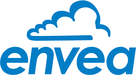
Catalog excerpts
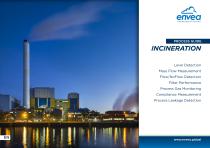
PROCESS GUIDE INCINERATION Level Detection Mass Flow Measurement Flow/NoFlow Detection Filter Performance Process Gas Monitoring Compliance Measurement Process Leakage Detection
Open the catalog to page 1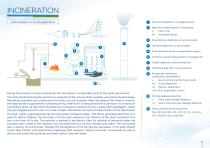
INCINERATION Click numbers to access application Point level detection in charging chute Mass flow measurement of absorbent Coke, lime Ash level detection at filter outlets Flow detection at ash transportation system Flow/NoFlow detection at cyclone outlet Continuous level measurement in storage silos Single baghouse outlet monitoring Dust filtration Predictive bag filter row monitoring Process gas monitoring: Combustion optimization Gas monitoring at the boiler outlet Acids abatement Mercury abatement NOx abatement control During the process of waste incineration the atmospheric...
Open the catalog to page 2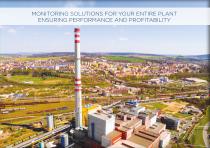
MONITORING SOLUTIONS FOR YOUR ENTIRE PLANT ENSURING PERFORMANCE AND PROFITABILITY
Open the catalog to page 3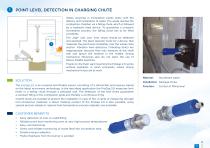
POINT LEVEL DETECTION IN CHARGING CHUTE Waste recycling in incineration plants starts with the delivery and incineration of waste. The waste reaches the combustion chamber via a falling chute, which is followed by a hydraulic feed device. To guarantee a constant incineration process, the falling chute has to be filled constantly. The „high“ and „low“ limit values should be detected and alarmed. The plant operator looks for a device, that measures the point level completely over the whole cross section. Vibration level detectors (Vibrating forks) are inappropriate, because they only measure...
Open the catalog to page 4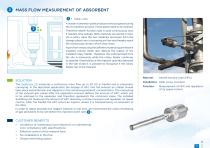
MASS FLOW MEASUREMENT OF ABSORBENT 2 Coke, Lime A waste incineration plant produces exhaust gases during the incineration process. These gases need to be cleaned. Therefore hearth furnace coke is used continuously and, if needed, lime hydrate. Both materials are stored in silos. Via a rotary valve the two materials are blown from the storage places into a conveying air flow and thereby reach the exhaust gas stream which they clean. Apart from measuring the different material quantities the installed volume meter also detects the output of the installed rotary feeder. Therefore the material...
Open the catalog to page 5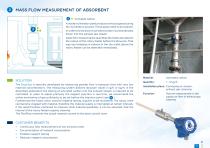
MASS FLOW MEASUREMENT OF ABSORBENT 2 Activated carbon A waste incineration plant produces exhaust gases during the incineration process. These gases need to be cleaned. In order to bind dioxins activated carbon is pneumatically blown into the exhaust gas stream. Apart from measuring the quantities the meter also detects the output of the rotary feeder before the blow line. That way any bridging of material in the silo outlet above the rotary feeder can be detected immediately. SOLUTION The PicoFlow is specially developed for measuring powder flow in transport lines with very low material...
Open the catalog to page 6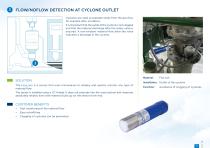
FLOW/NOFLOW DETECTION AT CYCLONE OUTLET Cyclones are used to separate solids from the gas flow, for example after scrubbers. It is important that the outlet of the cyclone is not clogged and that the material discharge after the rotary valve is ensured. A non-existent material flow after the valve indicates a blockage in the cyclone. SOLUTION The FlowJam is a sensor that uses microwaves to reliably and quickly monitor any type of material flow. The sensor is installed using a 1.5“ thread. It does not protrude into the cross-section and measures absolutely reliably even with material build...
Open the catalog to page 7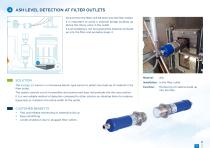
ASH LEVEL DETECTION AT FILTER OUTLETS All dust from the filters will fall down into the filter outlets. It is important to avoid a material bridge building up above the rotary valve in the outlet. If such bridging is not recognized the material will build up into the filter and probably plugs it. SOLUTION The ProGap 2.0 sensor is a microwave barrier type sensor to detect any build up of material in the filter outlet. The system consists out of a transmitter and receiver and does not protrude into the cross section. Installation: In the filter outlet Function: Monitoring of material build up...
Open the catalog to page 8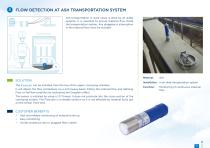
FLOW DETECTION AT ASH TRANSPORTATION SYSTEM Ash transportation in most cases is done by air slides systems. It is essential to ensure material flow inside the transportation system. Any plugging or interruption in the material flow must be avoided. SOLUTION The FlowJam can be installed from the top of the upper conveying chamber. It will detect the flow contactless via a microwave beam hitting the material flow and defining Flow or NoFlow condition by evaluating the Dopplers effect. Installation: In air slide transportation system Function: Monitoring of continuous material flow The sensor...
Open the catalog to page 9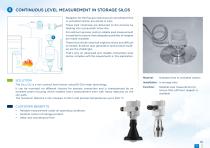
CONTINUOUS LEVEL MEASUREMENT IN STORAGE SILOS Reagents for the flue gas cleaning such as hydrated lime or activated carbon are stored in silos. These bulk chemicals are delivered to the process by feeding into a pneumatic blow line. For optimum process control, reliable level measurement is essential to ensure that adequate quantities of reagent are made available. These kind of bulk chemical might be sticky and difficult to handle. Extreme dust generation and product buildup are the challenges. That’s why an advanced and reliable contactless level sensor complies with the requirements in...
Open the catalog to page 10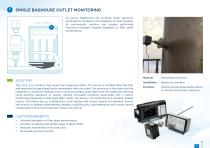
SINGLE BAGHOUSE OUTLET MONITORING To ensure baghouses are working under optimum performance conditions, the installation of dust monitors to continuously monitor and display particulate emissions provides valuable feedback on filter plant performance. SOLUTION The VIEW 370 monitors dust levels from baghouse filters. The sensor is installed after the filter and measures the particulate levels immediately after the outlet. The proximity to the outlet and the capability to measure readings once a second provides pulse data from the baghouse cleaning cycle allowing operators to quickly identify...
Open the catalog to page 11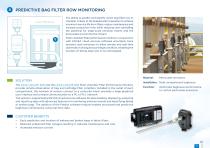
PREDICTIVE BAG FILTER ROW MONITORING The ability to predict and identify which bag filter row or chamber is likely to fail enables plant operators to achieve maximum service life from filters, reduce maintenance and increase production time while reducing and controlling the potential for large-scale emission events and the associated environmental impact. Multi-chamber filter performance monitors in conjunction with ENVEA cloud services software accurately track dynamic dust emissions to allow remote and real-time observation of bag and cartridge condition, enabling the location of failing...
Open the catalog to page 12All ENVEA catalogs and technical brochures
-
LAS 5000XD
2 Pages
-
Amesa-M Mercury Sampler (Hg)
2 Pages
-
PCME STACK 980
4 Pages
-
PCME STACK 602
4 Pages
-
PCME STACK 710 dust monitor
4 Pages
-
PCME STACK 990
4 Pages
-
MGC101- Multi-Gas Calibrator
2 Pages
-
E-Series - AF22E SO2 monitor
2 Pages
-
SM-4 CEMS Mercury Monitor
2 Pages