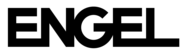
Catalog excerpts
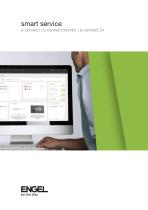
smart service
Open the catalog to page 1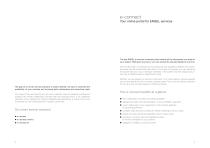
The goal of our smart service solutions is clearly defined: we want to maximise the availability of your machine and minimise both maintenance and downtime costs. Our range of services extends from an online customer portal to predictive maintenance systems and remote maintenance services with fast response times. If an unplanned downtime occurs despite this, fast and straightforward assistance is critical. This is why we provide you with professional 24/7 support, world-wide. Our smart service solutions: ■ e-connect ■ e-connect.monitor ■ e-connect.24 The free ENGEL e-connect customer...
Open the catalog to page 2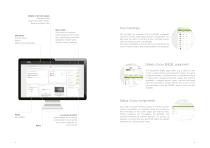
Details of service cases Service tickets Spare parts offers/orders Service engineer calls Machinery Current status Alarms Machine documentation Quick links Direct links to important areas/functions in the portal (e.g. checking the price and availability of spare parts, sending service requests) Your machinery You are given an overview of all your ENGEL equipment (machines, robots, stand-alone solutions, peripherals). You ■** also have the option of naming all your machines individually and organising them accordingly. If you also use ENGEL e-connect.24 for your machines, the ____ current...
Open the catalog to page 3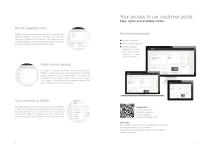
Your access to our customer portal Easy, quick and available online Price & availability check ENGEL gives you quick and easy access to all spare parts offered by ENGEL or to all the information you may need from your machine’s bill of materials. The prices are automatically displayed, including individual special conditions. It is also possible to request quotations directly. Technical requirements: Internet connection EDGE Device (optional) operating system: Windows 7 or newer OS X 10.5 or newer Android 4.4 or newer iOS 8.0 or newer Online service requests In cases of machine downtime,...
Open the catalog to page 4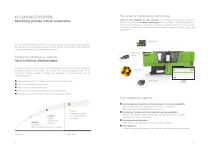
e-connect.monitor Monitoring process-critical components Even the best self-adapting machines must be serviced to achieve their expected service life. Maintenance was previously based on fixed intervals in combination with production schedules developed by competent service teams. The future of maintenance starts today Listen to the heartbeat of your machine: The predictive maintenance systems in e-connect.monitor, the condition monitoring solution by ENGEL, mark the beginning of a new era in the maintenance and repair of injection moulding machines. It is now possible to monitor...
Open the catalog to page 5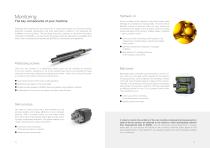
MonitoringThe key components of your machine Predicting the remaining life and service life of components helps you minimise planned downtime, schedule maintenance, and order spare parts in advance. This maximises the availability of your machines. The best thing about this, however, is that all the information collected in the ENGEL e-connect customer portal is perfectly organised and available at all times. Data is analysed automatically using ENGEL's infrastructure and algorithms. Plasticising screws Until now, the condition of a plasticising screw could only be checked by removing it...
Open the catalog to page 6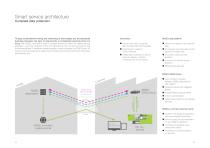
Through comprehensive linking and networking of technologies and the associated business processes, the topic of data security is increasingly becoming more of a focus. With ENGEL, your data is safe: Our system architecture meets the highest security standards - you have complete control and transparency over the data connections and the transferred data. A hardened operating system is used to operate the EDGE Device. All systems used are subjected to regular security tests and access is restricted to employees authorised by you. Connection ■ secure end-to-end connection with the latest...
Open the catalog to page 7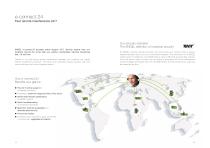
ENGEL e-connect.24 provides online support 24/7. Service experts from our locations around the world help you resolve unscheduled machine downtimes fast - at any time. Thanks to our cost-saving remote maintenance package, your machine can quickly resume trouble-free production. The result is an optimised support process and even more productivity with a short payback period. An ENGEL customer service technician can only access your machine when a service request has been sent by you or an authorised employee. The connection to the ENGEL central server is initiated by your EDGE Device using...
Open the catalog to page 8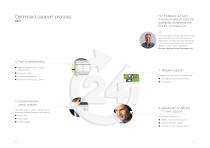
Huf (Hulsbeck & Furst) ensures maximum machine availability world-wide with ENGEL e-connect.24 24/74. Fast troubleshooting ■ initiate troubleshooting or simply solve problems ■ full service history ■ close service request ■ disconnect from ENGEL server U With this project, we can see how the new solutions help us to not only reduce our travel times, but also and most importantly improve our overall productivity. All of this makes us much more competitive." Dirk Horn, Corporate Process Technology at Huf 1. Request support Operator can send service request from ■ a PC/laptop/tablet/mobile...
Open the catalog to page 9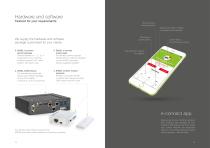
Hardware and software Tailored for your requirements View and send service request Service technician currently connected to the machine We supply the hardware and software package customised for your needs: 3. ENGEL e-connect service package Choose between a 1-, 2-, 3- or 5-year plan for your machine, including unlimited 24/7 online support, 365 days a year. screen page For sending a service request directly from the machine. Standard on new ENGEL machines; optional upgrades available. 2. ENGEL EDGE Device The user-friendly plug & play solution with software package for your PC or laptop....
Open the catalog to page 10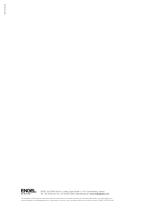
ENGEL AUSTRIA GmbH | Ludwig-Engel-Straße 1 | 4311 Schwertberg, Austria Tel. +43 50 620 0 | Fax +43 50 620 3009 | sales@engel.at | www.engelglobal.com The information, product features and pictures contained in this brochure are intended exclusively as a technical guide. ENGEL is not responsible for any technical changes or print/typographical errors . Reproduction in whole or in part is prohibited without the prior written consent of ENGEL AUSTRIA GmbH.
Open the catalog to page 11All ENGEL AUSTRIA GmbH catalogs and technical brochures
-
press | release
4 Pages
-
ENGEL services
9 Pages
-
Plasticising unit
15 Pages
-
Composite Technologies
13 Pages
-
combimelt
15 Pages
-
automotive
19 Pages
-
Amorphous Metal Moulding
5 Pages
-
smart machine
15 Pages
-
Automation
41 Pages
-
engel AUTOMATIUON
15 Pages
-
ENGEL INSERT
15 Pages
-
Trining
11 Pages
-
protect
3 Pages
-
iQ weight control
2 Pages
-
Engel Flomo
16 Pages
-
Scope of products
29 Pages
-
CC300
7 Pages
-
e-motion 30 TL
8 Pages
-
ENGEL plus
2 Pages
-
ENGEL e-cap
3 Pages
-
ENGEL e-mac
11 Pages
-
ENGEL elast
11 Pages
-
ENGEL insert PRO
7 Pages
-
ENGEL combimelt
5 Pages
-
Customized Soft-Touch
3 Pages
-
Engel EXJECTION®
4 Pages
-
ENGEL e-factory
4 Pages
Archived catalogs
-
e-motion TL
9 Pages
-
ENGEL e-victory
17 Pages
-
ENGEL e-motion
17 Pages
-
ENGEL duo
19 Pages
-
ENGEL victory
15 Pages
-
ENGEL Control
8 Pages
-
ENGEL VIPER
13 Pages
-
speed injection moulding machine
10 Pages