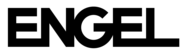
Catalog excerpts
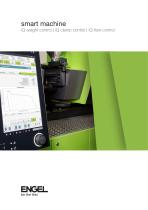
c°ntrol 1 iQfbw control Smart machine Q We’ght c°'nrol I iQ clamp
Open the catalog to page 1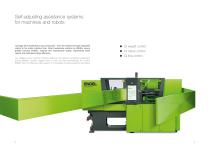
Self-adjusting assistance systems for machines and robots Leverage the full potential of your production – from the machine through integrated robots to the entire machine floor. Smart assistance systems by ENGEL ensure greater process stability, superior and reproducible quality, significantly fewer rejects and optimised energy efficiency. Our intelligent smart machine solutions determine the optimum production parameters during operation, actively suggest them or even set them automatically. As a result, ENGEL inject 4.0 offers you ideal support for increasingly complex production...
Open the catalog to page 2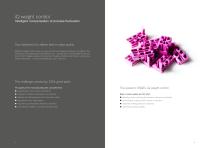
Your objective is to deliver best-in-class quality. ENGEL iQ weight control helps you keep control over all external production conditions. This smart piece of software does the thinking for you - shot by shot. It compensates for fluctuations in both material quality and the injection moulding machine environment - without any manual intervention, in a fully automated way, and in real-time. The challenge: producing 100% good parts The quality of the manufactured parts can suffer from: ■ material batch and moisture fluctuations ■ changes in ambient temperature and humidity ■ different...
Open the catalog to page 3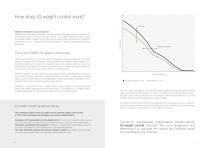
How does iQ weight control work? Maximum precision for your production ENGEL injection moulding machines are perfectly equipped for your production requirements. They achieve optimum process precision thanks to accurately repeatable screw position and speed. ENGEL iQ weight control takes this one step further and ensures a constant fill volume shot for shot – independent of external influences – therefore guaranteeing constant part quality. Material quantity This is how ENGEL iQ weight control works The actual fill volume can vary in the injection process due to external influences: the...
Open the catalog to page 4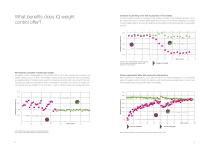
What benefits does iQ weight control offer? Constant mould filling even with fluctuations in the material In case of batch changes or changes in the moisture content of the material, flashed or short shot parts often occur. Injection parameters would need to be manually readjusted. iQ weight monitor reliably detects viscosity fluctuations and iQ weight control automatically compensates for them. Permanently consistent moulded part weight iQ weight control compensates for fluctuations shot by shot, and reduces the moulded part weight variance by up to 85%. The intelligent software still pays...
Open the catalog to page 5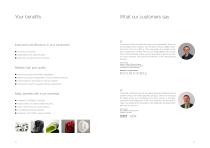
Your benefits What our customers say Improved cost-efficiency in your production ■ improves productivity ■ significantly fewer defective parts ■ faster start-up after machine downtime (( The results of the test series are clear-cut and repeatable. Thanks to the iQ weight control software, we were able to reduce weight fluctuations from 0.02 g to 0.003 g. This is equivalent to a weight consistency improvement of 85%. We are now totally satisfied with a reject rate of 0.047%. Based on this, we have been able to reduce the quality control overhead, and improve the efficiency of the...
Open the catalog to page 6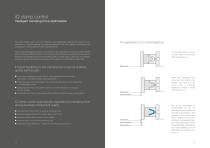
The tiniest details, such as mould breathing, can substantially influence the quality of your production. In mould breathing, the opening pressure of the melt partially compensates the compression of the mould due to the clamping force. If the mould breathing is too great or to small, this can cause rejects due to burn marks (diesel effect) or flashes. ENGEL iQ clamp control determines the optimum clamping force quickly and therefore automatically keeps mould breathing within the ideal range. In this way, the intelligent software supports the operator and ensures the quality of your...
Open the catalog to page 7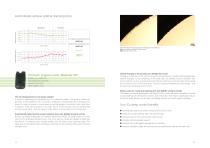
Automatically achieve optimal clamping force Shot counter Configured clamping force 5000 kN Optimised clamping force 4000 kN Transmitted light microscope pictures of the edge of a moulded part. Left: burr formation without iQ clamp control Right: with iQ clamp control. Shot counter Product: Engine cover; Material: PP ENGEL duo 4400/700 Clamping force 4000 kN Injection unit 4400 Shot weight 510 g The full clamping force is not always needed In practice, optimising the clamping force is a subjective matter: The result is heavily dependent on the experience of the operator. Setting an...
Open the catalog to page 8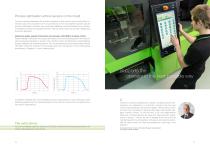
Process optimisation without sensors on the mould Common process parameters like injection pressure or melt cushion only provide limited information about the processes in the mould. Sensors on the mould deliver important data for process optimisation. However, they cause high additional costs and therefore only a fraction of all injection moulds are equipped with them. With iQ clamp control, we provide a reliable and economic alternative. Supports the operator in the best possible way Determine quality-relevant information economically with ENGEL iQ clamp control Receive relevant...
Open the catalog to page 9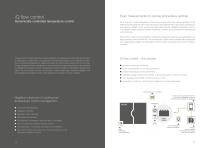
Dynamically controlled temperature control Exact measurements for precise temperature settings For a long time, mould temperature control was a process which was mainly orientated on the defined flow temperature at the mould and which was adjusted with a great deal of experience and patience, ENGEL flomo was the first major step towards intelligent temperature control. The intelligent water distribution system measures, monitors and documents the temperature control process. With e-flomo it was not only possible to measure the temperature and process parameters, but also to actively control...
Open the catalog to page 10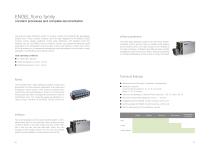
The optimum water distribution system for cooling moulds and managing their temperature: ENGEL flomo. These compact modules, which are fully integrated into the ENGEL CC300 machine control, replace traditional cooling water distributors with floatation body flow metering. You can use ENGEL flomo to measure, monitor, log important temperature control parameters of the temperature control process; e-flomo even features a closed loop control. All of this enables you to manage the temperature control processes of your moulds in a safe, repeatable, time-efficient and convenient manner. ideal...
Open the catalog to page 11All ENGEL AUSTRIA GmbH catalogs and technical brochures
-
press | release
4 Pages
-
ENGEL services
9 Pages
-
Plasticising unit
15 Pages
-
Composite Technologies
13 Pages
-
combimelt
15 Pages
-
automotive
19 Pages
-
Amorphous Metal Moulding
5 Pages
-
smart service
11 Pages
-
Automation
41 Pages
-
engel AUTOMATIUON
15 Pages
-
ENGEL INSERT
15 Pages
-
Trining
11 Pages
-
protect
3 Pages
-
iQ weight control
2 Pages
-
Engel Flomo
16 Pages
-
Scope of products
29 Pages
-
CC300
7 Pages
-
e-motion 30 TL
8 Pages
-
ENGEL plus
2 Pages
-
ENGEL e-cap
3 Pages
-
ENGEL e-mac
11 Pages
-
ENGEL elast
11 Pages
-
ENGEL insert PRO
7 Pages
-
ENGEL combimelt
5 Pages
-
Customized Soft-Touch
3 Pages
-
Engel EXJECTION®
4 Pages
-
ENGEL e-factory
4 Pages
Archived catalogs
-
e-motion TL
9 Pages
-
ENGEL e-victory
17 Pages
-
ENGEL e-motion
17 Pages
-
ENGEL duo
19 Pages
-
ENGEL victory
15 Pages
-
ENGEL Control
8 Pages
-
ENGEL VIPER
13 Pages
-
speed injection moulding machine
10 Pages