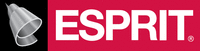

Catalog excerpts
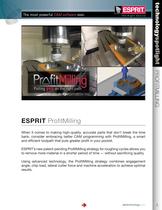
technologyspotlight ProfitMilling ESPRIT ProfitMilling When it comes to making high-quality, accurate parts that don’t break the time bank, consider embracing better CAM programming with ProfitMilling, a smart and efficient toolpath that puts greater profit in your pocket. ESPRIT’s new patent-pending ProfitMilling strategy for roughing cycles allows you to remove more material in a shorter period of time — without sacrificing quality. Using advanced technology, the ProfitMilling strategy combines engagement angle, chip load, lateral cutter force and machine acceleration to achieve optimal results. dptechnology.com 1
Open the catalog to page 1
technologyspotlight 21/2-Axis Advantages 75% cycle-time reduction* 500% increase in tool life* Decreased programming time Reduced energy consumption Significant productivity improvements, even with light and medium-duty machine tools Available for 2 ½ ,3, 4, and 5-axis roughing cycles 3-Axis ProfitMilling • • • • • • 75% C T ycle ime Reduction 4-Axis How ProfitMilling Works ProfitMilling is a high-speed roughing cycle that allows you to take a significantly deeper cut of the tool and increase the cutting feed. Rather than controlling just one parameter, ProfitMilling monitors several vital...
Open the catalog to page 2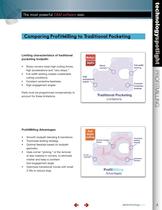
The most powerful CAM software ever. Comparing ProfitMilling to Traditional Pocketing Limiting characteristics of traditional pocketing tool path: • Sharp corners mean high cutting forces, high accelerations and "zero stops." • Full-width slotting creates undesirable cutting conditions. • Constant centerline feedrates • High engagement angles Parts must be programmed conservatively to account for these limitations. Traditional Pocketing ProfitMilling Advantages • Smooth toolpath blending & transitions • Trochoidal slotting strategy • Optimal feedrate based on toolpath • Uses corner...
Open the catalog to page 3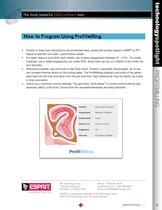
DP Technology Corp. 1150 Avenida Acaso Camarillo, CA 93012 USA ProfitMilling • Double or triple tool-manufacture recommended feed, speed and surface speed in MMPT or IPT. Adjust to specific tool wear / performance needs. • For steel, titanium and other hard metals, use a radial engagement between 27 – 37%. For softer materials, use a radial engagement just under 90%. Most parts can be cut a depth of two times the tool diameter. • Whenever possible, use tools with a high flute count. Coolant is generally discouraged, as its use can increase thermal shock on the cutting edge. The...
Open the catalog to page 4Archived catalogs
-
ESPRIT Report Generator
2 Pages
-
ESPRIT General Overview Eng.
4 Pages