

Catalog excerpts
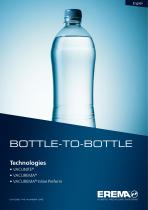
BOTTLE-TO-BOTTLE Technologies • VACUNITE® • VACUREMA® • VACUREMA® Inline Preform
Open the catalog to page 1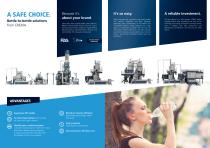
A SAFE CHOICE. Bottle-to-bottle solutions from EREMA. Because it's about your brand. Clean melt, clean recycled pellets, clean preforms. EREMA bottle-to-bottle systems stand for uncompromising food contact compliance, highly efficient decontamination, high-performance filtration and safe handling. For top-quality end products. Stable processes and consistently high quality pellets and preforms: Production and plant managers appreciate these characteristics of VACUNITE® and VACUREMA® systems. Simple operation and a high degree of automation included. The fact that the end product remains...
Open the catalog to page 2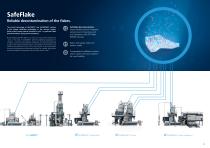
SafeFlake Reliable decontamination of the flakes. The central advantage of VACUNITE® and VACUREMA® systems is the unique SafeFlake technology in the vacuum reactor, which unites several central functions in one - in particular flake decontamination, drying and IV treatment. By pre-treating the PET flakes in a vacuum at the correct temperature - and, in the case of VACUNITE®, with the additional application of nitrogen - moisture and migratory substances are removed effectively as part of the process before extrusion. This prevents any hydrolytic and oxidative decomposition of the melt in the...
Open the catalog to page 3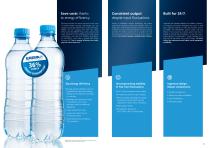
Save costs thanks to energy efficiency. Thanks to SafeFlake's vacuum technology, the system achieves the required IV values and maintains them at a stable level - even though the input material has mixtures of different IV values and wall thickness as well as varying humidity. The intrinsic viscosity (IV) is so stable here that the values even lie within the tolerance limits for virgin PET material. For constant quality and high product safety. Supported with valuable feedback from EREMA customers, our engineers and product developers have come up with some ingenious solutions to make the...
Open the catalog to page 4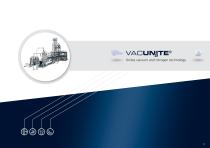
Unites vacuum and nitrogen technology
Open the catalog to page 5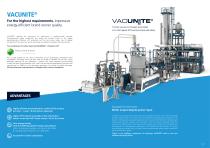
VACUNITE® For the highest requirements. Impressive energy-efficient brand owner quality. • Unites vacuum & nitrogen technology • For the highest rPET purity & enhanced safety VACUNITE® redefines the benchmark for performance in bottle-to-bottle recycling: Uncompromising safety, productivity and quality are ensured thanks to the highest decontamination efficiency, rPET granulates with the best colour values, top IV stability, compactness of the system as well as low energy consumption throughout the entire process. Your combination for safety: Improved VACUREMA® + Polymetrix SSP This is made...
Open the catalog to page 6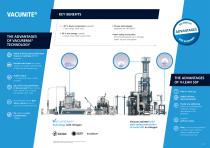
KEY BENEFITS • ~ 40 % fewer components required* -> less energy, lower costs THE ADVANTAGES OF VACUREMA® TECHNOLOGY • 36 % less energy needed* -> lower costs, better environment • Proven technologies developed for VACUNITE® • More safety and quality All thermal processes are in nitrogen and/or vacuum atmosphere Highly efficient decontamination thanks to SafeFlake BEFORE extrusion Flexible with input even when moisture, IV values, bulk densities & flake wall thicknesses vary ... Stable output ... IV value and colour remain constant Up to 40 % less dwell time in the extruder*) less thermal...
Open the catalog to page 7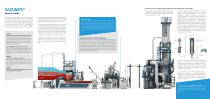
Patented vacuum assisted nitrogen solid state polycondensation (V-LeaN SSP) The food-grade, spherical and crystalline pellets obtained in this way are fed to the nitrogen SSP in a hot state. This patented system was developed exclusively for EREMA by Polymetrix and has the following special features: The key components of the system include a vacuum reactor with integrated nitrogen flushing which is connected directly to a single-screw extruder. Thanks to the ingenious function of the mixers in the vacuum reactor they feature three ultraefficient function zones which interact perfectly with...
Open the catalog to page 8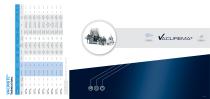
Total energy consumption** (0.35 kWh/kg) Nitrogen consumption * At an input flake IV of 0.76 dl/g ** including expected power consumption of necessary water chillers at the customer´s plant Subject to latest technical updates. System throughput Technical data. VACUNITE® Extruder Residual moisture Food Grade < 50ppm FDA NOL / efsa < 50ppm FDA NOL / efsa < 50ppm FDA NOL / efsa < 50ppm FDA NOL / efsa < 50ppm FDA NOL / efsa < 50ppm FDA NOL / efsa < 50ppm FDA NOL / efsa < 50ppm FDA NOL / efsa < 50ppm FDA NOL / efsa Advantages < 10 redundant filter < 10 redundant filter < 10 redundant filter < 10...
Open the catalog to page 9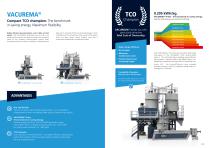
Compact TCO champion. The benchmark in saving energy. Maximum flexibility. 0.295 kWh/kg. VACUREMA® Prime - the benchmark in saving energy. Specific total energy consumption kWh/kg comparative value 5 VACUREMA stands out with particularly attractive Total Cost of Ownership. VACUREMA® Prime Highly efficient decontamination, safe, stable and fast results. With VACUREMA® technology, you can rely on an efficient and extremely cost effective system that compactly unites all the necessary bottle-to-bottle process steps. Uncompromising food contact compliance, impressively low total cost of...
Open the catalog to page 10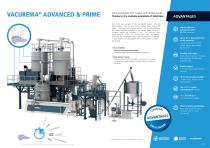
VACUREMA ADVANCED & PRIME ® Short processing time = quick and reliable results. Thanks to the multiple potentials of SafeFlake. One of the core strengths of the VACUREMA® system is that the entire process - from the flake to the finished, food contact rPET pellet - is particularly fast, efficient and safe. This is made possible by the unique SafeFlake technology in the vacuum reactor, because it combines several key functions in one - in particular flake decontamination, drying and IV treatment. With VACUREMA® Advanced and VACUREMA® Prime, the full potential is unleashed in two reactors....
Open the catalog to page 11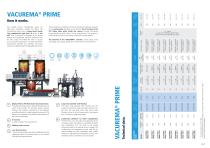
spherical or cylindrical inline crystallised * At an input flake IV of 0.76 dl/g ** including expected power consumption of necessary water chillers at the customer´s plant Subject to latest technical updates. < 50ppm FDA NOL / efsa -4000 VACUREMA® PRIME 2628 T spherical or cylindrical inline crystallised < 50ppm FDA NOL / efsa -3300 VACUREMA® PRIME 2625 T spherical or cylindrical inline crystallised < 50ppm FDA NOL / efsa -2600 VACUREMA® PRIME 2321 T spherical or cylindrical inline crystallised < 50ppm FDA NOL / efsa -2200 VACUREMA® PRIME 2021 T spherical or cylindrical inline crystallised...
Open the catalog to page 12All EREMA Engineering Recycling Maschinen und Anlagen catalogs and technical brochures
-
INTAREMA® ZeroWastePro
6 Pages
-
QualityOn 2021
5 Pages
-
INTAREMA® TVEplus®
5 Pages
-
INTAREMA® T/TE
5 Pages
-
INTAREMA® RegrindPro®
4 Pages
-
INTAREMA® Imagefolder
7 Pages
-
SW Direct Flow
2 Pages
-
SW RTF
6 Pages
-
ReFresher
12 Pages
-
re360
7 Pages
-
QualityOn
6 Pages
-
LASERFILTER
5 Pages
-
RegrindPro®
4 Pages
-
INTAREMA® K
5 Pages
-
INTAREMA®
7 Pages
-
HG D
4 Pages
-
HG AIR
3 Pages
-
ecoSAVE
6 Pages
-
DD / Air Flush Module
3 Pages
-
COREMA®
5 Pages
-
ASP
4 Pages
-
INTAREMA TVEplus
5 Pages
Archived catalogs
-
Application Post Consumer
7 Pages
-
Spare Parts Online
2 Pages
-
Service
6 Pages
-
INTAREMA
5 Pages
-
Vacurema Bottle to bottle
7 Pages
-
VACUREMA PELLETISING
7 Pages
-
Vacurema inline
9 Pages