 and are fully compatible with the NIL process chain. die master to high volume manufacturing Step and Repeat Mastering Wafer-level Manufacturing High refractive index glasses High refractive index resists Excellent pattern fidelity for nanoimprinted devices ■■ Robust and scalable processing NIL Process Chain for 200 mm / 300 mm Wafers Sizes To enable mass manufacturing on 200 mm / 300 mm wafers, typically not only the waferlevel NIL but also the mastering has to be considered in order to scale from masters with single devices to fully populated wafers and subsequent reliable replication of working stamps and wafer level production of the devices. This general process flow is depicted in Fig. 1 and schematically illustrates the required process steps. The shown reference process flow has been used to evaluate in more detail the NIL process with HRI materials. As a starting point an e-beam written master with a single die has been used. This master is replicated multiple times by the EVG770 step and repeat (S&R) NIL system to create a wafer-level master. The resulting S&R master is the basis for subsequent wafer-level manufacturing. The advantage of the S&R mastering is that all devices are a replica from a single device which can be optimized for best performance. Additionally, the S&R mastering is more cost effective and allows easier scaling to 200 mm / 300 mm wafers or even beyond. The actual production line is completely supported by the fully integrated EVG Hercules NIL system. The system includes all required pre-processing as cleaning, coating and baking as well as EVGs proprietary SmartNIL technology. The system is than used in a first step to manufacture a so-called working stamp which is eventually used for the nanoimprinting of the final devices. EVG®7200 Automated Smart NIL® UV-NIL System HERCULES® NIL Fully-integrated Smart NIL® UV-NIL System Fig. 1: Schematic overview of the full process chain for high volume manufacturing with SmartNIL on 8” and 12” wafers. 06.05.2019 - SmartNIL® with High Refractive Index Materials EV Group - DI Erich Thallner Strasse 1 - 4782 St. Florian am Inn - Austria - Con
Open the catalog to page 1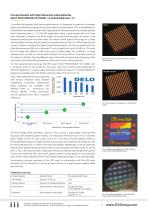
Process Results with High Refractive Index Materials DELO PHOTOBOND VE 533861 on Schott RealView™ 1.7 To achieve the required final device performance it is important to preserve the pattern quality and fidelity throughout the process chain as shown above. This is established for conventional nanoimprint resists which typically don't have particular functional properties and a refractive index n ~ 1.5. For HRI applications these newer resists with n>1.7 have been evaluated. Therefore, the same master and manufacturing steps as shown in the reference process flow has been used. The master...
Open the catalog to page 2All EV Group catalogs and technical brochures
-
EVG®770 NT
1 Pages
-
EVG Product Range Brochure
12 Pages
-
EV Group Product Range
12 Pages