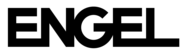
Catalog excerpts
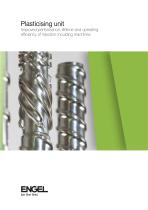
Plasticising unit Improved performance, lifetime and operating efficiency of injection moulding machines
Open the catalog to page 1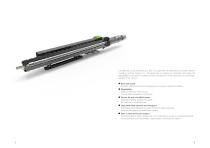
It all depends on the plasticising unit. Both the quality and the performance of modern injection moulding machines depend on it. The plasticising unit defines the achievable melt quality, the repeatability of the injection moulding process, and above all, the life expectancy and cost-effectiveness of the machine. ■ Best melt quality Excellent material and thermal homogeneity for a variety of process conditions. ■ Repeatability Maximum precision. Shot by ■shot. Through highly-developed components. ■ Service life and cost effectiveness Application-specific material executions. For maximum...
Open the catalog to page 2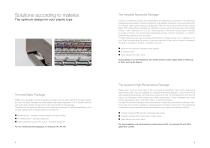
Solutions according to material The optimum design for your plastic type The versatile Advanced Package Thanks to a hardening process and welded flights, the plasticising components in the Advanced Package achieve excellent corrosion resistance, high abrasion resistance, and a long service life. For example, large screws, starting at a diameter of 80 mm, are produced with premium welded flights: PTA welding (Plasma-Transfer-Arc-Welding) is used to weld a hard alloy layer onto the flight surface – with a thickness of 1 to 2 mm. Wear protection in the screw channel base is ensured by a layer...
Open the catalog to page 3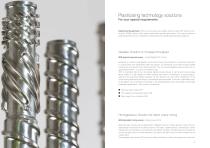
Plasticising technology solutions For your special requirements Determined by geometry. While 3-zone screws are versatile, barrier screws offer maximum productivity. ENGEL offers a wide range of application-specific geometries. They ensure maximum plasticising performance, impressive mixing quality and outstanding plasticising capacity. Versatile: Solution to increase throughput SPS (special purpose screw) – double-flighted G2.3 screw Advances in mould and temperature control technology have resulted in a continuous reduction in cooling times and significantly higher throughput, by...
Open the catalog to page 4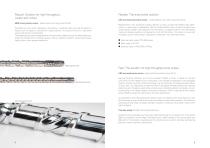
Robust: Solution for high throughput, output and colour Flexible: The automotive solution UAS (universal automotive screw) – double-flighted screw with mixing head (G18) MBS (mixing barrier screw) – Barrier screw with mixing head (G16S) Polyolefins can pose major challenges in processing, in particular where very high throughput is required and the plastic is coloured with master batches. The solution for this is to use barrier screws with dynamic mixing heads. The engineering principle of separating the solid and molten material through the barrier flight guarantees the highest level of...
Open the catalog to page 5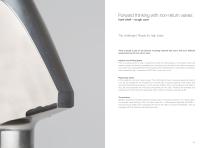
Forward thinking with non-return valves hard shell – tough core The challenge | Ready for high loads There is hardly a part on the injection moulding machine that has to fulfil such different requirements as the non-return valve: Injection and holding phase From a functional point of view, it prevents the melt from flowing back in the injection and hold pressure phase. Achieving a repeatable shut-off behaviour at the start of the injection process is one of the most critical parameters for the quality of the moulded parts. In this phase, the dynamic load is extremely high – pressures of...
Open the catalog to page 6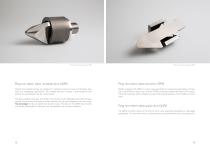
Ring non-return valve universal-shut UNR9 Ring non-return valve universal-shut UNR9 Ring non-return valve universal-shut UNR9 Ring non-return valve opt-shut OPR9 Carbide hard material phases are designed to withstand maximum stress and therefore best meet very challenging requirements. This material execution includes a laser-alloyed tip that reduces the wear between the tip and the sleeve. ENGEL developed the OPR9 non-return valve specifically for crystal clear applications. Compared to the UNR9 non-return valve, all of the OPR9’s components additionally have a PVD coating. This further...
Open the catalog to page 7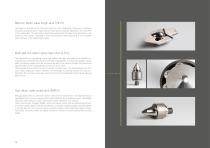
Ball non-return valve tough-shut TOR10 The larger the diameter of the non-return valve, the more challenging it becomes to achieve a very good closing behaviour. Highly-precise mould filling is essential, especially in the production of thin-walled parts. The best way to meet these requirements for larger screw diameters is with a ball non-return valve – especially if screw decompression after plasticising is not a possible option because of the required part quality. Multi-ball non-return valve clear-shut CLR12 The requirements for processing crystal clear plastics with high shot weights...
Open the catalog to page 8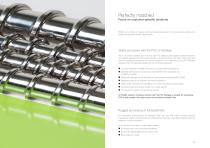
Perfectly matchedFocus on costumer-specific solutions ENGEL can provide, on request, optimised plasticising systems that are precisely tailored to a variety of application specific requirements. Stable processes with the PVC-U Package PVC-U dry blend or pellets, also known as rigid PVC, belong to those plastics classes that pose very special requirements for the entire injection moulding machine. Low shear, high torque and chemical resistance characterise the machine equipment. The modifications of the PVC Package perfectly cover the demands plaqced on the machine's equipment. ■...
Open the catalog to page 9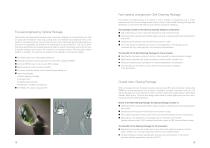
Focused engineering: Optical Package Optical parts with large wall thicknesses pose a particular challenge for the plasticising unit. After all: Large wall thicknesses mean long cooling times and therefore long residence times of the plastic in the plasticising unit, the hot runner and the mould. Particularly gentle melting behaviour and best homogenisation are therefore the prerequisites for lens production. The use of optimised screw geometries and material executions helps to extend the process window for the user. If required, material can be fed to the machine in a controlled manner....
Open the catalog to page 10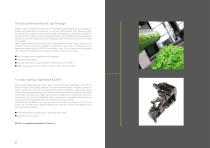
The fast performer with the Cap Package Maximum speed, dynamics and performance: The ENGEL speed plasticising unit is designed for durable high-performance from beginning to end. Fast rotating screws, short strokes and fast, precise injection; all system components are capable of handling the most extreme demands and are ideally suited for intensive use in the packaging industry. The G16CAP barrier screw is specially designed to meet the requirements of the packaging industry in the manufacture of PE-HD caps for beverages. High-strength material execution, paired with a sophisticated...
Open the catalog to page 11All ENGEL AUSTRIA GmbH catalogs and technical brochures
-
press | release
4 Pages
-
ENGEL services
9 Pages
-
Composite Technologies
13 Pages
-
combimelt
15 Pages
-
automotive
19 Pages
-
Amorphous Metal Moulding
5 Pages
-
smart service
11 Pages
-
smart machine
15 Pages
-
Automation
41 Pages
-
engel AUTOMATIUON
15 Pages
-
ENGEL INSERT
15 Pages
-
Trining
11 Pages
-
protect
3 Pages
-
iQ weight control
2 Pages
-
Engel Flomo
16 Pages
-
Scope of products
29 Pages
-
CC300
7 Pages
-
e-motion 30 TL
8 Pages
-
ENGEL plus
2 Pages
-
ENGEL e-cap
3 Pages
-
ENGEL e-mac
11 Pages
-
ENGEL elast
11 Pages
-
ENGEL insert PRO
7 Pages
-
ENGEL combimelt
5 Pages
-
Customized Soft-Touch
3 Pages
-
Engel EXJECTION®
4 Pages
-
ENGEL e-factory
4 Pages
Archived catalogs
-
e-motion TL
9 Pages
-
ENGEL e-victory
17 Pages
-
ENGEL e-motion
17 Pages
-
ENGEL duo
19 Pages
-
ENGEL victory
15 Pages
-
ENGEL Control
8 Pages
-
ENGEL VIPER
13 Pages
-
speed injection moulding machine
10 Pages