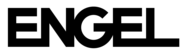
Catalog excerpts
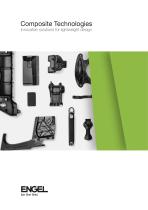
Composite Technologies Innovative solutions for lightweight design
Open the catalog to page 1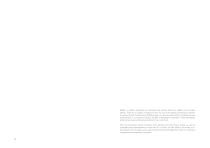
ENGEL is globally recognised by customers and partners alike as a reliable and innovative partner. There are a number of reasons for this. As one of the leading companies in injection moulding machine manufacturing, ENGEL’s goal is to take new paths and to constantly provide developments in our industry including the field of lightweight composites. These trail-blazing enhancements are exciting advancements for our customers. With nine production plants in Europe, North America and Asia (China, Korea), as well as subsidiaries and representatives in more than 85 countries, we offer tailored,...
Open the catalog to page 2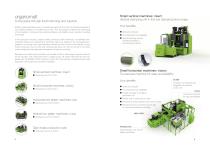
Composites through thermoforming and injection ENGEL organomelt allows you to manufacture parts with the best mechanical properties at low weights creating a cost effective process. This technology combines the processing of thermoplastic, continuous fibre-reinforced blanks with ENGEL proven injection moulding technology. In the production process, organic sheets (continuous fibre-reinforced, consolidated thermoplastic blanks) and unidirectional reinforced tapes are heated to the processing temperature in an energy- and cycle-optimised method and then formed in the injection mould. Further...
Open the catalog to page 3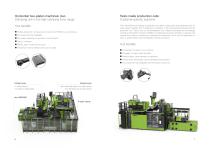
Horizontal two-platen machines: duo Clamping unit in the high clamping force range Tailor-made production cells Customer-specific solutions Your benefits The most efficient part design is essential to be able to create parts at an attractive price. In many cases, however, this increases the complexity of the manufacturing process and the production cell. Topics such as functionalisation and multiple thicknesses are increasingly coming to the forefront. Thanks to ENGEL’s comprehensive product portfolio, customers can choose from various modules and customise the production cell to suit the...
Open the catalog to page 4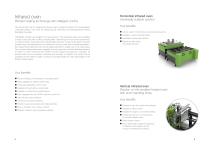
Infrared oven Efficient heating technology with intelligent control The critical factor for the organomelt process chain is optimal heating of the thermoplastic composite blanks. They must be heated quickly, efficiently and homogeneously without damaging the plastic. The ENGEL infrared oven adapts to the requirements of the respective parts and is available in various sizes and with or without a sliding table. Depending on the process requirements, we offer you both a horizontal and a vertical heating concept. To heat up the parts in the best possible way, the heating field can be divided...
Open the catalog to page 5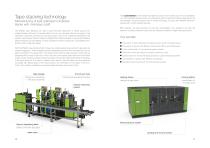
Tape stacking technology The consolidation of the locally fixed layer structure is then carried out in the consolidation unit. The heating/cooling process in combination with the special tool technology allows the consolidation of layer structures with a uniform thickness, but also with different wall thicknesses with minimal residual porosity. Manufacturing of load optimised composite blanks with minimized cutoff The ENGEL tape stacking unit uses a pick-and-place approach to create layups from unidirectionally reinforced composite tapes that can be precisely placed according to the...
Open the catalog to page 6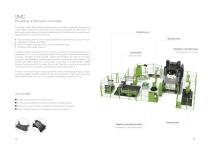
Processing of thermoset composites Processing of SMC (Sheet Moulding Compound) is particularly suitable for the production of flat visible components as well as structural components exposed to high stress. The technology enables extensive functional integration and is therefore used for a wide range of high-performance composite components. • • • • Unwinding unit Handling robot Fully automated system solution for best repeatability and dimensional accuracy of the part Realisation of complex geometries Additional features possible as ribs, inserts or duroplastic tapes Paintable surface...
Open the catalog to page 7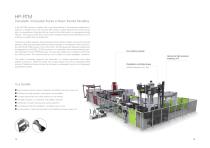
Duroplastic composites thanks to Resin Transfer Moulding In the HP-RTM process, a preform with a ply setup tailored to the respective application is placed in a heated mould. The mould is then closed. A highly reactive resin (mostly epoxy resin or polyurethane) is injected into the mould and the fibre preform is impregnated during injection. The reactive matrix then cures under increased pressure and temperature to form a strong an durable fibre composite part. Thanks to its system expertise and extensive product portfolio, ENGEL, along with renowned partners, offers fully automated systems...
Open the catalog to page 8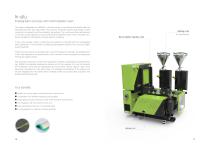
Impregnation process with thermoplastic resin The range of applications for ENGEL in-situ technology is very diverse and ideally suited for structural parts that face high stress. The process combines reactive technology for fibre composite components with thermoplastic processing. The continuous-fibre reinforcement on the part can be tailored to the load while the thermoplastic matrix of the composite component enables functionalisation through injection moulding. Melting units for Caprolactam Servo-electric injection units In the in-situ process, carbon or glass fibre are inserted in a...
Open the catalog to page 9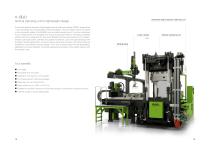
Hennecke high-pressure metering unit To meet the specific demands of lightweight products and its processes, ENGEL designed the v-duo specifically for processing fibre-reinforced plastics. The low-height machine is based on the successful design of the ENGEL duo two-platen clamping unit. It can be customised to your needs thanks to its versatility and choice of equipment options. The easily accessible vertical machine is equipped with the proven ENGEL ecodrive drive solution and is characterised by precisely profile-controlled and parallel movements. Due to the optional design with a single...
Open the catalog to page 10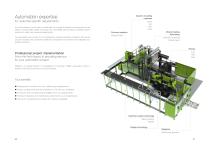
Automation expertise Injection moulding machines for customer-specific requirements If you are looking for more than a combination of modular automation components such as robots, conveyor belts, safety enclosures, etc., the ENGEL team is happy to develop system solutions to meet your individual requirements. Our specialists have access to a comprehensive modular assembly kit system with proven process modules; they implement additional components and functions and integrate your preferred devices. victory duo v-duo insert Infrared heating technology Conveyor systems Conveyor belt Vertical...
Open the catalog to page 11All ENGEL AUSTRIA GmbH catalogs and technical brochures
-
press | release
4 Pages
-
ENGEL services
9 Pages
-
Plasticising unit
15 Pages
-
combimelt
15 Pages
-
automotive
19 Pages
-
Amorphous Metal Moulding
5 Pages
-
smart service
11 Pages
-
smart machine
15 Pages
-
Automation
41 Pages
-
engel AUTOMATIUON
15 Pages
-
ENGEL INSERT
15 Pages
-
Trining
11 Pages
-
protect
3 Pages
-
iQ weight control
2 Pages
-
Engel Flomo
16 Pages
-
Scope of products
29 Pages
-
CC300
7 Pages
-
e-motion 30 TL
8 Pages
-
ENGEL plus
2 Pages
-
ENGEL e-cap
3 Pages
-
ENGEL e-mac
11 Pages
-
ENGEL elast
11 Pages
-
ENGEL insert PRO
7 Pages
-
ENGEL combimelt
5 Pages
-
Customized Soft-Touch
3 Pages
-
Engel EXJECTION®
4 Pages
-
ENGEL e-factory
4 Pages
Archived catalogs
-
e-motion TL
9 Pages
-
ENGEL e-victory
17 Pages
-
ENGEL e-motion
17 Pages
-
ENGEL duo
19 Pages
-
ENGEL victory
15 Pages
-
ENGEL Control
8 Pages
-
ENGEL VIPER
13 Pages
-
speed injection moulding machine
10 Pages